CNC Machining Aluminum
- Exceptional Corrosion and Fatigue Resistance: Ideal for aerospace and medical industries.
- Precision:0.001mm
- Fast Turnaround Times: Receive your parts in just 1-7 days
- Certified Quality: ISO9001:2015 and IATF16949 certified processes for top-quality results.

Ensuring 0.001mm Precision in CNC Aluminum Machining
At Modo Rapid, we provide high precision in our machining processes, with tolerances up to ±0.001 mm.
Our commitment to tight tolerances ensures that your components meet the highest standards, crucial for your critical applications.
Aluminum Material Selection
Which aluminum alloy is best for my application and what is the difference between 6061 and 7075?
Choosing the right aluminum alloy is essential for optimal performance and durability. The primary difference between 6061 and 7075 aluminum lies in their composition and mechanical properties. 6061 aluminum is known for its excellent machinability, corrosion resistance, and weldability, making it ideal for structural components, automotive parts, and consumer goods.
7075 aluminum, on the other hand, is a high-strength alloy with superior toughness and fatigue resistance, widely used in aerospace and military applications where strength is critical.
What aluminum alloys can I choose?
- 6061: Offers excellent mechanical properties and corrosion resistance, perfect for structural applications, automotive parts, and consumer goods.
- 7075: Known for high strength and toughness, suitable for aerospace and high-performance engineering.
- 2024: Provides high strength and fatigue resistance, commonly used in aerospace and military applications.
- 5052: Highly corrosion-resistant, ideal for marine and chemical environments.
- 6063: Excellent extrudability and surface finish, commonly used in architectural applications.
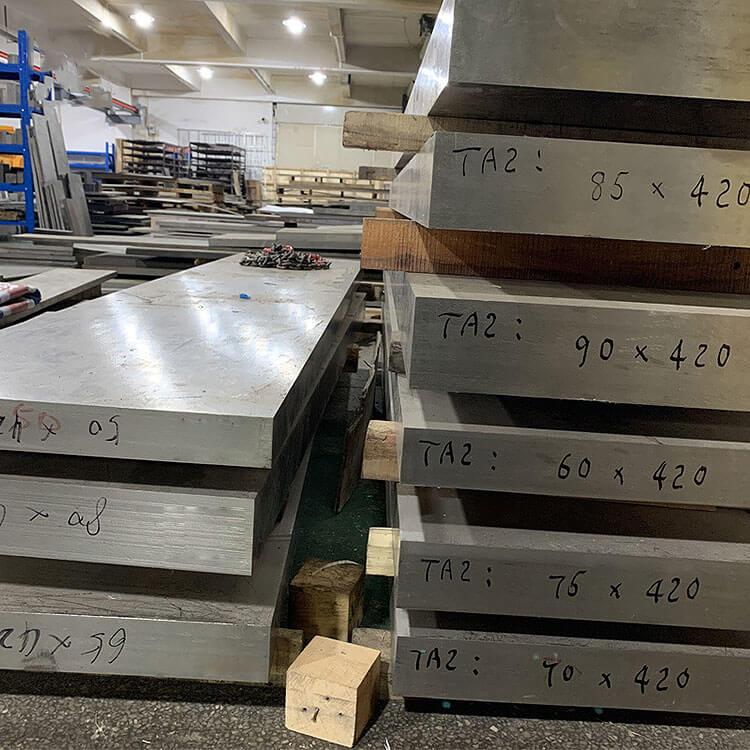
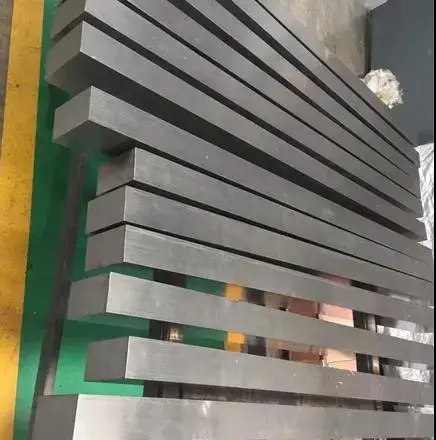
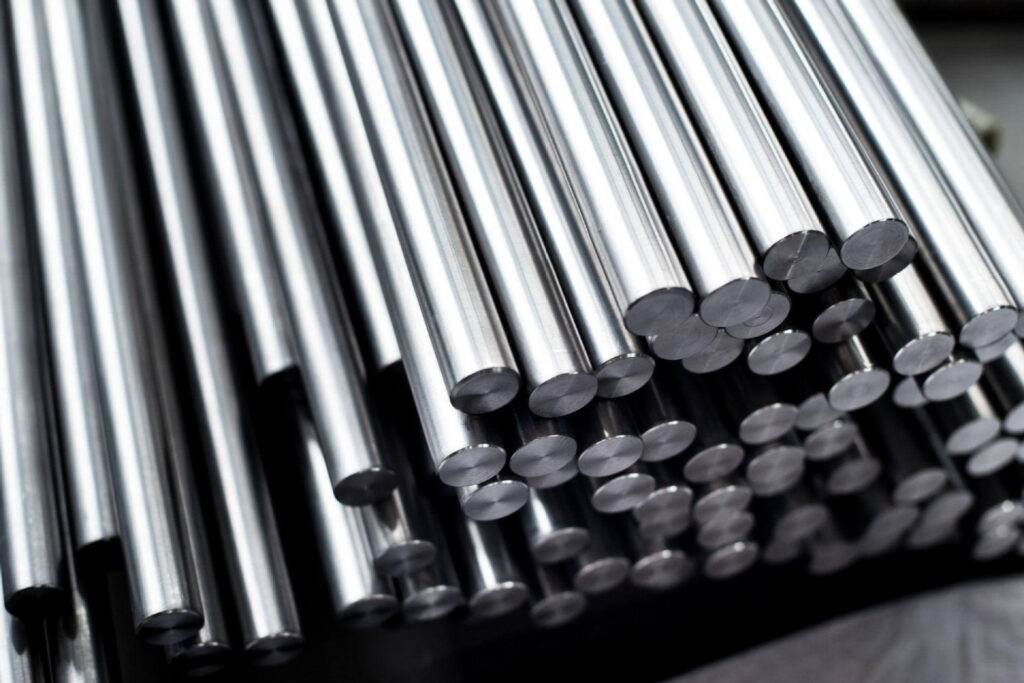
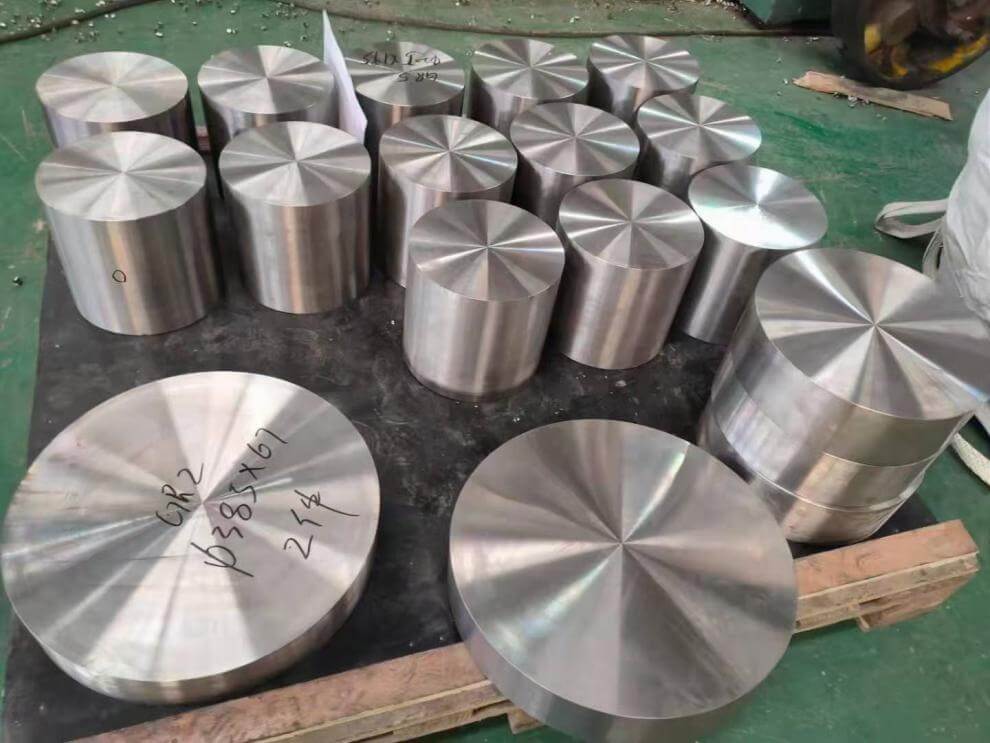
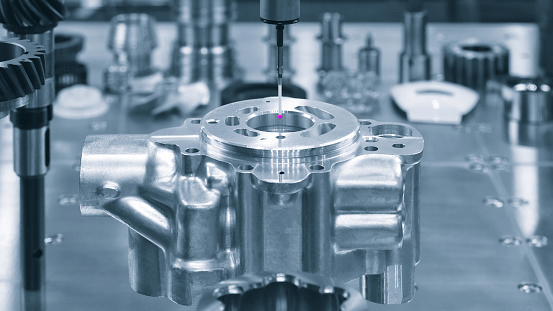
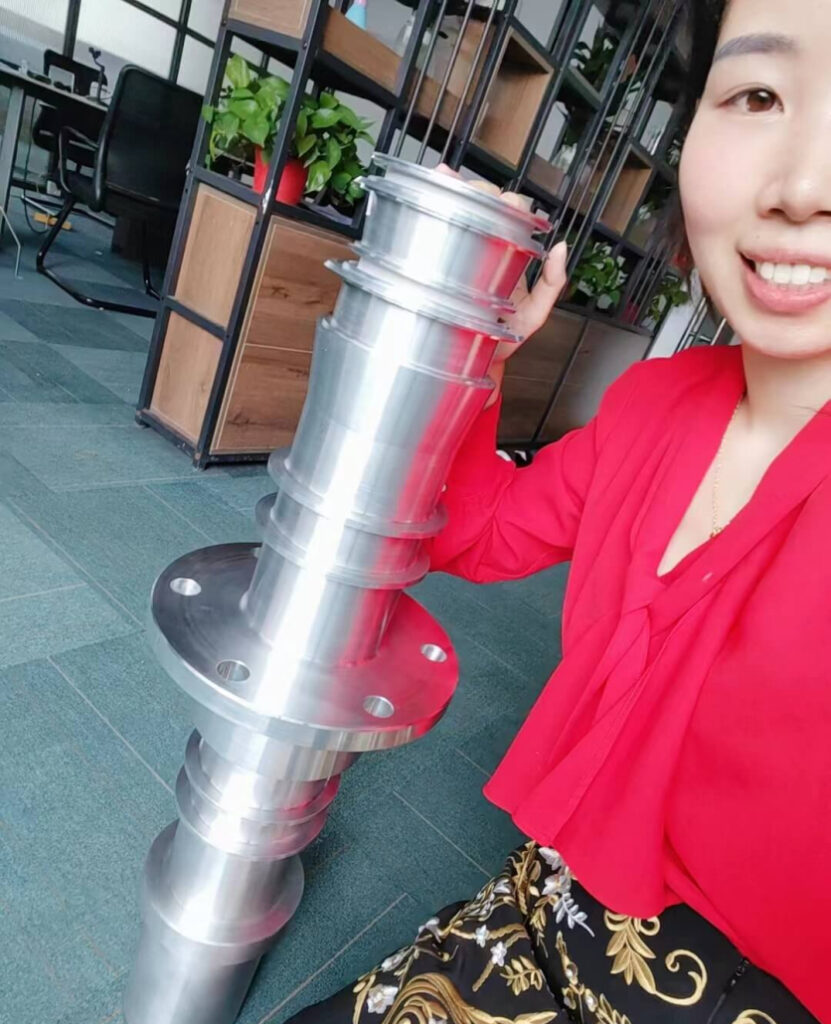
How Modo Rapid Ensures Your Aluminum Parts Remain Deformation-Free
Aluminum is a versatile material, but machining it requires expertise. At Modo Rapid, we prioritize your needs and ensure your aluminum parts maintain their integrity throughout the CNC machining process.
