CNC Machining Nylon
- Superior Impact Resistance: Ideal for automotive and consumer electronics applications.
- Precision:0.001mm
- Fast Turnaround Times: Receive your parts in just 1-7 days
- Certified Quality: ISO9001:2015 and IATF16949 certified processes for top-quality results.

Achieving 0.01mm Precision in CNC Nylon Machining
At Modo Rapid, our CNC machining processes ensure precision tolerances of up to ±0.01 mm, guaranteeing your components meet the highest standards required for critical applications.
Nylon Material Selection
Which Nylon grade is best for my application and what are the differences between standard and reinforced Nylon?
Choosing the right Nylon grade is essential for performance and durability. Standard Nylon offers excellent mechanical properties and ease of processing, ideal for general-purpose applications like gears and bearings. Reinforced Nylon, often with glass or carbon fibers, enhances strength and stiffness, making it suitable for structural components in automotive and industrial applications.
Available Nylon Grades:
- Standard Nylon: Excellent toughness and wear resistance for general use.
- Glass-Filled Nylon: Enhanced strength and rigidity for load-bearing applications.
- Carbon-Filled Nylon: Superior stiffness and thermal conductivity for high-performance parts.
- Oil-Filled Nylon: Reduced friction and improved wear resistance for sliding applications.
- Flame-Retardant Nylon: Enhanced safety for electrical and electronic components.
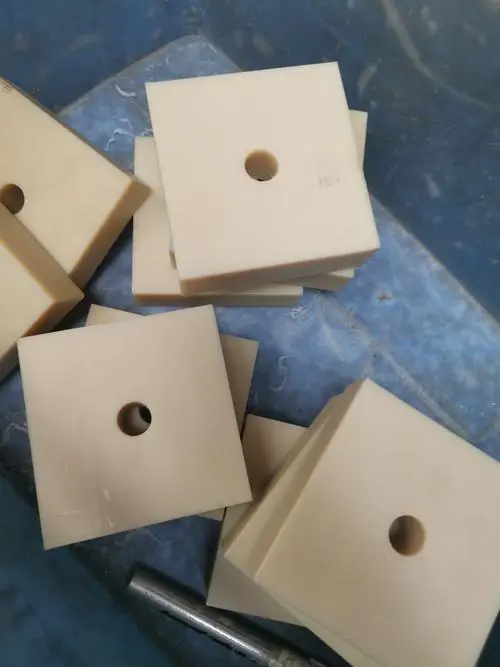
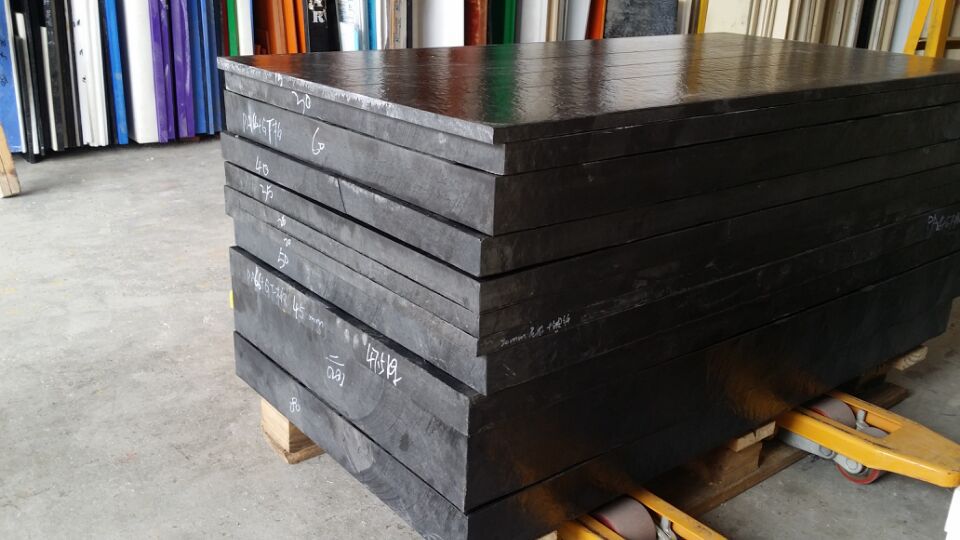
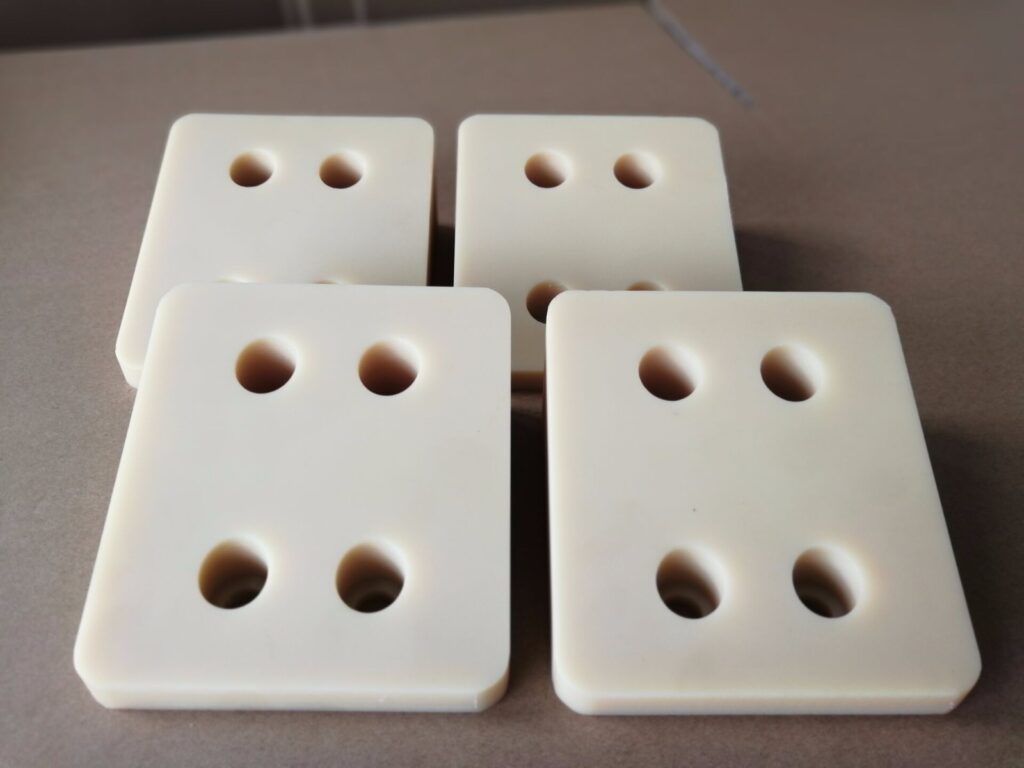
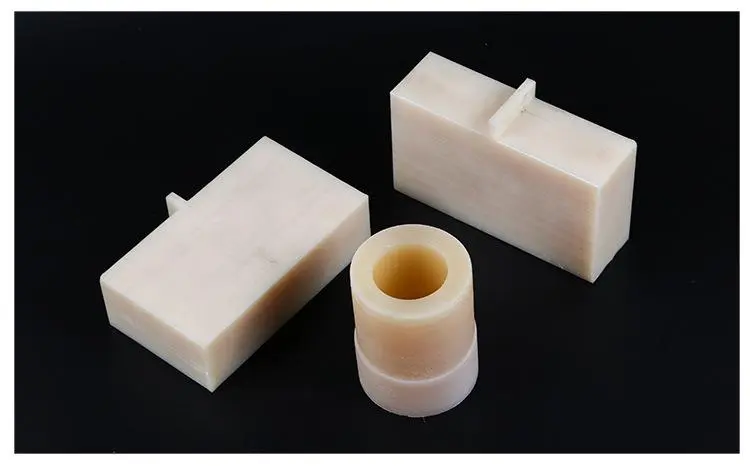
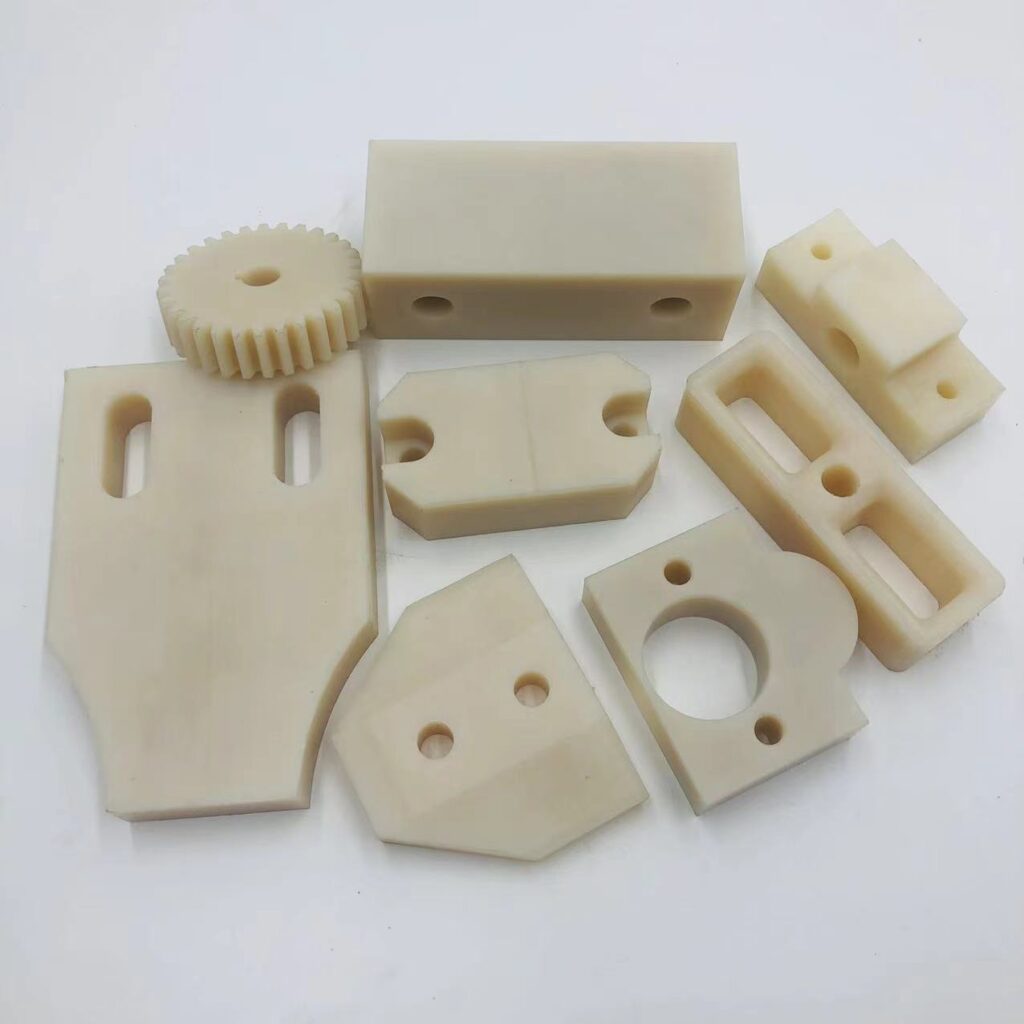
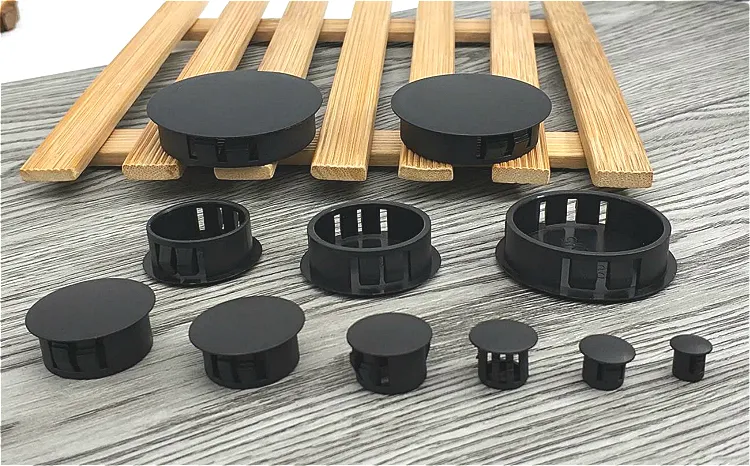
How Modo Rapid Ensures Your Nylon Parts Remain Deformation-Free
Machining Nylon requires careful management to prevent deformation. At Modo Rapid, we employ expert techniques to maintain the integrity of your parts.
Heat Buildup
Nylon can deform with excessive heat. We optimize cutting parameters and use high-pressure coolant systems to minimize heat, ensuring high-quality parts.
Tool Wear
Nylon’s abrasive nature can cause tool wear. We use sharp tools and appropriate feed rates to ensure efficient machining and precise parts.
Workholding
Secure workholding is crucial to prevent deformation. We maintain a tight grip and ensure constant tool motion, delivering flawless parts.
Maximum Part Sizes and Complex Geometries
- Part Sizes: We can machine parts up to 1500mm x 800mm x 600mm, suitable for most industrial applications.
- Complex Geometries: Our 5-axis and 4-axis CNC machines handle intricate geometries, internal channels, and high-precision apertures.
