CNC Metal
- Exceptional Corrosion and Fatigue Resistance: Ideal for aerospace and medical industries.
- Precision:0.001mm
- Fast Turnaround Times: Receive your parts in just 1-7 days
- Certified Quality: ISO9001:2015 and IATF16949 certified processes for top-quality results.

Custom Metal CNC Parts
CNC machined metals are essential in various industries, from aerospace to medical. At Modo Rapid, we offer a wide range of alloys for on-demand custom manufacturing. Explore each category below to learn more about specific alloys and their properties. Click on each category for detailed information on the available materials.
Common Metal Alloys
CNC machining Invar
- Invar 36: Low thermal expansion, perfect for aerospace and precision instruments.
- Super Invar: Even lower thermal expansion, used in optical and measurement instruments.
- Invar 42: Balanced properties for various industrial applications.
- Invar 48: Higher nickel content for specialized applications requiring unique properties.
CNC Machining Copper
- C110 (Electrolytic Tough Pitch Copper)
- C101 (Oxygen-Free Copper)
- C145 (Tellurium Copper)
- C182 (Chromium Copper)
- C172 (Beryllium Copper)
- C464 (Naval Brass)
- 6061: Offers excellent mechanical properties and corrosion resistance, perfect for structural applications, automotive parts, and consumer goods.
- 7075: Known for high strength and toughness, suitable for aerospace and high-performance engineering.
- 2024: Provides high strength and fatigue resistance, commonly used in aerospace and military applications.
- 5052: Highly corrosion-resistant, ideal for marine and chemical environments.
- 6063: Excellent extrudability and surface finish, commonly used in architectural applications.
CNC Machining Steel
Stainless Steel:
- 304 Stainless Steel
- 316 Stainless Steel
- 17-4 PH Stainless Steel
Carbon Steel:
- 1018 Carbon Steel
- 1045 Carbon Steel
- A36 Carbon Steel
Alloy Steel
- 4140 Alloy Steel
- 4340 Alloy Steel
Tool Steel
- D2 Tool Steel
- O1 Tool Steel
- A2 Tool Steel
- Inconel 600: Excellent oxidation and corrosion resistance, suitable for high-temperature and high-stress environments.
- Inconel 601: Outstanding resistance to heat and oxidation, commonly used in thermal processing applications.
- Inconel 625: Superior strength and toughness, ideal for aerospace and marine applications.
- Inconel 718: High strength and corrosion resistance, widely used in the aerospace and oil & gas industries.
- Inconel X-750: Excellent creep-rupture strength, used in high-temperature structural applications.
- Inconel 617: Combines good oxidation and corrosion resistance with excellent high-temperature strength.
Comprehensive List of Metal Part Finishes
Anodizing
- Creates a corrosion-resistant and decorative oxide layer.
- Available in various colors.
Powder Coating
- Provides a durable, high-quality finish.
- Available in a wide range of colors and textures.
Electroplating
- Adds a thin layer of metal coating for improved corrosion resistance and aesthetics.
- Common types include chrome, nickel, and zinc plating.
Polishing
- Achieves a smooth and shiny surface.
- Removes scratches and minor imperfections.
Brushing
- Produces a uniform, linear texture.
- Often used for aesthetic purposes.
Sandblasting
- Creates a matte, textured surface.
- Useful for cleaning and surface preparation.
Black Oxide
- Offers mild corrosion resistance and a black finish.
- Commonly used for tool and fastener applications.
Passivation
- Enhances the corrosion resistance of stainless steel.
- Removes free iron and other contaminants.
Laser Engraving
- Marks the surface with text, logos, or patterns.
- Provides high precision and durability.
Powder Coating
- Offers a thicker and more durable finish than traditional painting.
- Available in a variety of colors and finishes.
Electrophoresis
- Applies a uniform coating for corrosion resistance.
- Often used for automotive and appliance parts.
Chemical Etching
- Uses chemicals to create detailed designs or textures.
- Suitable for intricate patterns and fine details.
UV Coating
- Provides a clear, glossy finish.
- Offers protection against UV radiation and environmental damage.
Electropolishing
- Enhances the brightness and smoothness of metal surfaces.
- Removes a thin layer of material for a clean, polished finish.
Oxidation
- Forms a protective oxide layer.
- Can be colored to achieve different aesthetic effects.
Hot-Dip Galvanizing
- Dips metal parts in molten zinc for corrosion protection.
- Creates a thick, durable coating.
Powder Coating
- Electrostatically applied powder that is cured under heat.
- Provides a durable and high-quality finish.
Painting
- Applies liquid paint for color and protection.
- Available in various types and finishes.
PVD Coating (Physical Vapor Deposition)
- Deposits thin film coatings for wear resistance and aesthetics.
- Often used for decorative finishes and cutting tools.
Chemical Conversion Coating
- Enhances corrosion resistance and paint adhesion.
- Common types include chromate and phosphate coatings.