Heat Management
Aluminum alloys can generate significant heat during machining. We use high-speed machining techniques and efficient cooling systems to manage heat buildup, ensuring high-quality aluminum parts for you.
Burr Formation
Aluminum can form burrs during machining. We use specialized tooling and techniques to minimize burr formation and ensure smooth, precise edges on your parts.
Workholding
Aluminum’s lower rigidity requires a firm grip during CNC machining. We maintain a tight hold and ensure constant tool motion without interruptions. This prevents deformation and guarantees that your parts are machined to perfection.
At Modo Rapid, we understand the challenges of machining aluminum and employ expert techniques to ensure your parts remain flawless and deformation-free.
What are the maximum part sizes and complex geometries you can handle?
Part Sizes: We can machine parts with maximum dimensions of 1500mm x 800mm x 600mm, meeting the needs of most industrial applications.
Complex Geometries: Our 5-axis and 4-axis CNC machining centers can precisely machine complex geometries, including internal channels, intricate surfaces, and high-precision apertures. Our equipment can manage fine features and tight tolerances, ensuring your design intentions are perfectly realized.
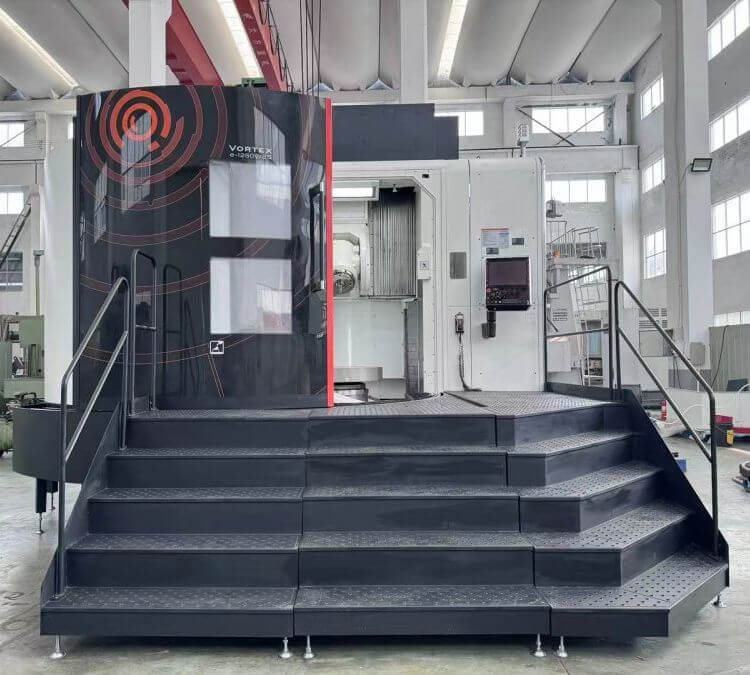
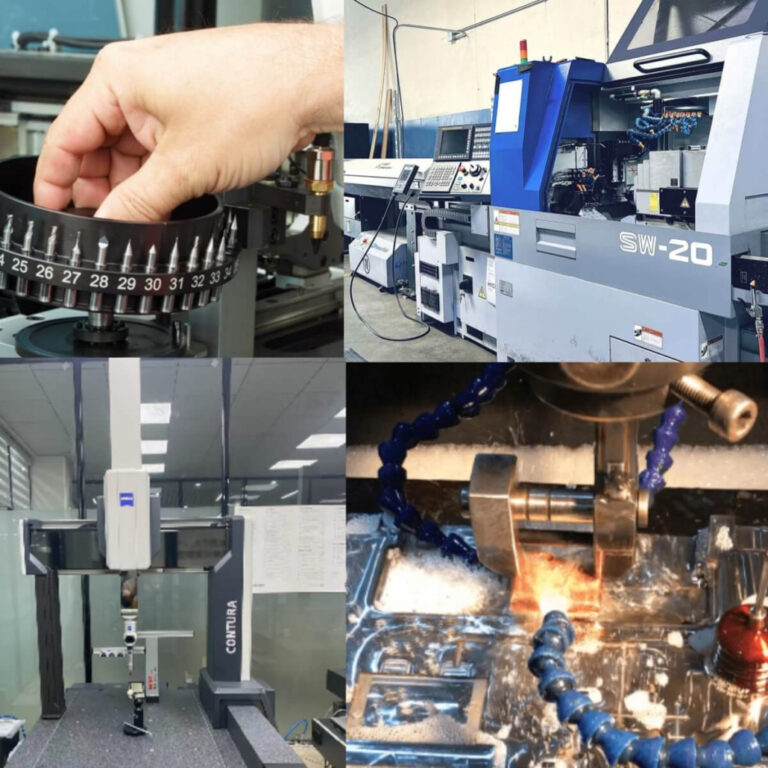
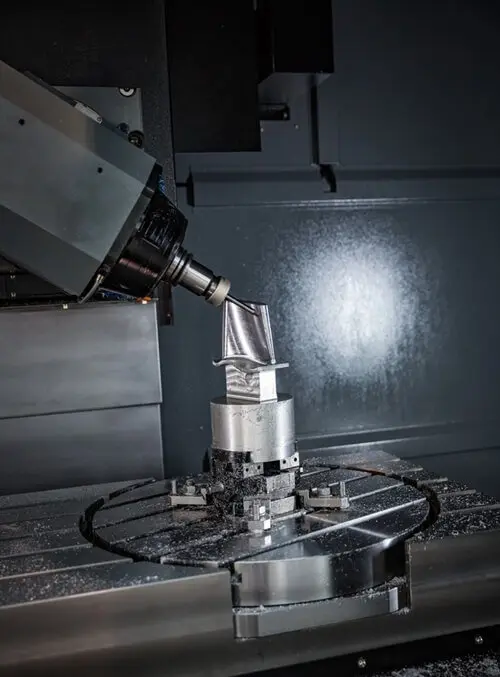
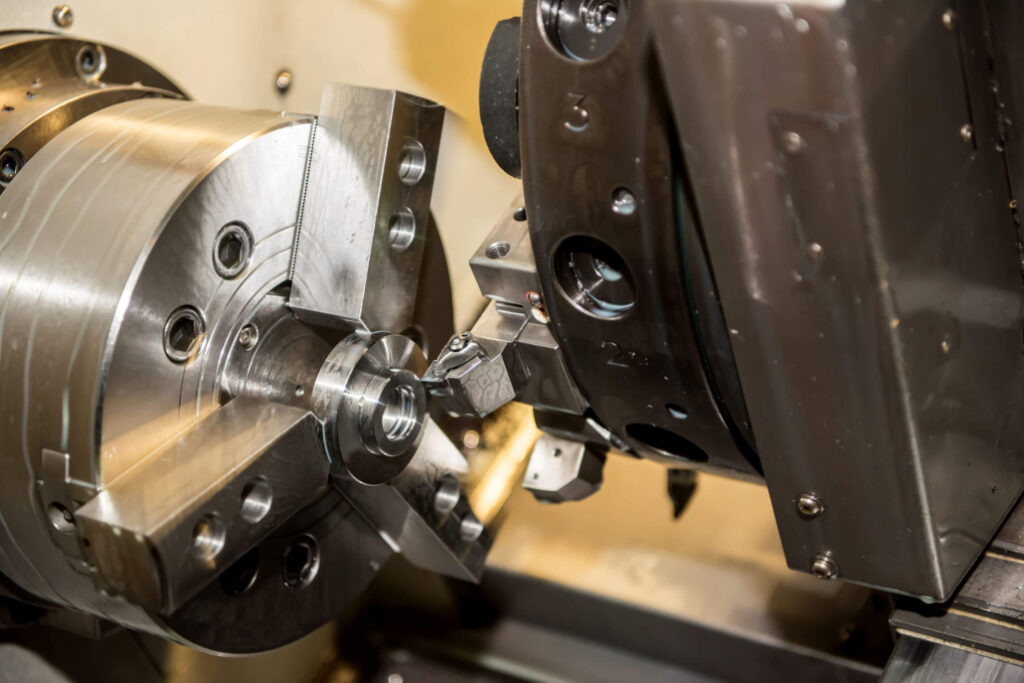
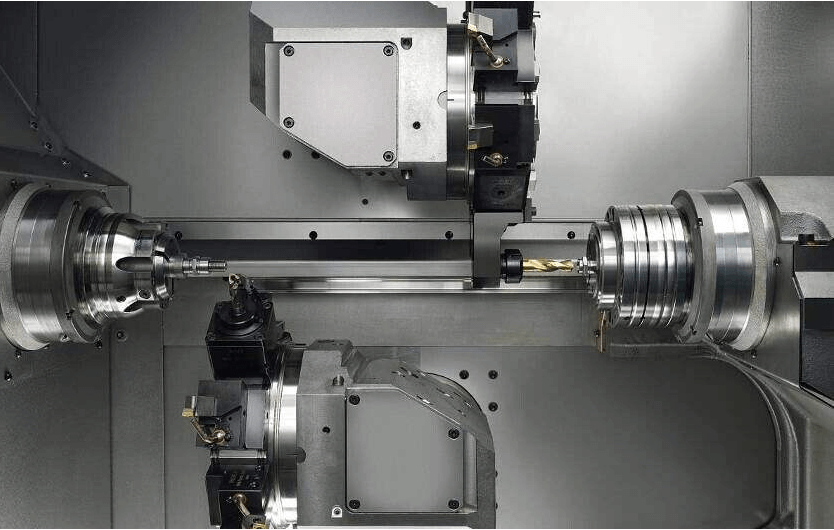

What advanced CNC equipment do you have for machining aluminum alloys?
- 5-Axis CNC Machining Centers: Capable of producing complex geometries and intricate designs, ensuring high accuracy and smooth finishes on aluminum components.
- High-Speed CNC Mills: Equipped with robust spindles and high feed rates, ideal for efficiently machining aluminum while maintaining tight tolerances.
