CNC Milling
- Machined Metal and Plastic Prototypes & Production Parts in as Fast as 1-7 Days.
- ISO 9001 & IATF 16949
- 100% Factory Price
Our CNC Milling Capabilities

3-Axis Milling
This is the most basic type, suitable for flat and simple 3D surface machining. The workpiece can only move along the X, Y, and Z axes.
4-Axis Milling
An additional rotational axis (usually the A or B axis) is added, allowing the workpiece to rotate around one axis. It is suitable for complex geometries and angles.
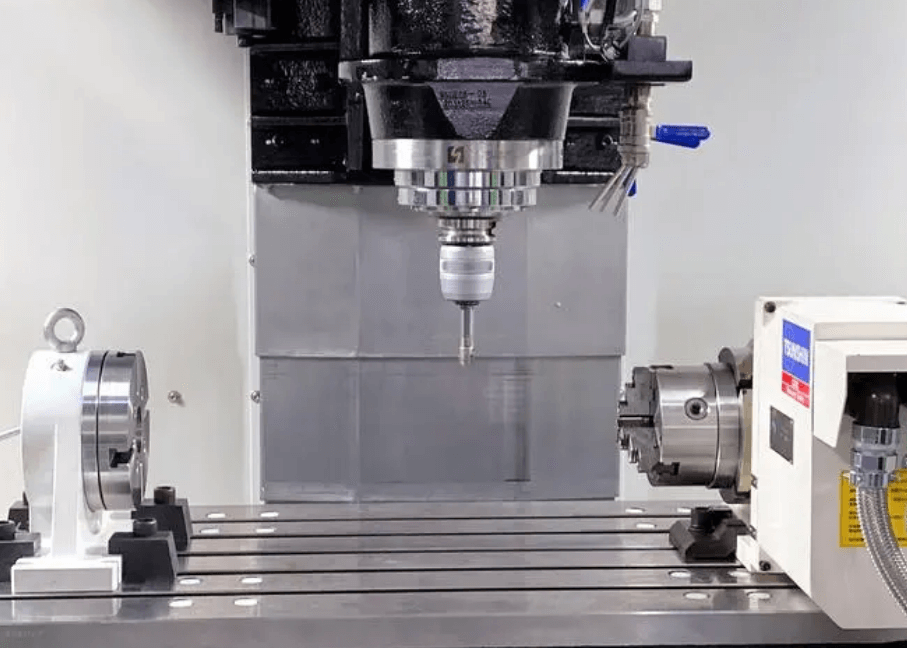
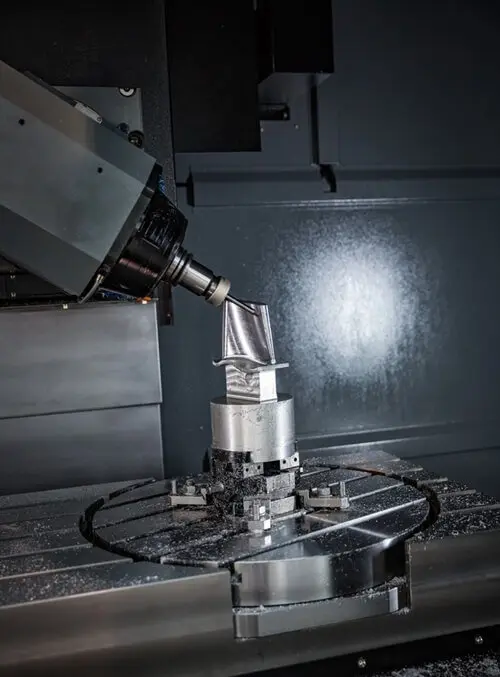
5-Axis Milling
The workpiece can move along five axes (X, Y, Z, and two rotational axes). This type is ideal for very complex parts, such as those used in aerospace and medical devices.
Vertical Milling Machine
The spindle is perpendicular to the worktable surface, making it suitable for machining larger and heavier workpieces.