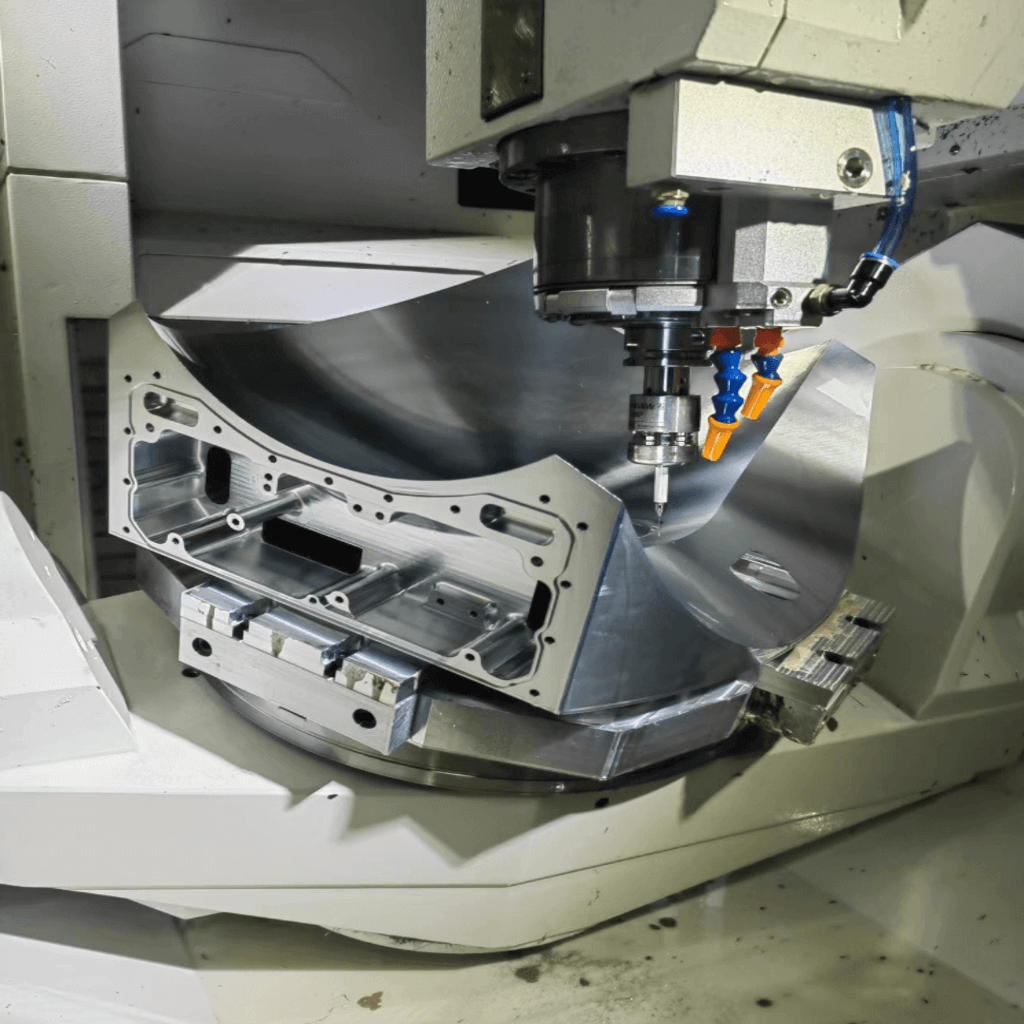
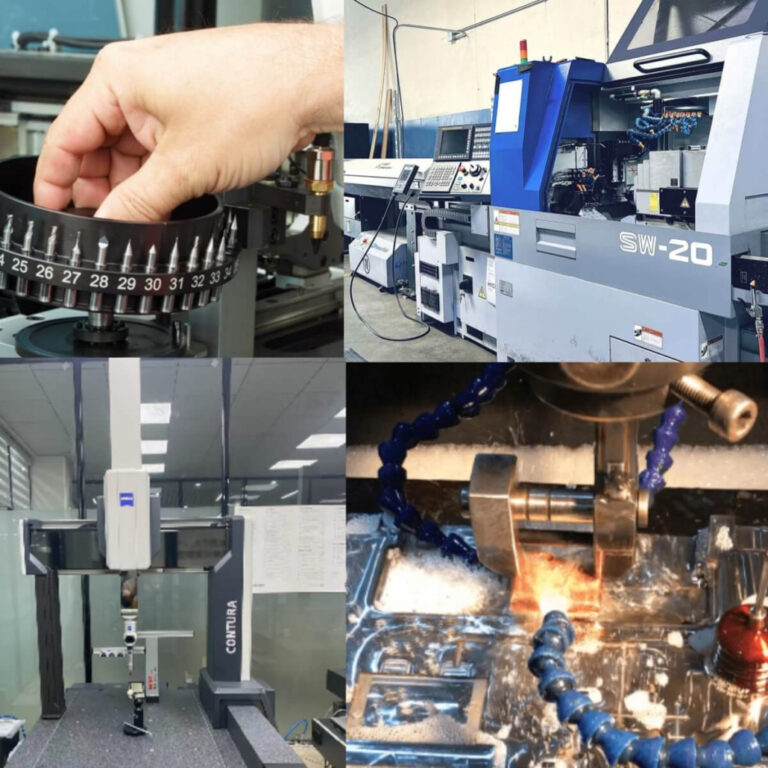
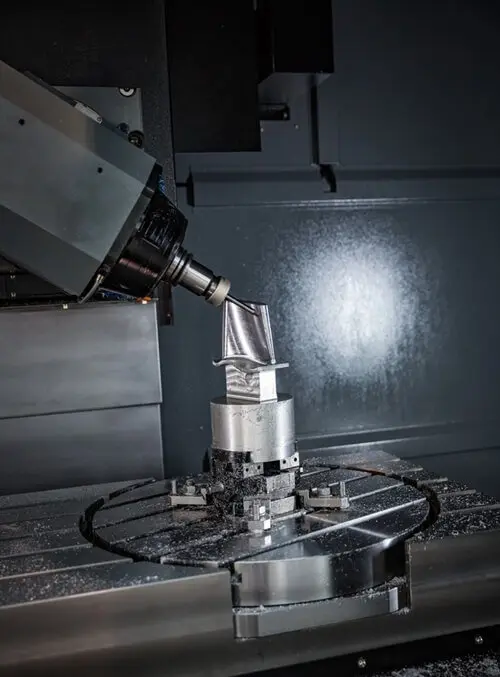
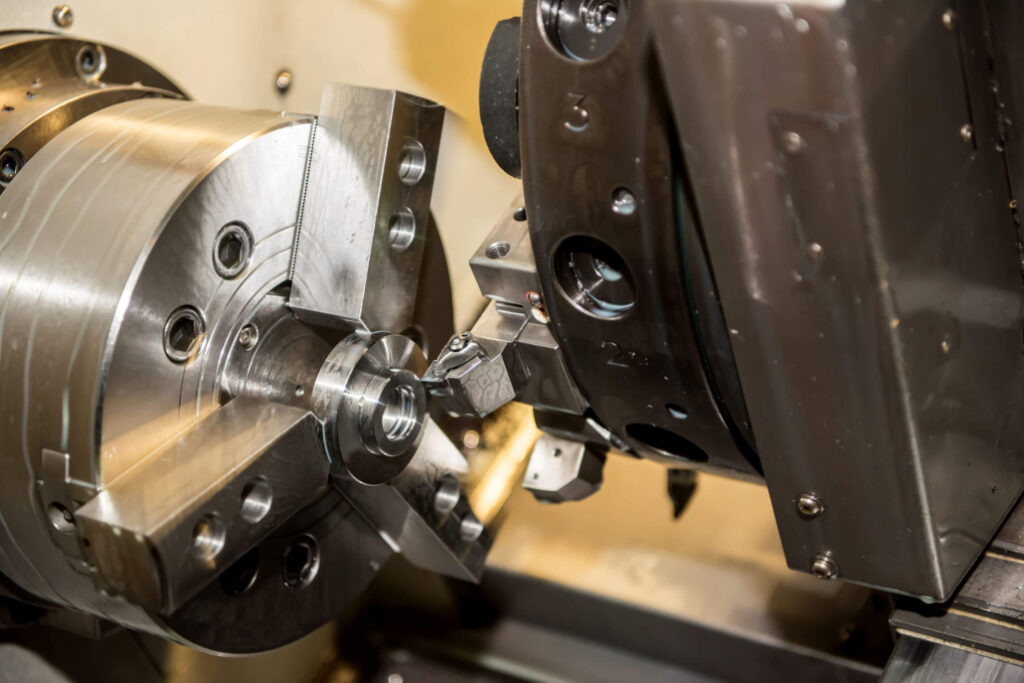
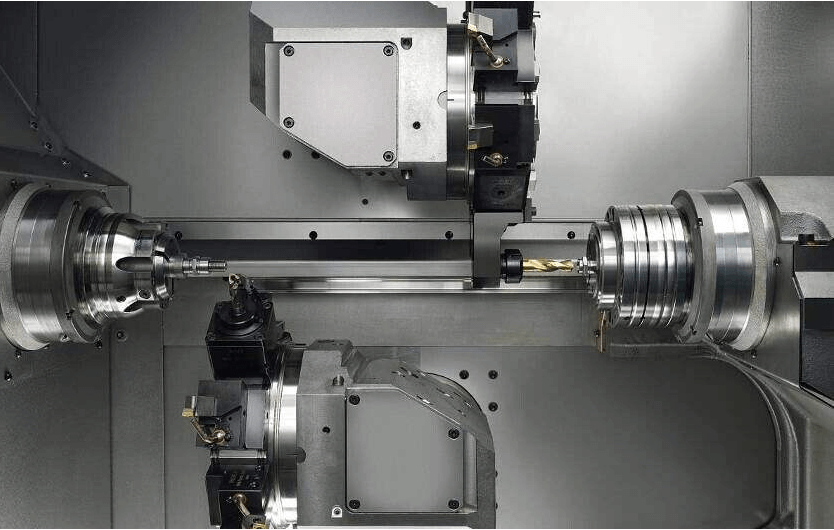

Advanced CNC Equipment for Machining Nylon
- 5-Axis CNC Machining Centers: For complex geometries and smooth finishes.
- High-Speed CNC Mills: Ideal for efficiently machining Nylon with tight tolerances.
- Multi-Tasking CNC Lathes: Versatile production in a single setup.
- Precision CNC Grinders: For fine surface finishes and exact dimensions.
- EDM (Electrical Discharge Machining): High precision without inducing stress.
- Mill-Turn Machines: For high-precision parts with reduced machining time.
Nylon Parts Finishes
Surface Finish Options
- Smoothing
- Polishing
- Bead Blasting