- Multi-Tasking CNC Lathes: These machines combine milling and turning capabilities, allowing for versatile and efficient production of aluminum parts in a single setup.
- Precision CNC Grinders: Essential for achieving the fine surface finishes and exact dimensions required for high-performance aluminum components.
- EDM (Electrical Discharge Machining): Utilized for cutting intricate shapes and hard-to-machine areas, providing high precision without inducing stress in the aluminum material.
- Mill-turn machine: Combines turning and milling functions in one, completing complex multi-axis machining on a single setup. It improves accuracy and efficiency, ideal for high-precision parts. For aluminum alloy parts, its high rigidity and multi-axis capabilities reduce machining time and ensure quality. Using efficient tools and optimized parameters further enhances production speed and reliability.
Aluminum Parts Finishes
Surface Finish Options
- Smoothing
- Polishing
- Bead blasting
- Brushing
- Painting
- Chroming
- Anodizing
- Powder coating
- Electrophoresis
Impact of Surface Preparation on Aluminum Parts
Surface preparation significantly influences both the performance and appearance of aluminum parts:
- Enhanced Durability: Proper surface preparation can increase the lifespan of aluminum parts by improving resistance to corrosion and wear.
- Improved Functionality: A well-prepared surface can reduce friction and improve the efficiency of mechanical components.
- Aesthetic Appeal: High-quality finishes enhance the visual appeal of aluminum parts, making them suitable for both functional and decorative applications.
- Adhesion of Coatings: Proper preparation ensures better adhesion of subsequent coatings or treatments, ensuring consistent and long-lasting finishes.