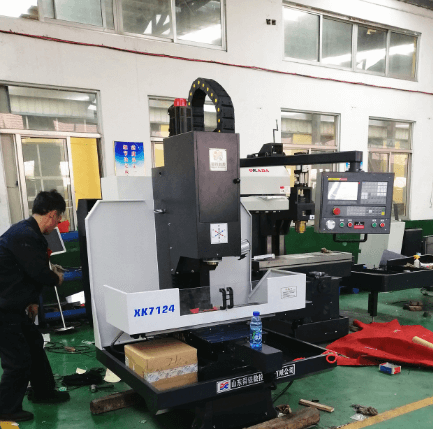
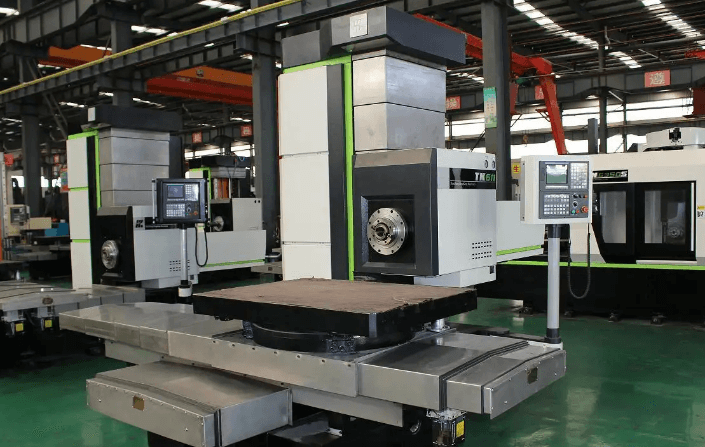
Horizontal Milling Machine
The spindle is parallel to the worktable surface, suitable for machining long, bar-shaped workpieces and multi-surface machining.
Gantry Milling Machine
It features a large gantry frame, making it suitable for machining extremely large workpieces and complex shapes.
- XYZ Axis Travel: 500026001000mm
- Table Size: 5000*2400mm
- Spindle Nose to Table Distance: 350-1350mm
- T-slot Size: 2812200mm
- Gantry Width: 2700mm
- Spindle Speed: 6000rpm
- Spindle Power: 55kw
- Table Load Capacity: 18T
- Control System: FANUC 0i-MF
- Manufacture Year: 2016
- Overall Dimensions: 1230063005000mm
- Machine Weight: 47t
- Features: Three-axis linear guideways, BT50 gear head
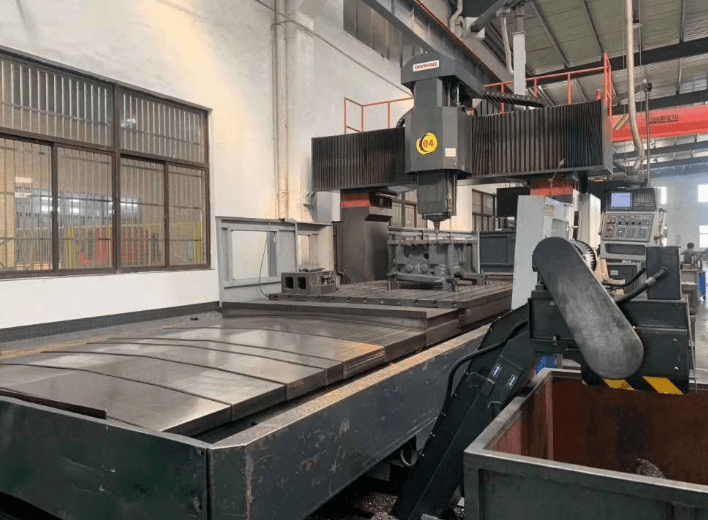
Work with A Certified Company
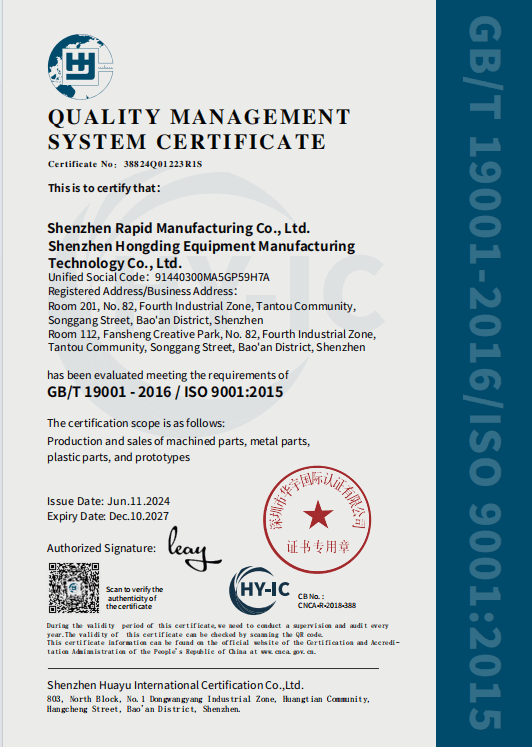

CNC Milling Design Advice and Capabilities
3-Axis Milling | 4-Axis Milling | 5-Axis Milling | |
---|---|---|---|
Max. Part size | 1800 x 950 x 480 mm (66.9 x 37.4 x 18.9 in) | 1200 x 800 x 600 mm (47.2 x 31.5 x 23.6 in) | 950 x 850 x 570 mm (37.4 x 33.5 x 22.4 in) |
Min. Part size | 12 x 12 x 12 mm (0.47 x 0.47 x 0.47 in) | 12 x 12 x 12 mm (0.47 x 0.47 x 0.47 in) | 12 x 12 x 12 mm (0.47 x 0.47 x 0.47 in) |
Min. Feature size | Ø 0.8 mm (Ø 0.031 in) | Ø 0.8 mm (Ø 0.031 in) | Ø 0.8 mm (Ø 0.031 in) |
Standard tolerance | Metals: +/- 0.10 mm (+/- 0.004 in) | Metals: +/- 0.10 mm (+/- 0.004 in) | Metals: +/- 0.10 mm (+/- 0.004 in) |
Plastics: +/- 0.15 mm (+/- 0.006 in) | Plastics: +/- 0.15 mm (+/- 0.006 in) | Plastics: +/- 0.15 mm (+/- 0.006 in) | |
Lead time | As low as 7 days for fewer than 50 parts | As low as 8 days for fewer than 50 parts | As low as 9 days for fewer than 50 parts |
CNC Machining Materials
Material Type | Examples |
---|---|
Metals | Aluminum (6061, 7075, 2024, 5052) |
Stainless Steel (304, 316, 17-4 PH) | |
Steel (A36, 1018, 1045, 4140) | |