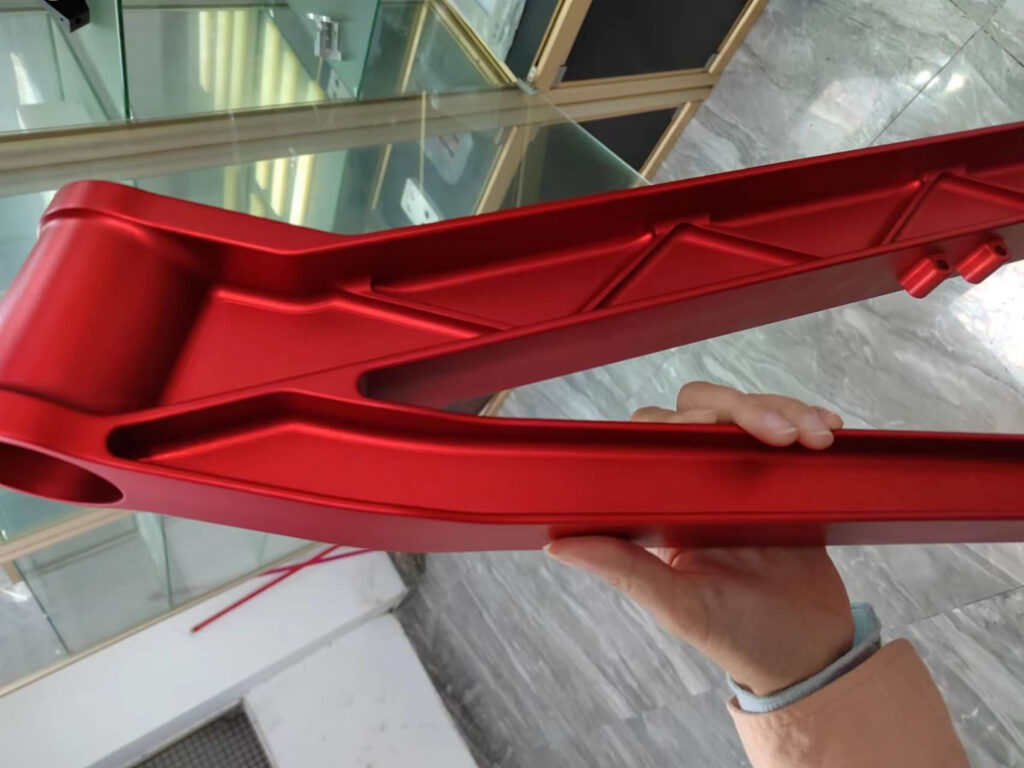
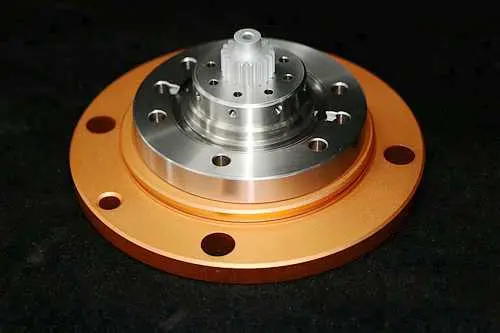
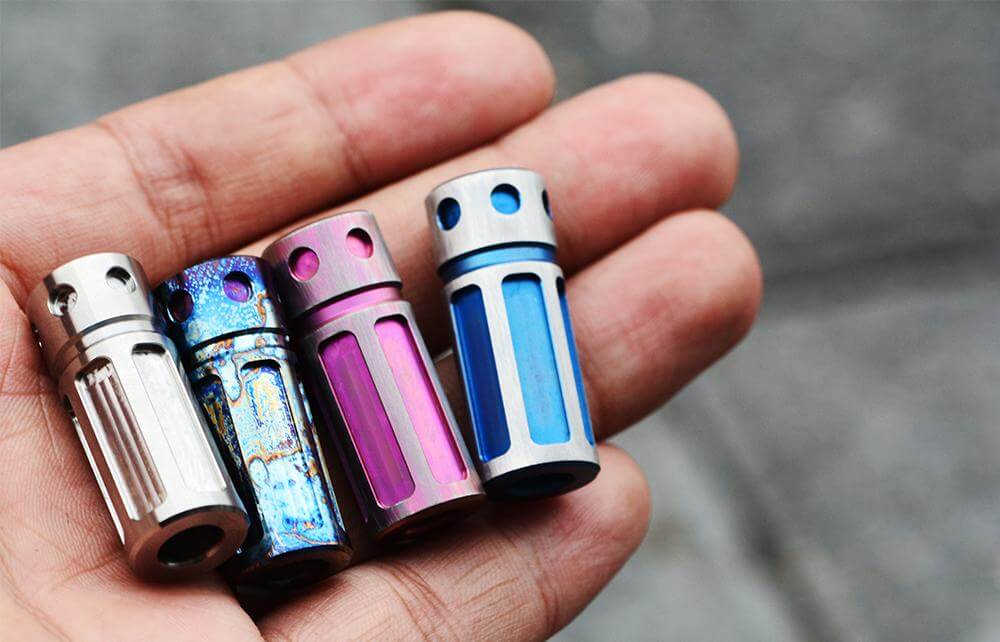

CNC Metal Machining Services
CNC metal machining is the process of transforming a raw piece of metal into a precise and desired shape or object. This is achieved with unparalleled accuracy using CNC (Computerized Numerical Control) machines, which can create almost any three-dimensional object designed through CAD (Computer Aided Design) software. At Modo Rapid, our skilled machinists utilize advanced 3- and 5-axis CNC machines to produce high-quality metal parts that meet our stringent DFM (Design for Manufacturability) checks. Our state-of-the-art CNC machines can craft intricate features on parts with exceptional precision, ensuring tight tolerances and superior quality for your projects.
Delivery Time
When selecting a supplier, it’s crucial to consider their production cycle and delivery capabilities, especially for urgent projects. Our commitment to timely delivery is unwavering, ensuring your project stays on track.