Aluminum Anodizing
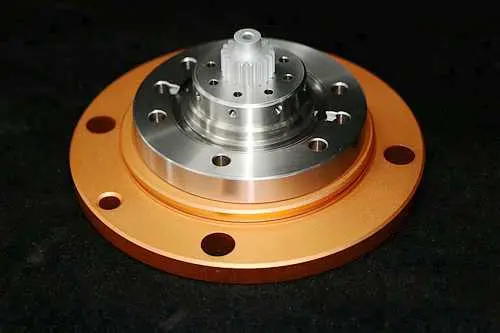
Aluminum Part Surface Finish
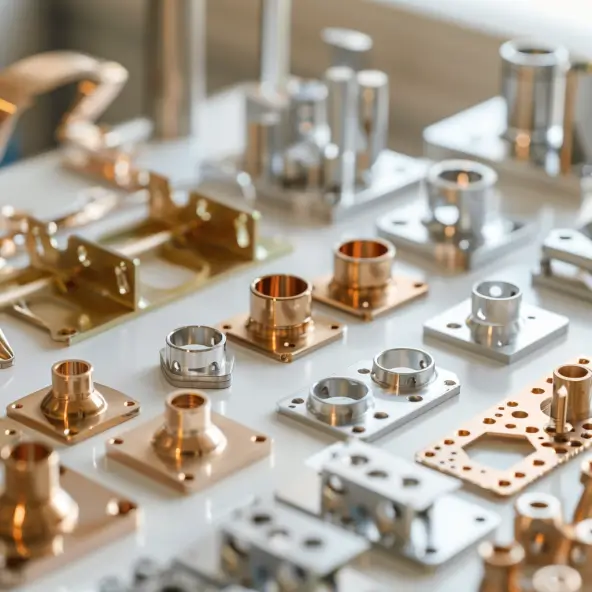
Cost Calculation for Custom Aluminum Alloy Parts
The cost of machining aluminum parts at Modo Rapid is determined by several key factors:
- Material Costs: The price of aluminum, though lower compared to other metals, varies based on alloy and market conditions.
- Complexity of Design: Parts with intricate designs and tight tolerances require more time and specialized tools, increasing costs.
- Machining Time: Longer machining times due to specific requirements for precision operations.
- Surface Finishes: Additional processes such as anodizing, polishing, or coating add to the total cost.
- Tool Wear: Aluminum’s properties require careful tool management, impacting tool replacement costs.
Volume Discounts and Minimum Order Quantity
At Modo Rapid, we offer volume discounts to accommodate larger production runs. The discounts increase with the order size, making it more cost-effective for bulk purchases. We understand the diverse needs of our clients, so we have set a flexible minimum order quantity to cater to both small and large projects.

Example: Cost Calculation
Let’s assume we have an aluminum alloy part with the following specifications:
- Dimensions: 100mm x 50mm x 10mm
- Complexity: Medium complexity geometry
- Surface Finish: Anodized
- Quantity: 50 pieces
Material Cost
- Price of aluminum alloy: $10/kg
- Weight per part: 0.4 kg
- Total material cost: 50 pieces x 0.4 kg x $10/kg = $200
Machining Cost
- Machining time for medium complexity parts: 1 hour/part
- Machining rate: $60/hour
- Total machining cost: 50 pieces x 1 hour/piece x $60/hour = $3,000
Surface Finish Cost
- Anodizing cost: $10/piece
- Total surface finish cost: 50 pieces x $10/piece = $500
Tool and Equipment Wear
- Estimated tool and equipment wear cost: $300
Other Costs
- Quality control and inspection fees: $200
- Packaging and shipping fees: $100
Total cost = Material cost + Machining cost + Surface finish cost + Tool and equipment wear + Other costs
Total cost = $200 + $3,000 + $500 + $300 + $300 = $4,300
Cost per part = Total cost / Quantity
Cost per part = $4,300 / 50 pieces = $86/piece
This example provides a rough estimate of the cost. Actual costs will vary based on specific designs, process requirements, and quantities. To receive an accurate quote, please provide detailed mechanical drawings and technical specifications. We will then provide a customized quote based on your needs.
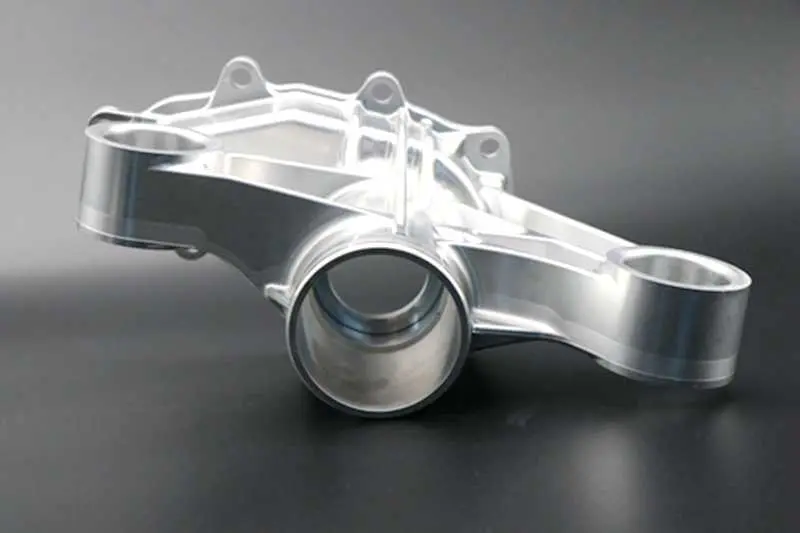
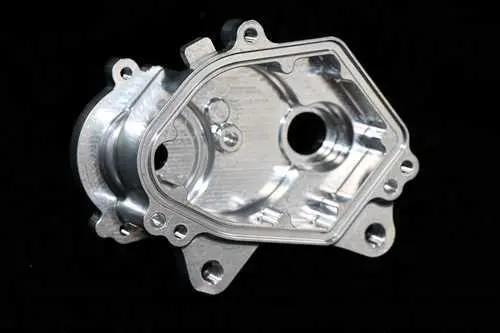
Production Lead Time and Delivery Time
Typical Lead Time from Order Placement to Delivery
At Modo Rapid, our standard lead time from order placement to delivery typically ranges from 1 to 2 weeks. This timeline includes:
- Order Confirmation and Planning: 1-2 days
- Procurement of Materials: 2-3 days
- Machining and Production: 5-7 days
- Quality Control and Inspection: 1-2 days
- Packaging and Shipping: 1-2 days
How Do We Deal With Your Expedited Orders?
Yes, we can shorten the production time for expedited orders. If you require faster delivery, please inform us at the time of order placement. Expedited orders are subject to an additional fee and depend on the current production schedule and the complexity of the parts. By prioritizing your order, we can often reduce the lead time to 1-7 days.