- Brushing
- Painting
- Plating
- Metallizing
- PVD Coating
- Powder Coating
- Electrophoresis
Impact of Surface Preparation on Nylon Parts
Proper surface preparation enhances durability, functionality, and aesthetic appeal, ensuring better adhesion of coatings and long-lasting finishes.
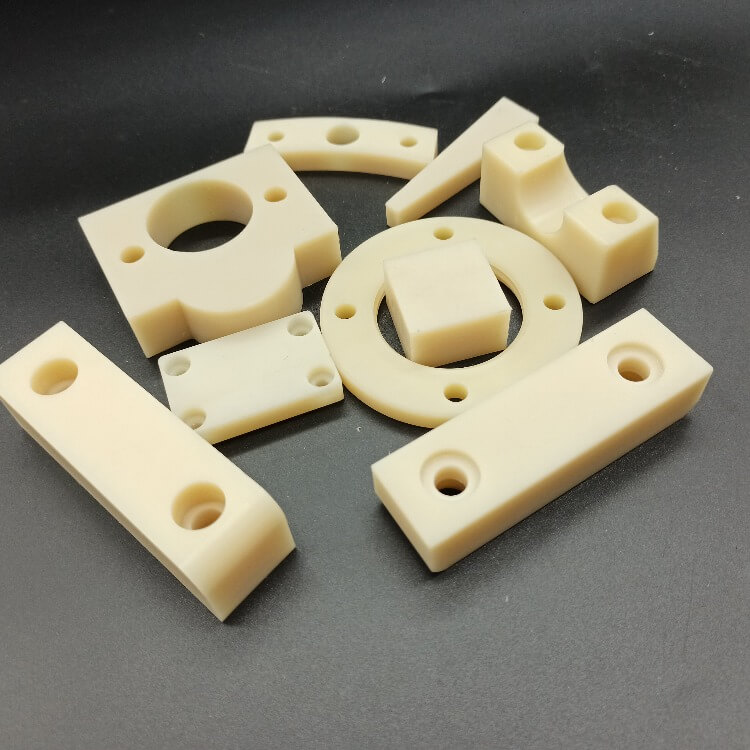
ABS Part Surface Finish
Cost Calculation for Custom Nylon Parts
Several factors determine the cost of machining Nylon parts at Modo Rapid:
- Material Costs: Nylon is relatively affordable.
- Complexity of Design: Intricate designs and tight tolerances increase costs.
- Machining Time: Longer times due to precise operations.
- Surface Finishes: Additional processes add to the total cost.
- Tool Wear: Nylon’s properties lead to moderate tool wear.