For prototypes, we offer the following delivery times:
- 1-30 pieces: Delivery within 7 days
- 31-100 pieces: Delivery within 15 days
- 100-500 pieces: Delivery within 18 days
We can reprioritize orders in case of project emergencies. Please let us know in advance.
Cost Control
We understand that cost efficiency is crucial when sourcing CNC prototypes. Our competitive pricing ensures that you get the best value without compromising on quality. Here’s how we keep costs low:
- Processing Fees: By utilizing advanced CNC machinery, we reduce production time and costs. For instance, our 5-axis milling can complete complex parts in fewer setups, saving both time and money.
- Material Costs: We have established relationships with top material suppliers, allowing us to procure high-quality materials at discounted rates. For example, our bulk purchasing of aluminum alloys translates to significant savings for our clients.
- Shipping Fees: Our strategic partnerships with leading logistics companies ensure efficient and cost-effective shipping. For instance, our expedited shipping options for urgent orders do not come with the high price tag you’d expect.
By choosing us, you’re guaranteed low-cost, high-quality CNC prototypes that meet your budget and performance requirements. For example, a recent project involving 50 custom parts was delivered within budget and ahead of schedule, demonstrating our commitment to cost efficiency and timely delivery.
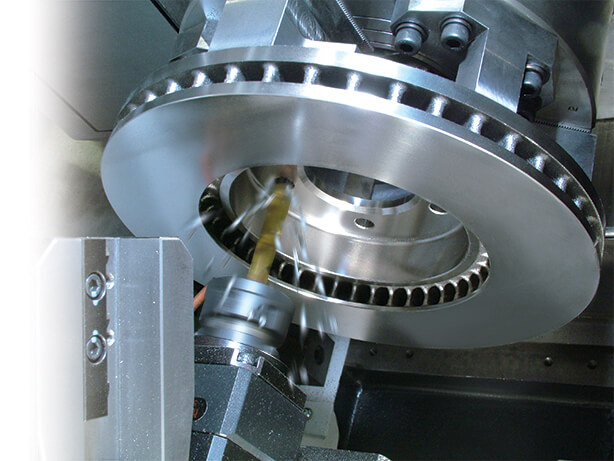
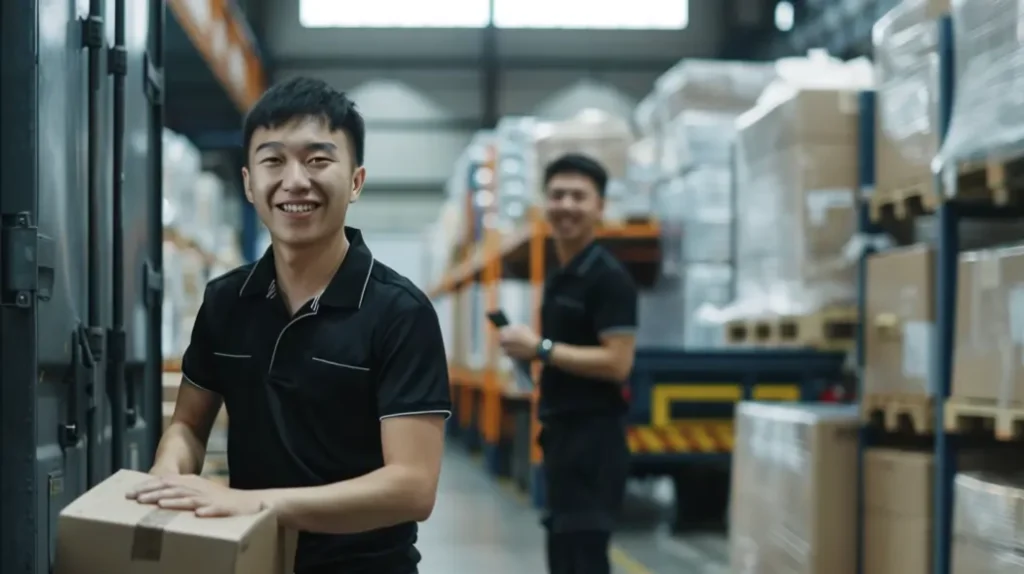
Communication Efficiency
Effective communication is key. We are online 16 hours daily, providing swift, expert support globally, ensuring seamless project management.
Flexibility
We specialize in prototypes and small batches, accommodating even single orders with flexible production and payment options.