Our team is committed to meeting your deadlines and ensuring that you receive your parts on time, even for urgent projects. Please contact us directly to discuss your specific requirements and expedited options.
How Do We Ensure Consistency and Quality for Each Batch of Parts?
Quality Control Measures:
Advanced Inspection Tools: Utilization of CMMs (Coordinate Measuring Machines), laser scanners, and precision gauges to measure critical dimensions and geometries.
In-Process Monitoring: Continuous monitoring during machining processes to detect and correct deviations in real-time.
Material Verification: Comprehensive material testing, including chemical composition and mechanical property analysis, to ensure conformity with specifications.
Surface Finish Analysis: Employing profilometers and other surface finish measurement tools to guarantee that all parts meet required surface quality standards.
Environmental Controls: Maintaining a controlled environment in production areas to minimize the impact of temperature and humidity variations on machining accuracy.
Ensuring Consistency and Quality for Each Batch:
Standard Operating Procedures (SOPs): Strict adherence to standardized processes for each operation to ensure uniformity across all production stages.
First Article Inspection (FAI): Conducting thorough inspections on the first piece of each batch to verify that it meets all specified requirements before proceeding with full-scale production.
Statistical Process Control (SPC): Applying SPC techniques to monitor and control the manufacturing process, ensuring that variations are kept within acceptable limits.
Lot Traceability: Implementing comprehensive traceability systems to track materials and processes for each batch, allowing for easy identification and resolution of any quality issues.
Final Inspection and Testing: Performing rigorous final inspections and functional tests on all parts before shipment to confirm that they meet client specifications and quality standards.
Our commitment to stringent quality control measures ensures that you receive consistent, high-quality parts in every batch, supporting your projects’ success and reliability.
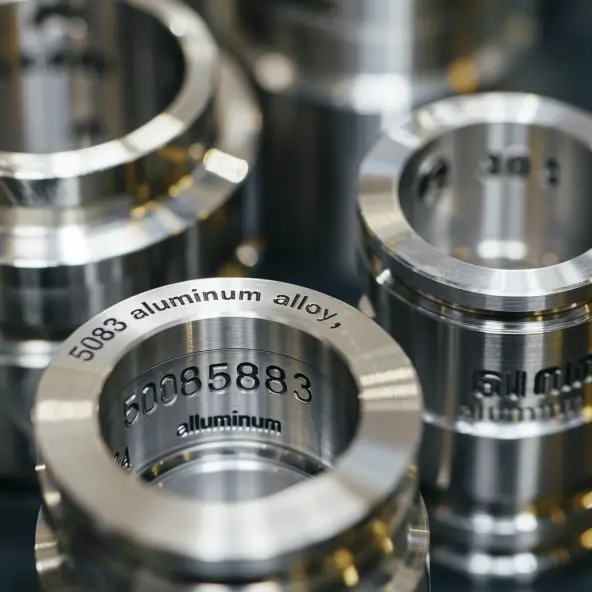
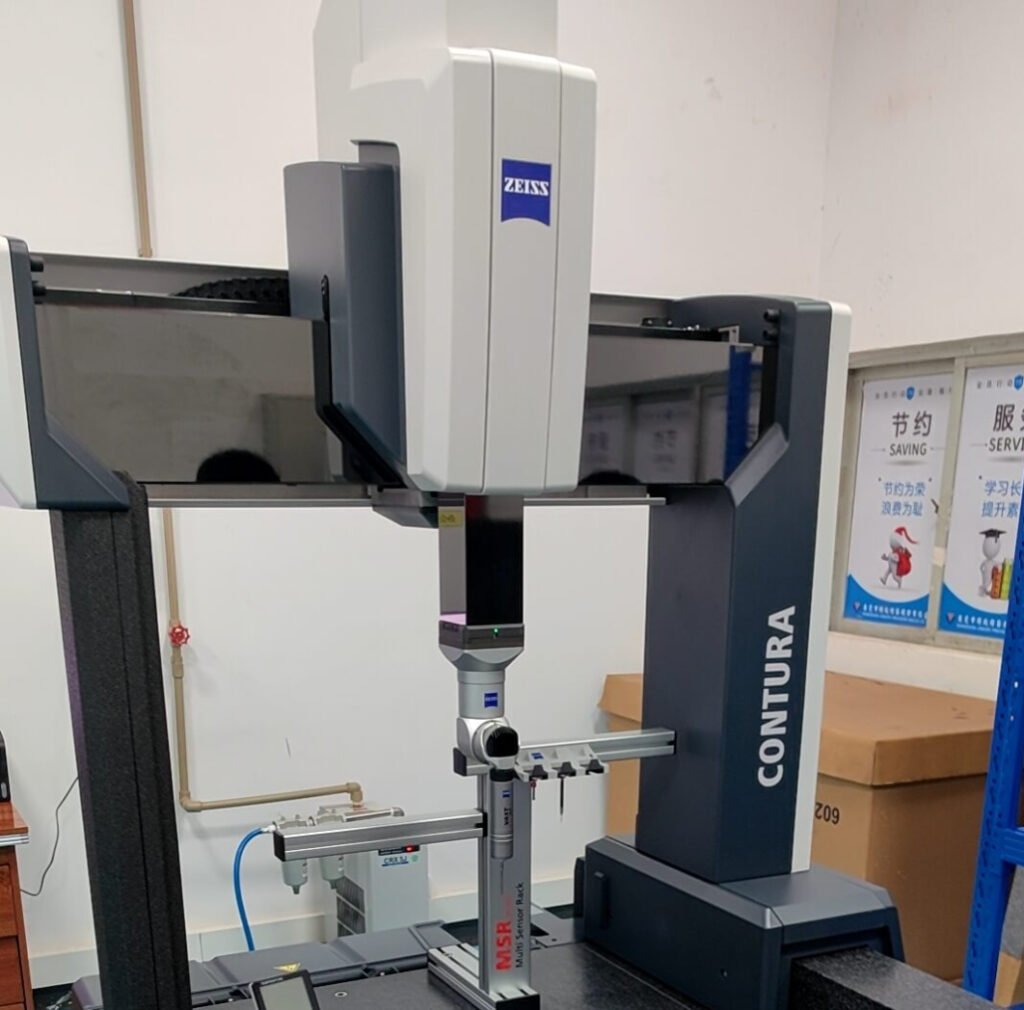
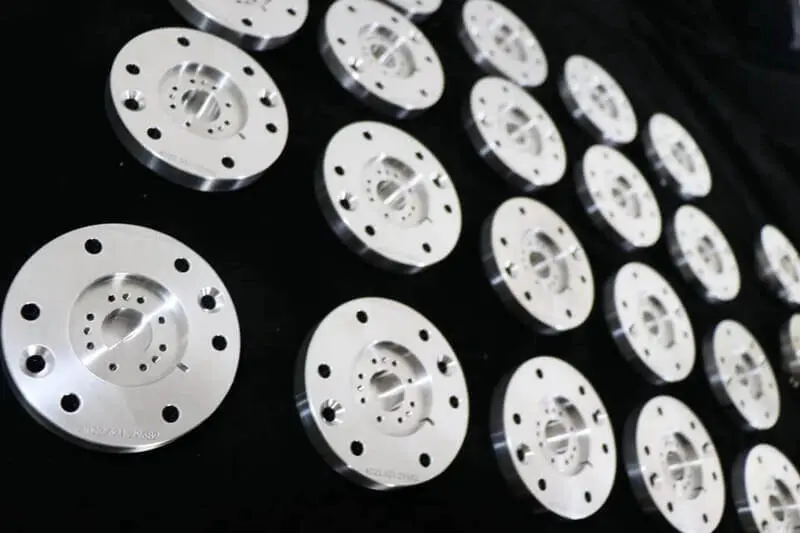
Why Modo Rapid is Your Trusted Partner for Aluminum Projects
At Modo Rapid, we combine extensive experience, advanced technology, and a skilled team to deliver high-quality aluminum parts.