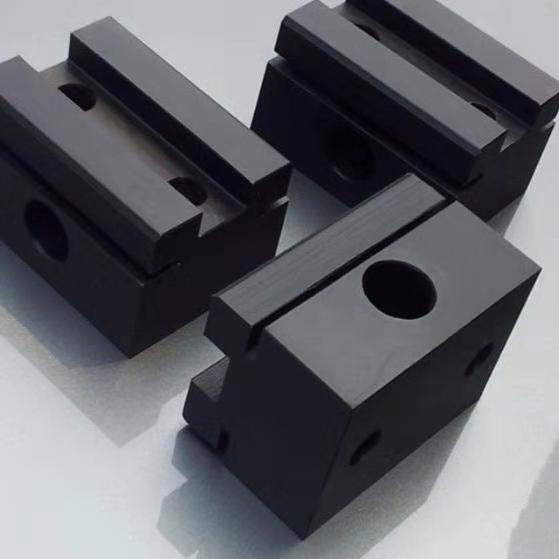
Example: Cost Calculation
Assuming a Nylon part with the following specifications:
- Dimensions: 100mm x 50mm x 10mm
- Complexity: Medium complexity geometry
- Surface Finish: Painted
- Quantity: 50 pieces
Material Cost
- Price of Nylon: $4/kg
- Weight per part: 0.2 kg
- Total material cost: 50 pieces x 0.2 kg x $4/kg = $40
Machining Cost
- Machining time for medium complexity parts: 0.5 hour/part
- Machining rate: $40/hour
- Total machining cost: 50 pieces x 0.5 hour/piece x $40/hour = $1,000
Surface Finish Cost
- Painting cost: $2/piece
- Total surface finish cost: 50 pieces x $2/piece = $100
Tool and Equipment Wear
- Estimated tool and equipment wear cost: $50
Other Costs
- Quality control and inspection fees: $100
- Packaging and shipping fees: $50
Total cost = Material cost + Machining cost + Surface finish cost + Tool and equipment wear + Other costs
Total cost = $40 + $1,000 + $100 + $50 + $150 = $1,340
Cost per part = Total cost / Quantity
Cost per part = $1,340 / 50 pieces = $26.80/piece
This example provides a rough estimate of the cost. Actual costs will vary based on specific designs, process requirements, and quantities. To receive an accurate quote, please provide detailed mechanical drawings and technical specifications.
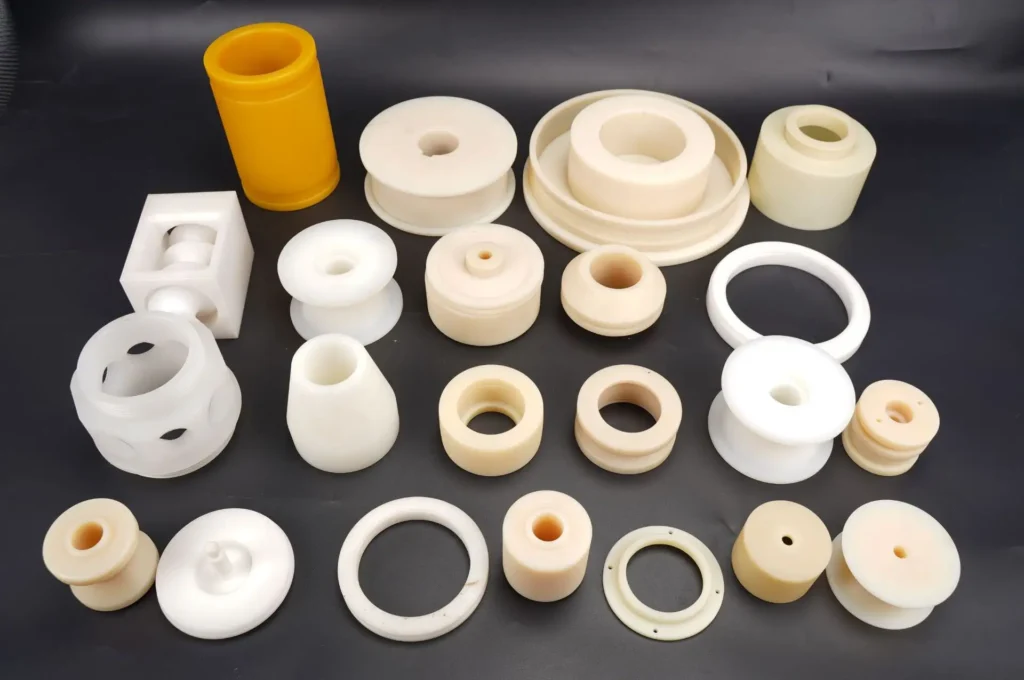
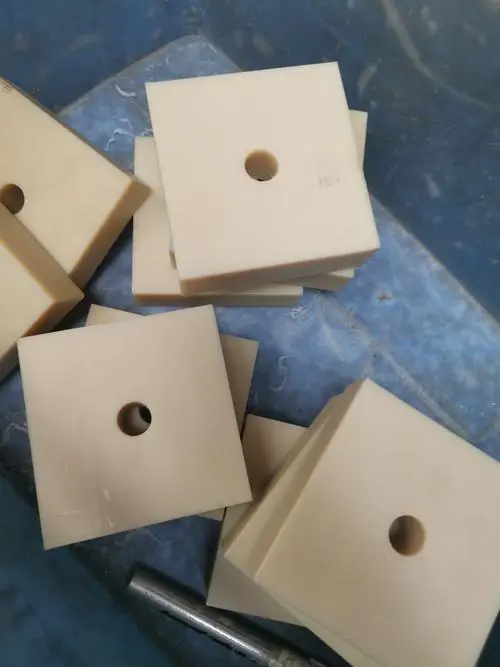
Production Lead Time and Delivery Time
Typical Lead Time from Order Placement to Delivery
Our standard lead time ranges from 1 to 2 weeks, including:
- Order Confirmation and Planning: 1-2 days
- Procurement of Materials: 2-3 days
- Machining and Production: 5-7 days
- Quality Control and Inspection: 1-2 days
- Packaging and Shipping: 1-2 days
Expedited Orders
We offer expedited production for urgent orders, often reducing lead time to 1-7 days. Please inform us at the time of order placement for expedited options.
How Do We Ensure Consistency and Quality for Each Batch of Parts?
Quality Control Measures
- Advanced Inspection Tools: CMMs, laser scanners, and precision gauges.
- In-Process Monitoring: Real-time deviation detection and correction.
- Material Verification: Comprehensive testing for conformity.
- Surface Finish Analysis: Profilometers for surface quality standards.
- Environmental Controls: Controlled environments for accuracy.
Ensuring Consistency and Quality
- Standard Operating Procedures (SOPs): Uniformity in production stages.
- First Article Inspection (FAI): Thorough inspections before full-scale production.
- Statistical Process Control (SPC): Monitoring and controlling variations.
- Lot Traceability: Tracking materials and processes.
- Final Inspection and Testing: Ensuring parts meet specifications before shipment.
Our commitment to stringent quality control measures ensures consistent, high-quality parts for your projects.