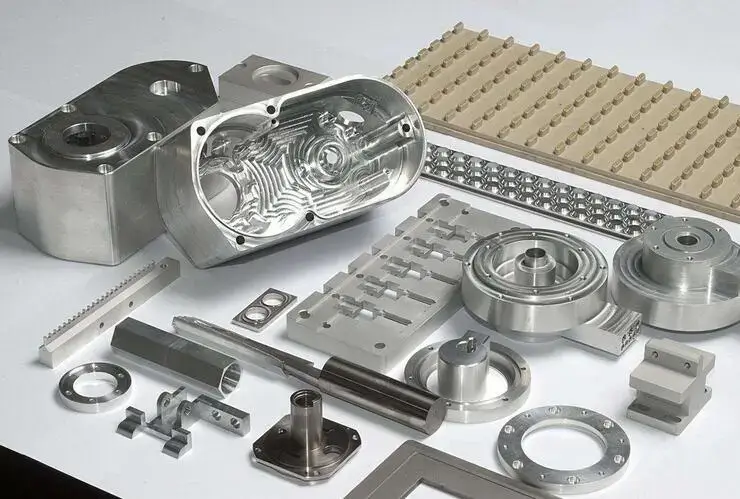
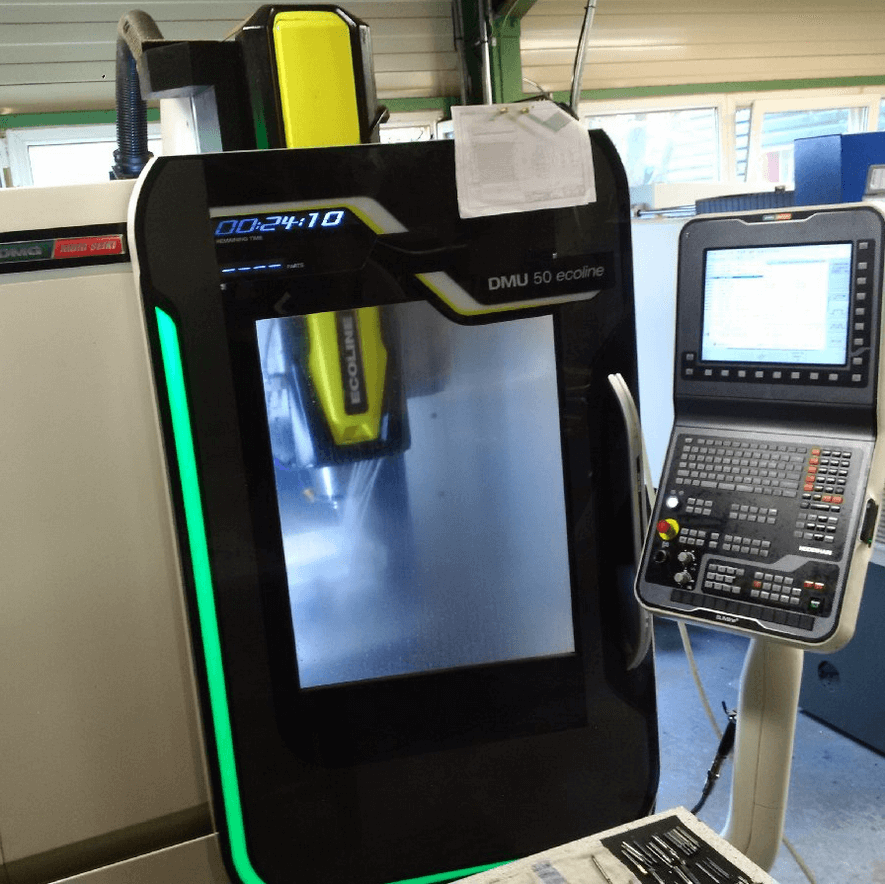
Confidentiality
We sign NDAs before discussing design details. Production occurs in temperature-controlled, sealed facilities.
Our employees and the company are also bound by confidentiality and non-compete agreements. The company and its employees are in a stable relationship to ensure that your designs are safe
What are the maximum part sizes and complex geometries you can handle?
- Part Sizes: We can machine parts with maximum dimensions of 1800mm x 800mm x 600mm, meeting the needs of most industrial applications.
- Complex Geometries: Our 5-axis and 4-axis CNC machining centers can precisely machine complex geometries, including internal channels, intricate surfaces, and high-precision apertures. Our equipment can manage fine features and tight tolerances, ensuring your design intentions are perfectly realized.