Rich Experience: Over a decade in aluminum machining across aerospace, medical, and automotive industries.
Advanced CNC Technology: Cutting-edge equipment for precision and efficiency in complex geometries.
Skilled Team: Expert engineers and technicians dedicated to quality and overcoming aluminum’s unique challenges.
Stringent Quality Control: Rigorous measures at every stage ensure consistent, reliable parts.
Customer-Centric Approach: Tailored solutions with open communication and collaboration.
Innovative Solutions: Continuous investment in R&D for advanced, competitive solutions.
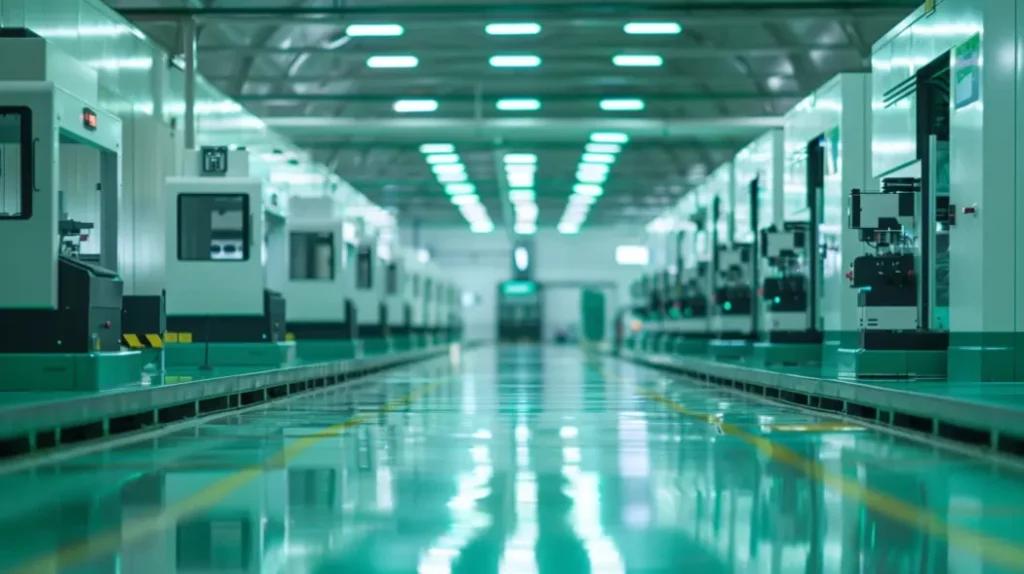
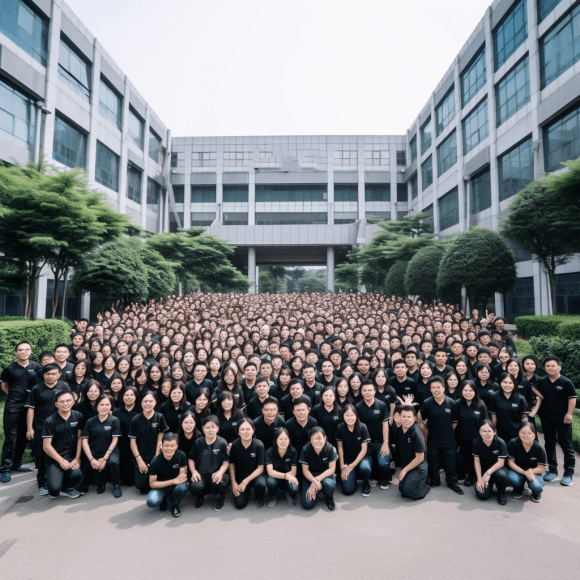
Client Feedback & Reviews
Ensuring Your Compliance with Environmental and Industry Standards
At Modo Rapid, we prioritize your need for environmentally responsible and industry-compliant manufacturing processes.
Meeting Your Environmental and Industry Standards: Our operations are designed to align with stringent environmental and industry regulations, ensuring that your projects not only meet but exceed these standards.
Certifications That Matter to You:
- ISO 9001: Guaranteeing consistent quality and continuous improvement in every product you receive.
- ISO 14001: Demonstrating our commitment to environmental management, so you can trust our sustainable practices.
- RoHS Compliance: Ensuring our materials are free from hazardous substances for your safety and peace of mind.
- REACH Compliance: Managing chemicals responsibly in our products to meet your regulatory requirements.
- IATF 16949: Meeting the rigorous quality management standards required for the automotive industry, ensuring the highest quality for your automotive projects.