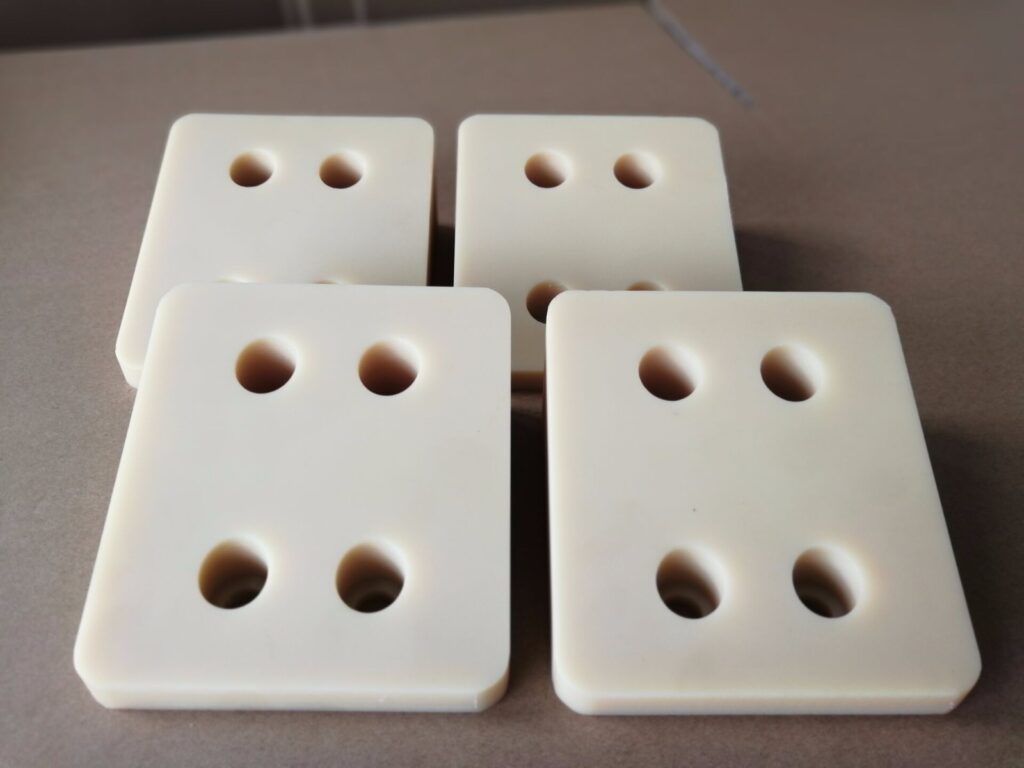

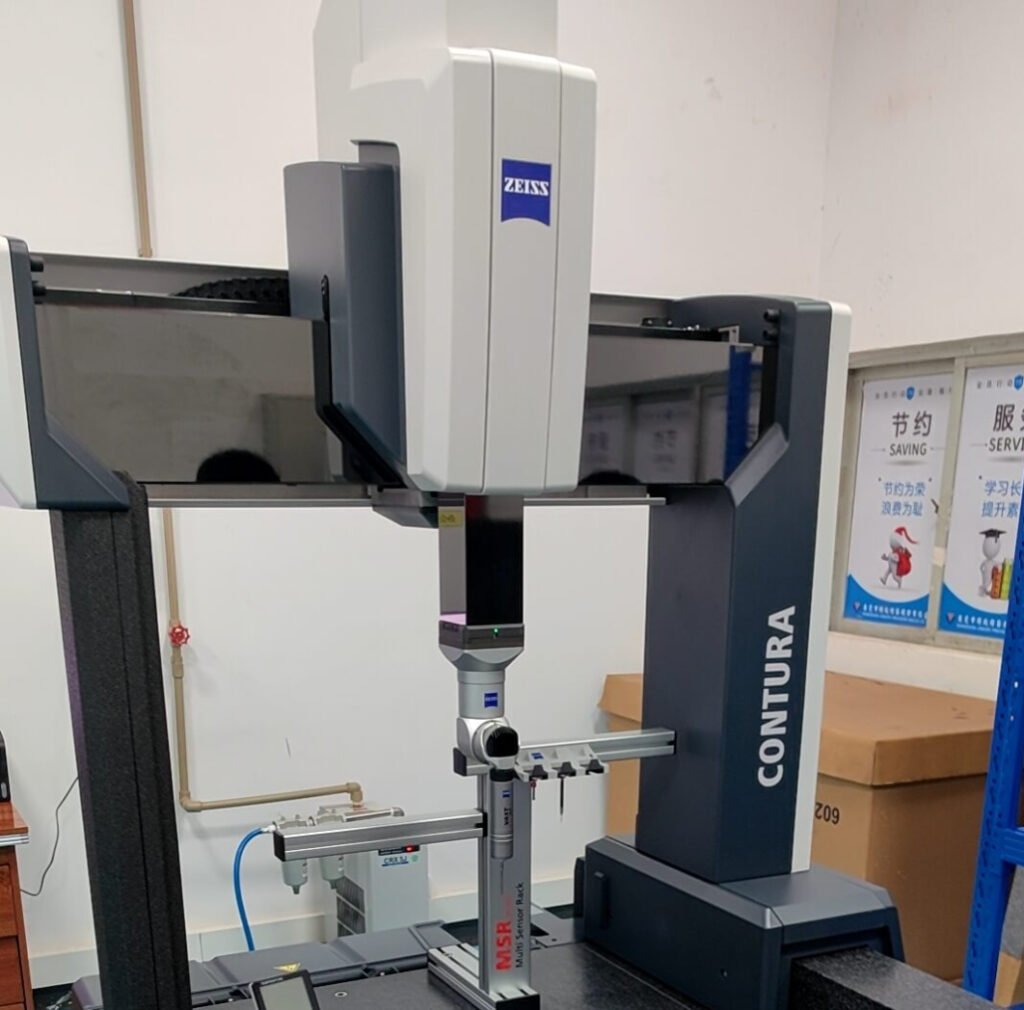
Why Modo Rapid is Your Trusted Partner for Nylon Projects
At Modo Rapid, we combine extensive experience, advanced technology, and a skilled team to deliver high-quality Nylon parts.
- Rich Experience: Over a decade in Nylon machining for various industries.
- Advanced CNC Technology: Cutting-edge equipment for precision.
- Skilled Team: Expert engineers dedicated to quality.
- Stringent Quality Control: Rigorous measures at every stage.
- Customer-Centric Approach: Tailored solutions with open communication.
- Innovative Solutions: Continuous R&D for competitive solutions.