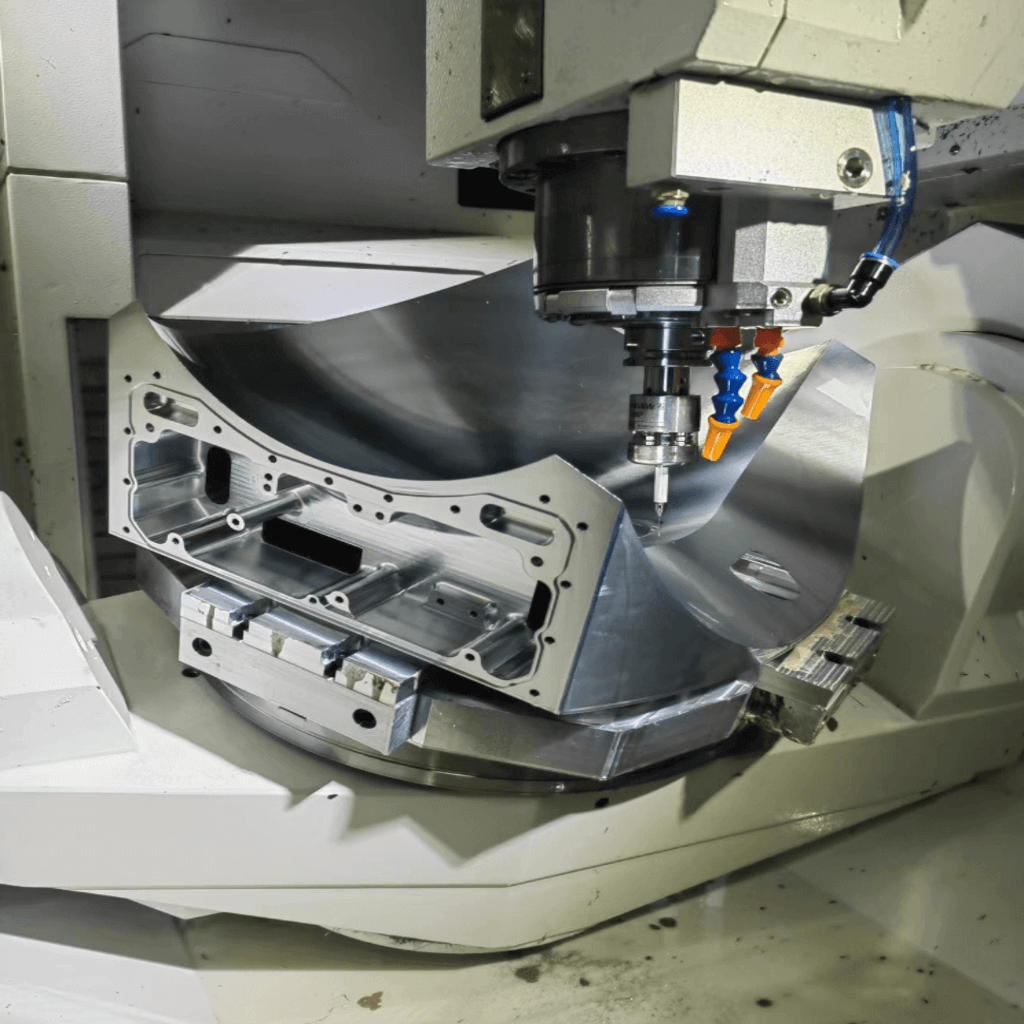
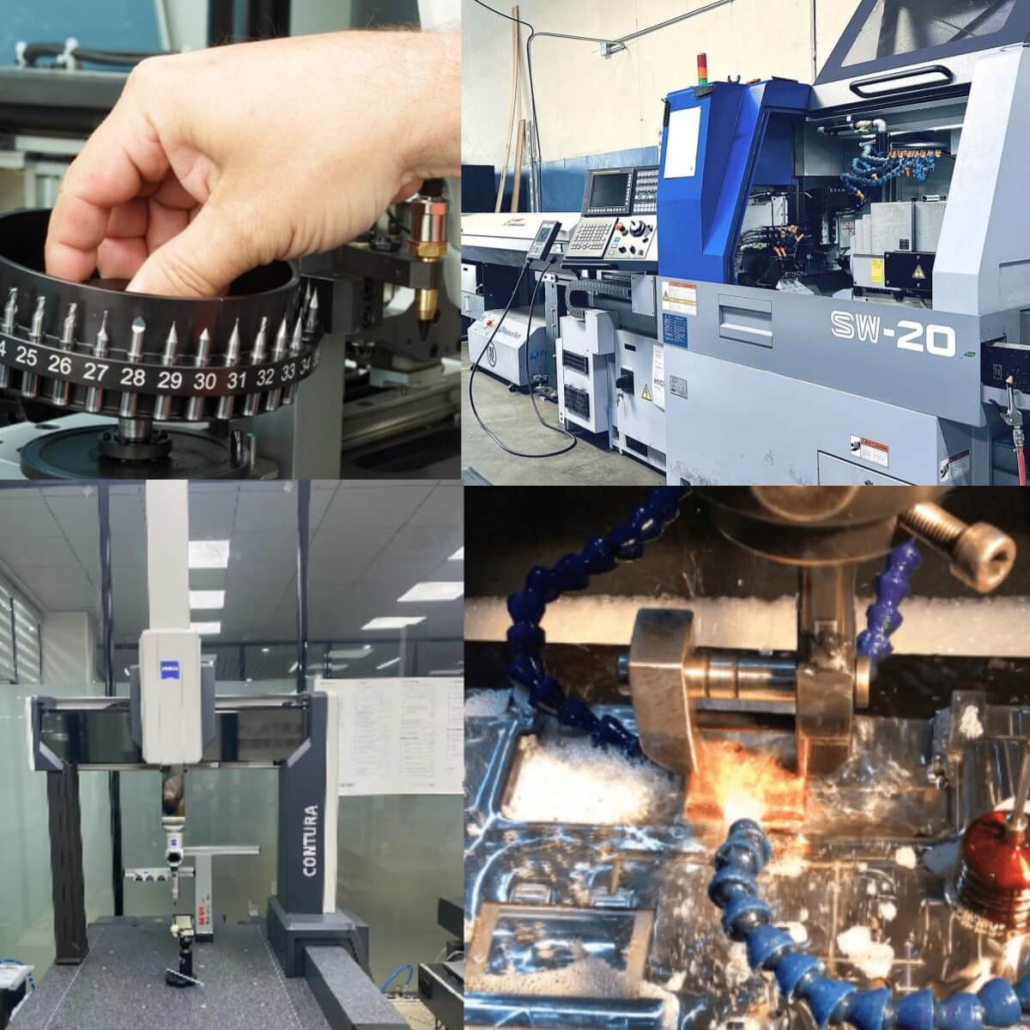
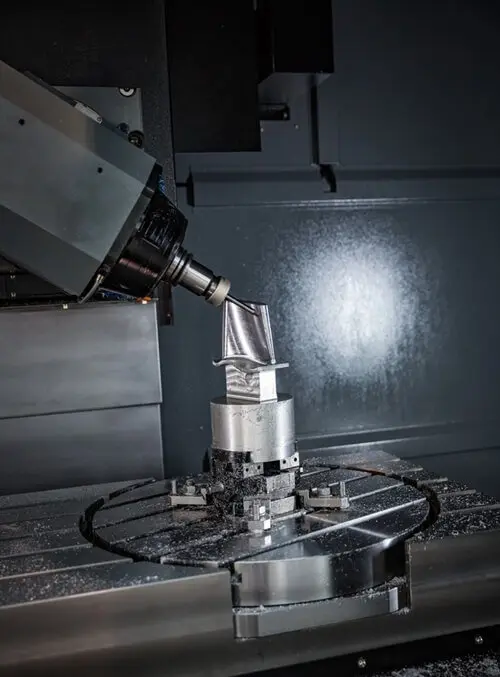
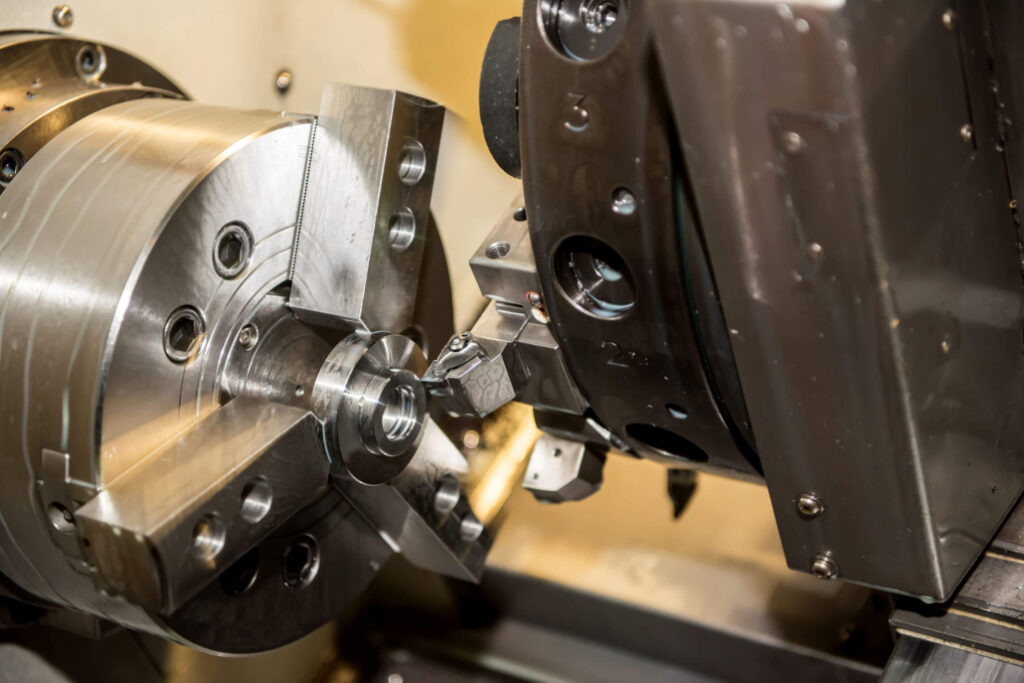
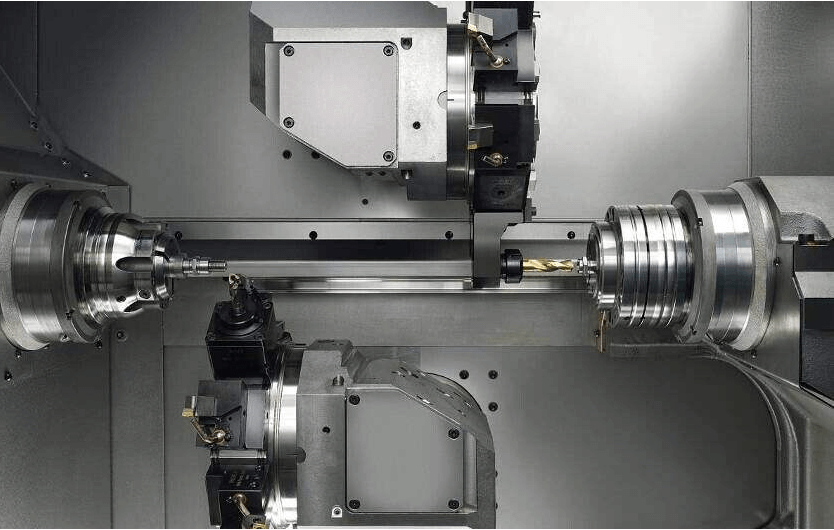
What advanced CNC equipment do you have for machining brass alloys?
- 5-Axis CNC Machining Centers: Capable of producing complex geometries and intricate designs, ensuring high accuracy and smooth finishes on brass components.
- High-Speed CNC Mills: Equipped with robust spindles and high feed rates, ideal for efficiently machining brass while maintaining tight tolerances.
- Multi-Tasking CNC Lathes: These machines combine milling and turning capabilities, allowing for versatile and efficient production of brass parts in a single setup.
- Precision CNC Grinders: Essential for achieving the fine surface finishes and exact dimensions required for high-performance brass components.
- EDM (Electrical Discharge Machining): Utilized for cutting intricate shapes and hard-to-machine areas, providing high precision without inducing stress in the brass material.
- Mill-turn machine: Combines turning and milling functions in one, completing complex multi-axis machining on a single setup. It improves accuracy and efficiency, ideal for high-precision parts. For brass alloy parts, its high rigidity and multi-axis capabilities reduce machining time and ensure quality. Using efficient tools and optimized parameters further enhances production speed and reliability.