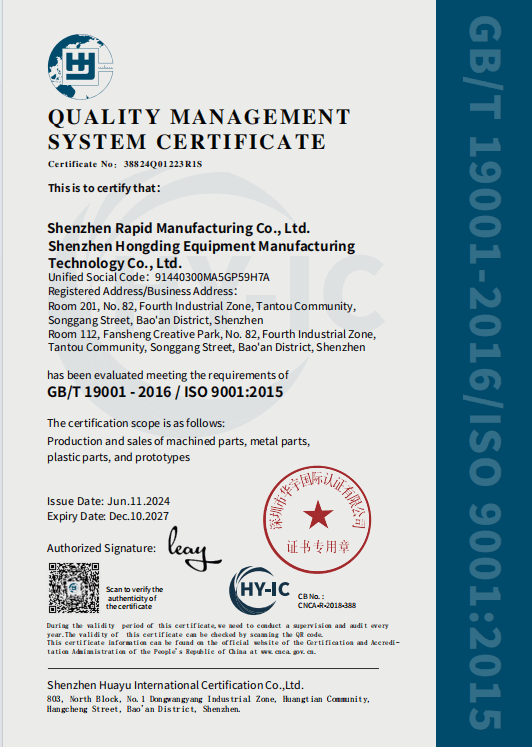
FAQ
6061 aluminum is one of the best options for CNC machining due to its excellent mechanical properties, good corrosion resistance, and ease of machining. It’s versatile and widely used across various industries.
Yes, 6061 aluminum machines very well. It has good machinability and responds well to both high-speed and low-speed machining processes, making it ideal for CNC operations.
6061 aluminum is considered one of the easiest machinable aluminum alloys. Its balanced properties make it suitable for a wide range of applications and straightforward to machine.
Inconel, a nickel-chromium-based superalloy, is often considered the hardest material to CNC machine due to its toughness, heat resistance, and tendency to work-harden.
A spindle with a power rating between 3 to 10 kW is typically suitable for CNC machining aluminum. The exact power required depends on the complexity and size of the parts being machined.
Aluminum is generally not hard to machine; however, it can present challenges like galling and tool wear if not machined with the right techniques and tools. Its softness can cause material to stick to the cutting tool if improper feeds and speeds are used.
6061 aluminum is generally more expensive than 5052 aluminum due to its superior mechanical properties and broader application range.
For CNC machining aluminum, cutting speeds typically range from 1500 to 3000 surface feet per minute (SFM). Exact speeds depend on the specific alloy and machining operation.
6061 aluminum is popular due to its excellent balance of strength, corrosion resistance, machinability, and cost. It is versatile and suitable for a wide range of applications from aerospace to consumer products.
You can differentiate 5052 and 6061 aluminum by their mechanical properties and chemical composition. 5052 has higher corrosion resistance and is more malleable, while 6061 is stronger and more suitable for structural applications. Material certificates and testing can also identify the alloy.
Common grades of aluminum used for CNC machining include 6061, 7075, 2024, and 5052, with 6061 being the most widely used due to its balanced properties.
6061 and 7075 are among the best aluminum alloys for CNC machining. 6061 is favored for its versatility, while 7075 is chosen for applications requiring higher strength.
The minimum thickness for machining aluminum largely depends on the part design and application, but generally, aluminum can be machined to thicknesses as thin as 0.5 mm with proper support and tooling.
A 2-flute end mill is generally better for aluminum as it provides larger chip clearance, reducing the risk of chip packing and improving surface finish.
A helix angle of 35° to 45° is considered ideal for machining aluminum. This range provides a good balance between cutting efficiency and chip evacuation.
By addressing these FAQs comprehensively and professionally, we demonstrate our expertise in CNC machining and our commitment to delivering high-quality aluminum parts tailored to your needs.
Custom Aluminum Parts for Your Project!
Experience tailored excellence with our high-precision aluminum parts. We manufacture to your exact specifications, ensuring top-quality results and cost efficiency.
At Modo Rapid, we prioritize your project’s success, offering unmatched precision and competitive prices. Choose us for seamless, customized aluminum part solutions. Send us your specifications and let us help you achieve your goals.
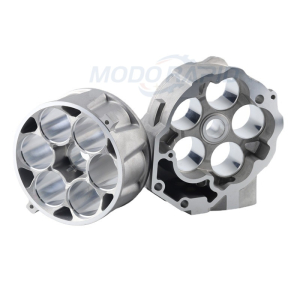
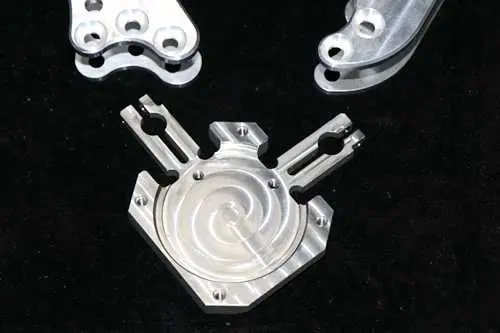
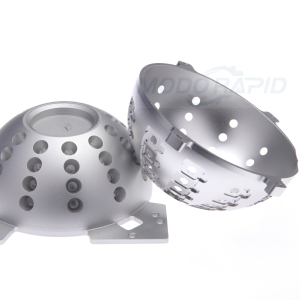
Get a quote for custom aluminum parts
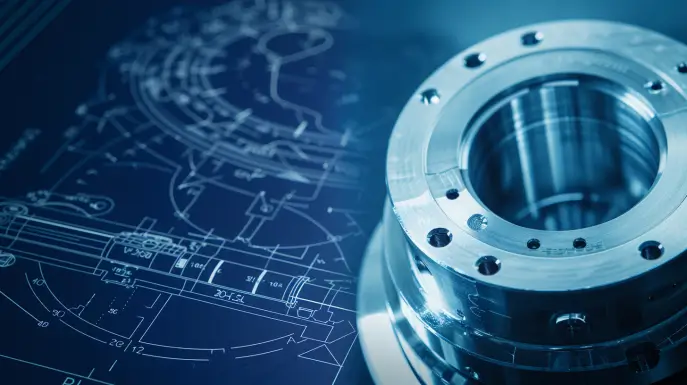