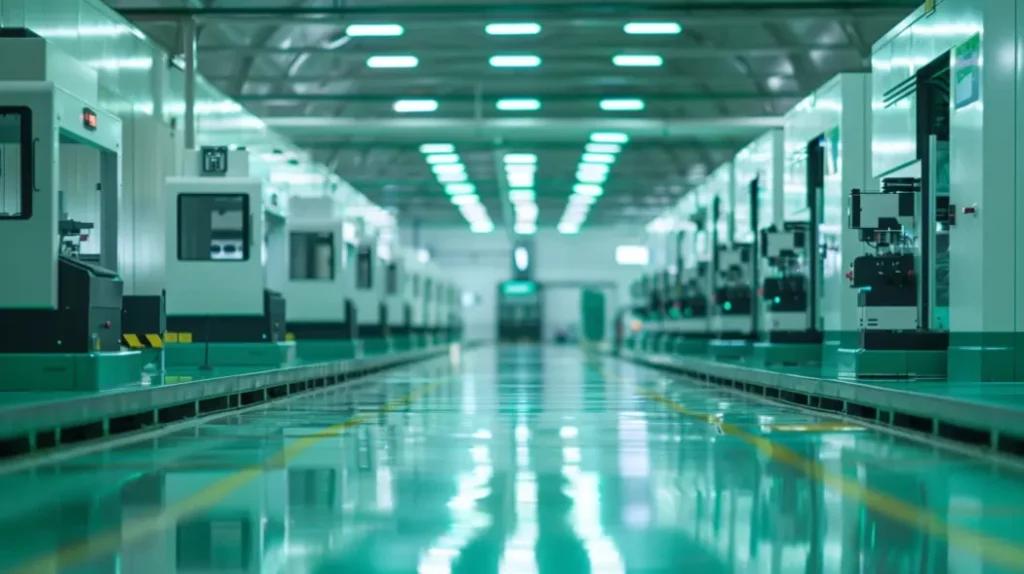
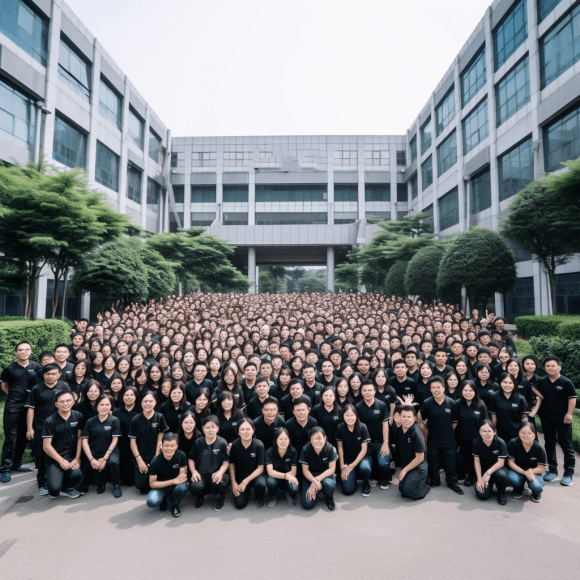
Client Feedback & Reviews
Ensuring Your Compliance with Environmental and Industry Standards
At Modo Rapid, we prioritize your need for environmentally responsible and industry-compliant manufacturing processes.
Meeting Your Environmental and Industry Standards: Our operations are designed to align with stringent environmental and industry regulations, ensuring that your projects not only meet but exceed these standards.
Certifications That Matter to You:
- ISO 9001: Guaranteeing consistent quality and continuous improvement in every product you receive.
- ISO 14001: Demonstrating our commitment to environmental management, so you can trust our sustainable practices.
- RoHS Compliance: Ensuring our materials are free from hazardous substances for your safety and peace of mind.
- REACH Compliance: Managing chemicals responsibly in our products to meet your regulatory requirements.
- IATF 16949: Meeting the rigorous quality management standards required for the automotive industry, ensuring the highest quality for your automotive projects.

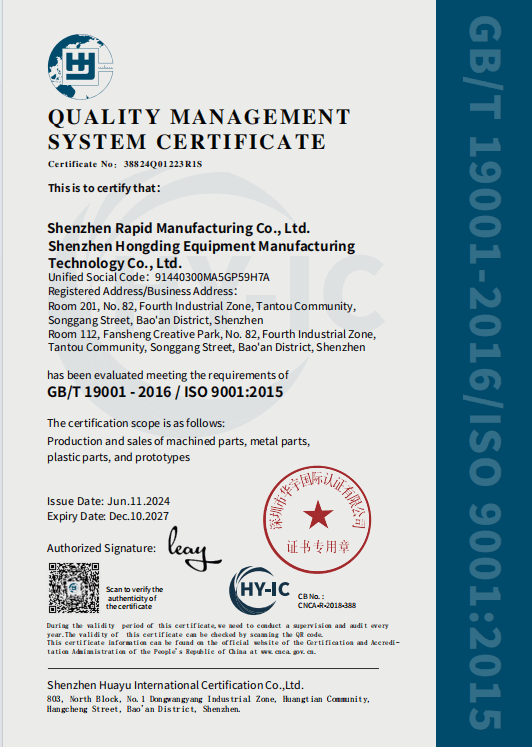
FAQ
Nylon 6 offers:
- Lower density
- Better toughness
- Better surface appearance
- Lower processing temperature
Nylon 6/6 offers:
- Higher temperature resistance
- Higher strength
- Higher stiffness
- Lower moisture absorption
- Better abrasion resistance
Nylon (PA) is a high-performance thermoplastic known for its high strength, ability to maintain mechanical properties at elevated temperatures, and chemical resistance. It is also lightweight, weighing 1/7th as much as bronze, making it an excellent replacement for metal in various applications.
Typical applications of nylon include gears, industrial bearings, nozzles, sheaves, and wear pads. It is often used in place of metal due to its lightweight properties.
Nylon is a thermoplastic, which means it melts when heated, unlike thermosets that remain set once formed. Nylon offers ease of machining and tight tolerances due to its inherent strength, toughness, and dimensional stability. However, it requires careful handling to prevent deformation and the use of non-aromatic, air-based coolants to achieve optimal surface finishes and close tolerances.
Annealing nylon helps to increase its ductility and reduce hardness, making it easier to machine. This process reduces the likelihood of surface cracks and internal stresses in the material.
Tungsten Carbide Alloy Tooling is recommended for machining nylon. It is also important to keep the part very cool, support it well, and use non-aromatic, air-based coolants.
To prevent contamination, AIP Precision Machining designs, heat-treats, and machines only plastics, with any sub-manufactured metalwork processed outside their facility. This approach ensures the highest level of sanitation and reduces the risk of metallic cross-contamination.
PA66, also known as Nylon, is a synthetic polymer widely used in various industries due to its excellent mechanical properties. It is a high-strength, rigid, and tough thermoplastic with good chemical resistance and the ability to withstand high temperatures. Nylon is used in automotive, aerospace, and electronics industries, among others.
- PA6: Better impact resistance and solubility resistance, but absorbs more water, leading to brittleness in warm and dry environments.
- PA66: Higher temperature resistance, strength, stiffness, lower moisture absorption, and better abrasion resistance.
The recommended tooling for machining PA66 or Nylon should be made of high-speed steel or carbide with a sharp cutting edge. The tool angles should be between 10 and 15 degrees.
- Cutting Speeds: 200 to 300 feet per minute.
- Feed Rates: 0.002 to 0.008 inches per tooth.
- Depth of Cut: 0.020 to 0.050 inches.
The fixturing methods should provide maximum support and stability. Recommended methods include clamping and vacuum chucking.
Coolant should be constantly flowed to reduce heat generated during machining. The coolant should be water-soluble and compatible with the material.
- High strength: Can withstand heavy loads and stresses effectively.
- Chemical resistance: Resistant to various chemicals, including oils, fuels, and solvents.
- Heat resistance: Maintains mechanical properties even at high temperatures.
- Easy machinability: Can be easily machined using standard equipment.
- Automotive: Gears, bearings, fuel tanks.