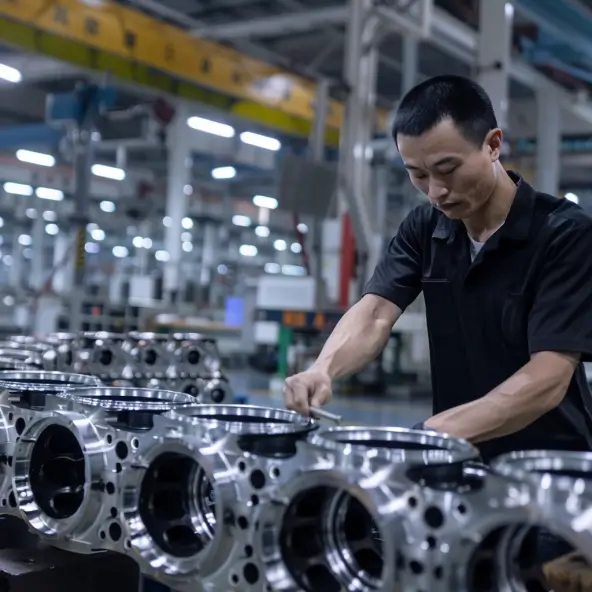
How Do We Deal With Your Expedited Orders?
Yes, we can shorten the production time for expedited orders. If you require faster delivery, please inform us at the time of order placement.
Expedited orders are subject to an additional fee and depend on the current production schedule and the complexity of the parts. By prioritizing your order, we can often reduce the lead time to 1-7 days.
Our team is committed to meeting your deadlines and ensuring that you receive your parts on time, even for urgent projects. Please contact us directly to discuss your specific requirements and expedited options.
How Do We Ensure Consistency and Quality for Each Batch of Parts?
Quality Control Measures:
Advanced Inspection Tools: Utilization of CMMs (Coordinate Measuring Machines), laser scanners, and precision gauges to measure critical dimensions and geometries.
In-Process Monitoring: Continuous monitoring during machining processes to detect and correct deviations in real-time.
Material Verification: Comprehensive material testing, including chemical composition and mechanical property analysis, to ensure conformity with specifications.
Surface Finish Analysis: Employing profilometers and other surface finish measurement tools to guarantee that all parts meet required surface quality standards.
Environmental Controls: Maintaining a controlled environment in production areas to minimize the impact of temperature and humidity variations on machining accuracy.
Ensuring Consistency and Quality for Each Batch:
Standard Operating Procedures (SOPs): Strict adherence to standardized processes for each operation to ensure uniformity across all production stages.
First Article Inspection (FAI): Conducting thorough inspections on the first piece of each batch to verify that it meets all specified requirements before proceeding with full-scale production.
Statistical Process Control (SPC): Applying SPC techniques to monitor and control the manufacturing process, ensuring that variations are kept within acceptable limits.
Lot Traceability: Implementing comprehensive traceability systems to track materials and processes for each batch, allowing for easy identification and resolution of any quality issues.
Final Inspection and Testing: Performing rigorous final inspections and functional tests on all parts before shipment to confirm that they meet client specifications and quality standards.
Our commitment to stringent quality control measures ensures that you receive consistent, high-quality parts in every batch, supporting your projects’ success and reliability.
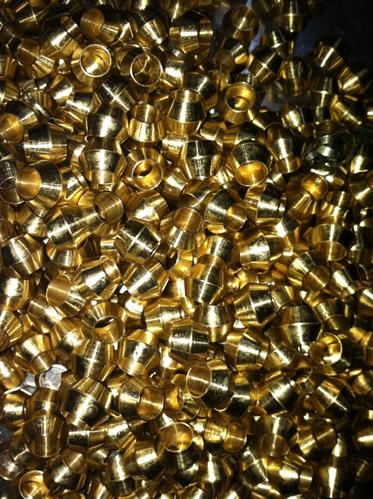

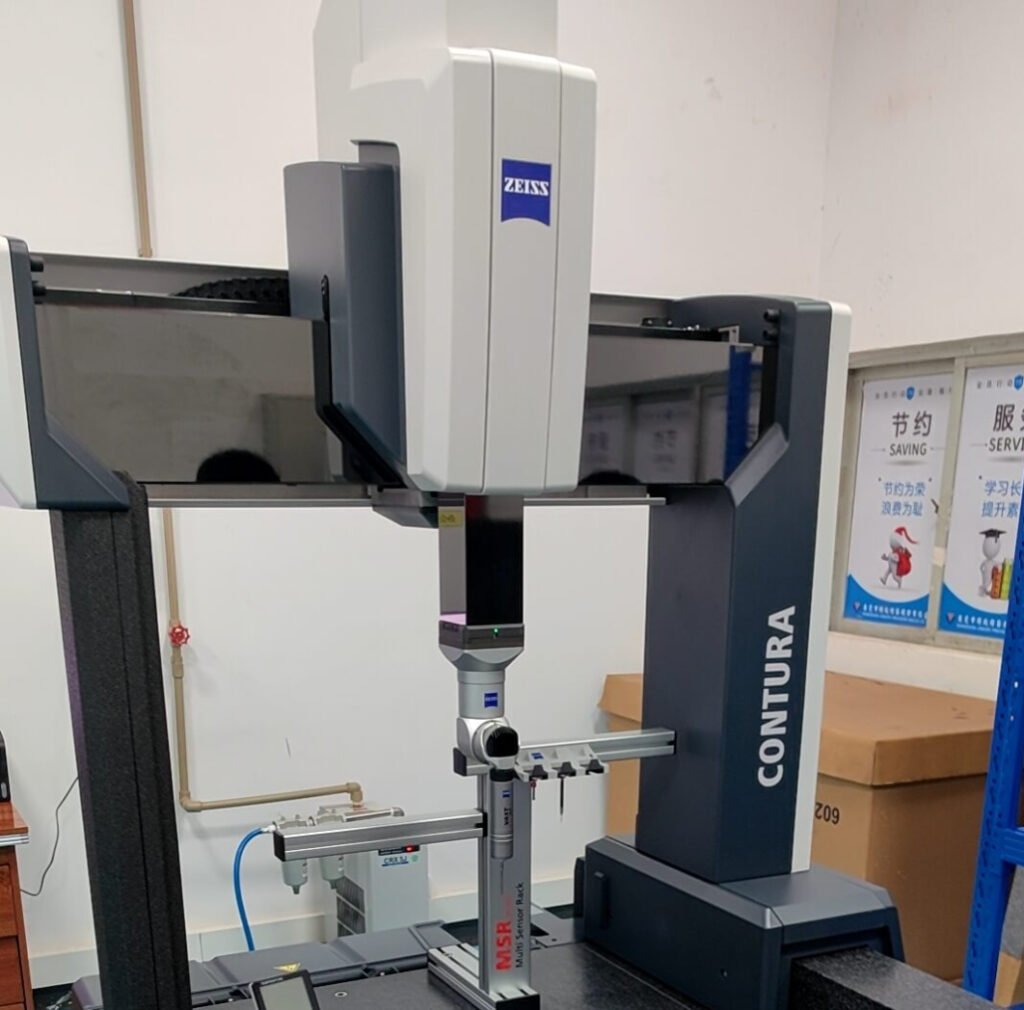
Ensuring Your Compliance with Environmental and Industry Standards