- Aerospace: Engine components, landing gear, electrical connectors.
- Electronics: Cable ties, connectors, switches.
- Industrial: Rollers, gears, bearings for heavy-duty machinery.
- Consumer Goods: Kitchen utensils, sporting equipment, toys.
An experienced machining provider ensures the highest quality plastic parts by selecting the right tooling, cutting parameters, and fixturing methods. This results in successful machining processes and high-quality final products.
Custom Nylon Parts for Your Project!
Experience tailored excellence with our high-precision Nylon parts. We manufacture to your exact specifications, ensuring top-quality results and cost efficiency. Choose Modo Rapid for seamless, customized Nylon part solutions. Send us your specifications and let us help you achieve your goals.
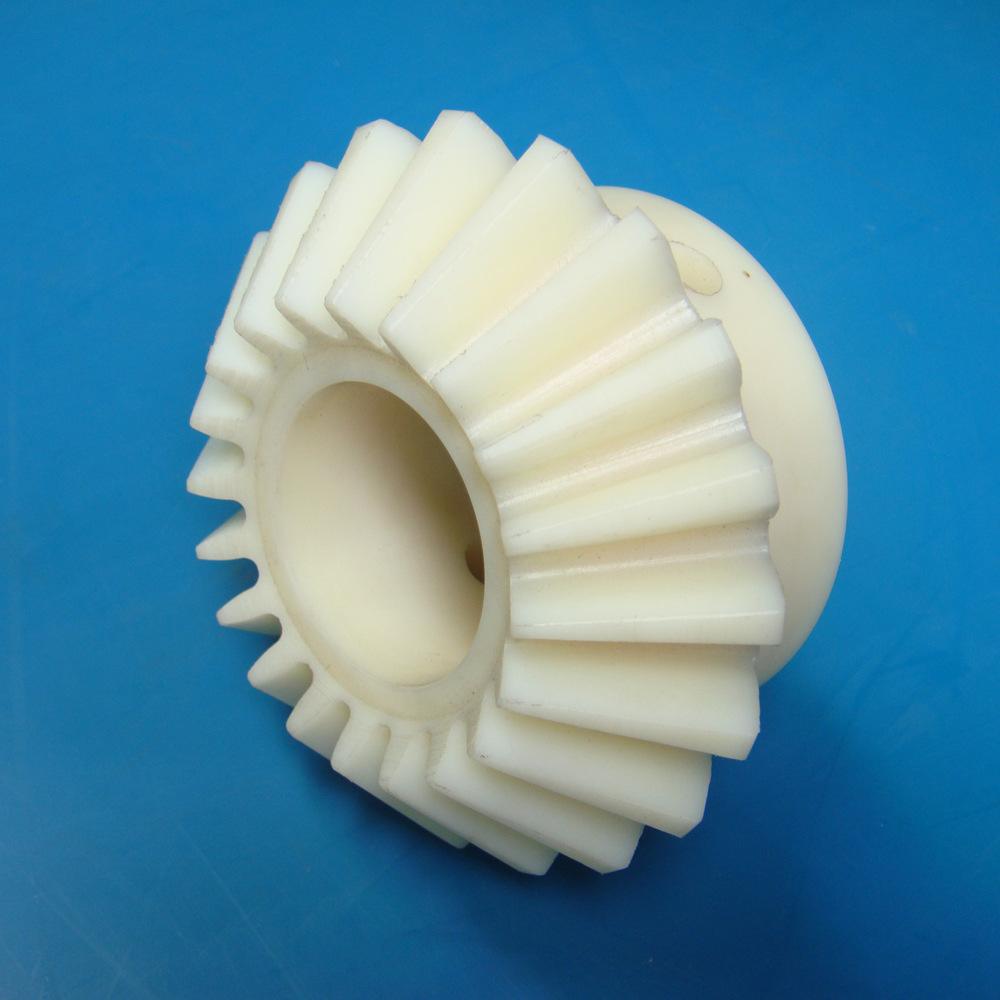
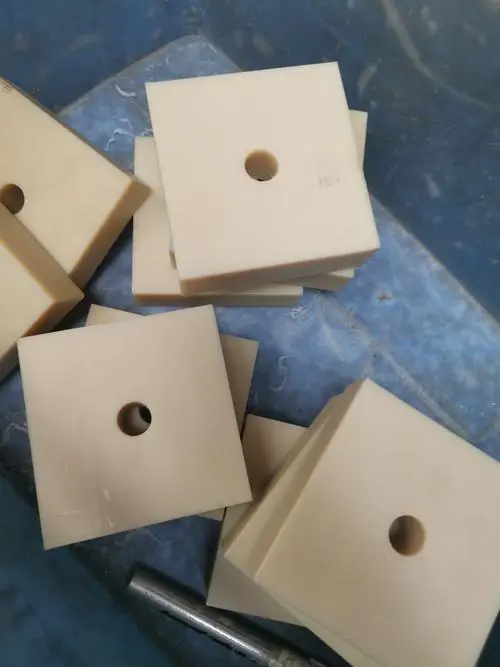
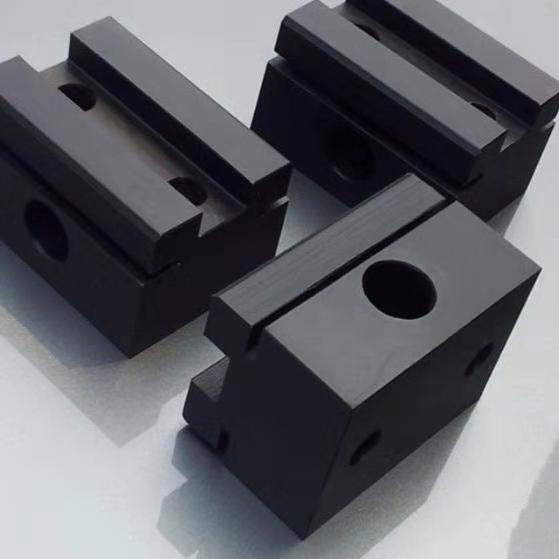
Get a quote for custom Nylon parts
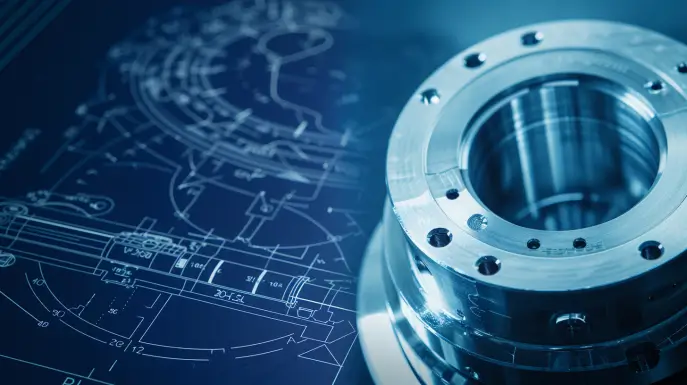