At Modo Rapid, we prioritize your need for environmentally responsible and industry-compliant manufacturing processes.
Meeting Your Environmental and Industry Standards: Our operations are designed to align with stringent environmental and industry regulations, ensuring that your projects not only meet but exceed these standards.
Certifications That Matter to You:
- ISO 9001: Guaranteeing consistent quality and continuous improvement in every product you receive.
- ISO 14001: Demonstrating our commitment to environmental management, so you can trust our sustainable practices.
- RoHS Compliance: Ensuring our materials are free from hazardous substances for your safety and peace of mind.
- REACH Compliance: Managing chemicals responsibly in our products to meet your regulatory requirements.
- IATF 16949: Meeting the rigorous quality management standards required for the automotive industry, ensuring the highest quality for your automotive projects.

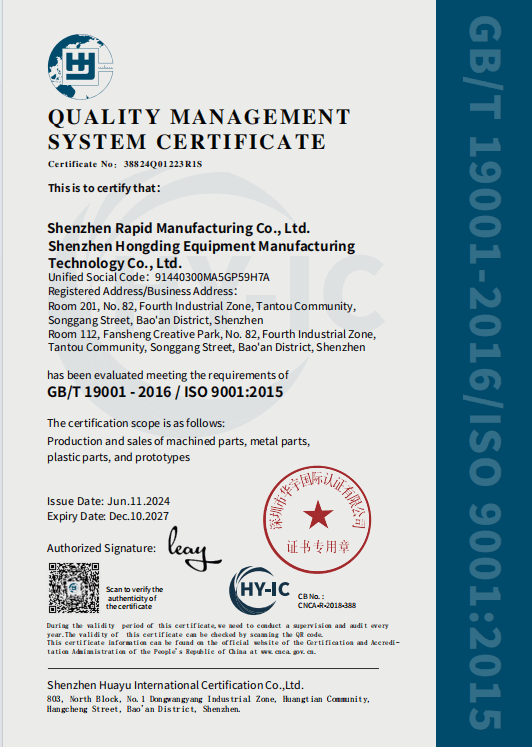
FAQ
We can achieve tight tolerances up to ±0.001mm, depending on the material and specific part requirements.
Yes, we provide rapid prototyping services to help you validate your designs before full-scale production.
Yes, our advanced 3- and 5-axis CNC machines are capable of producing highly intricate and detailed components with exceptional precision.
We accept various design file formats (such as STEP, IGES, and STL) and ensure strict confidentiality and security of your proprietary designs.
Yes, we can provide material certifications, inspection reports, and other necessary documentation upon request.
We offer global shipping and work with reliable logistics partners to ensure timely and safe delivery of your parts. Shipping options and costs will be detailed in the quotation.
Quality control is crucial, typically involving rigorous inspection processes, adherence to ISO standards, and advanced quality assurance techniques. Buyers often inquire about the supplier’s quality certifications and their processes for maintaining consistent part quality
Problems such as inconsistent part dimensions or poor surface finishes can arise from equipment wear, improper tooling, or inadequate process controls. It’s essential for suppliers to have protocols in place to address and prevent these issues
Lead times can vary based on the complexity of the parts, the materials used, and the supplier’s current workload. Procurement teams often ask about typical lead times and how suppliers manage to meet delivery deadlines
Post-sale support, including warranty services, repair options, and ongoing customer support, is an important consideration. Buyers want assurance that they can rely on the supplier for assistance even after the purchase is complete