Brass (C360) | |
Copper (C110, C101) | |
Titanium (Grade 2, Grade 5) | |
Magnesium | |
Nickel Alloys (Inconel, Monel) | |
Tool Steel (D2, O1, A2) | |
Plastics | ABS |
Nylon (PA6, PA66) | |
Polycarbonate (PC) | |
Polyethylene (PE) | |
Polypropylene (PP) | |
PEEK | |
PTFE (Teflon) | |
PVC | |
Delrin (POM) | |
Acrylic (PMMA) | |
Composites | Carbon Fiber |
Fiberglass | |
Specialty Materials | Ceramics (Alumina, Zirconia) |
Graphite | |
G10 | |
Phenolic | |
Other Materials | Wood (various types) |
Foam |
Customize Your CNC Prototype Parts According to Drawings
At Modo Rapid, we excel in creating high-precision CNC prototype parts customized to your exact designs. Our advanced 5-axis CNC machines allow us to craft complex and detailed components with exceptional accuracy. To guarantee top-notch quality, we employ ZEISS Coordinate Measuring Machines (CMM) for thorough inspection and verification.
As a premier factory in Shenzhen, we recognize the vital role that precision and quality play in your projects. Collaborate with us for unmatched precision, efficiency, and the expertise necessary to realize your prototypes.
Post-Processing Techniques |
---|
Anodizing, Bead Blasting, Black Oxide, Brushing |
Chromate Conversion Coating, Deburring, Electropolishing, Heat Treatment |
Laser Engraving, Painting, Passivation, Plating (Nickel, Chrome, Zinc) |
Polishing, Powder Coating, Sandblasting, Shot Peening |
Tumbling, Ultrasonic Cleaning, Vibratory Finishing, Welding |
Quality Checks at Every Stage for Your Milled Parts
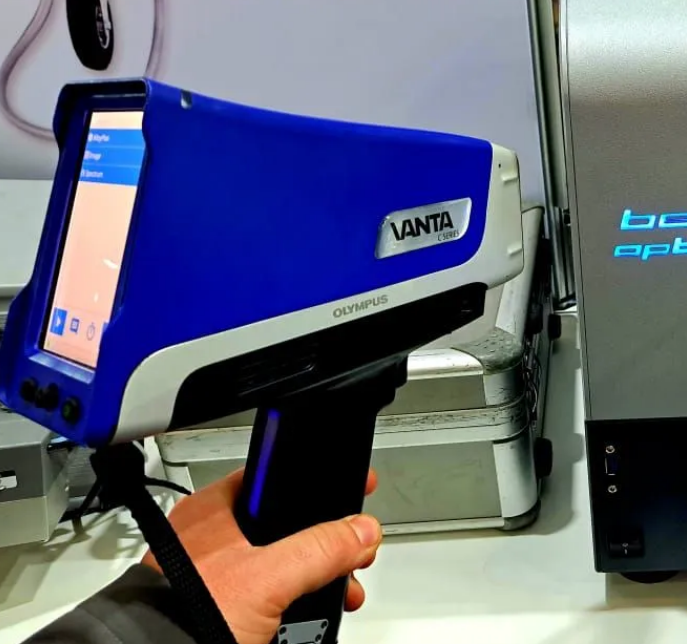
Initial Material Inspection:
Equipment: Optical Emission Spectrometer (OES) or X-ray Fluorescence (XRF) Analyzer. Purpose: Verify the composition and quality of raw materials before production begins.
In-Process Dimensional Inspection:
Equipment: Coordinate Measuring Machine (CMM) and Vernier Calipers. Purpose: Ensure parts meet dimensional specifications during various stages of machining.
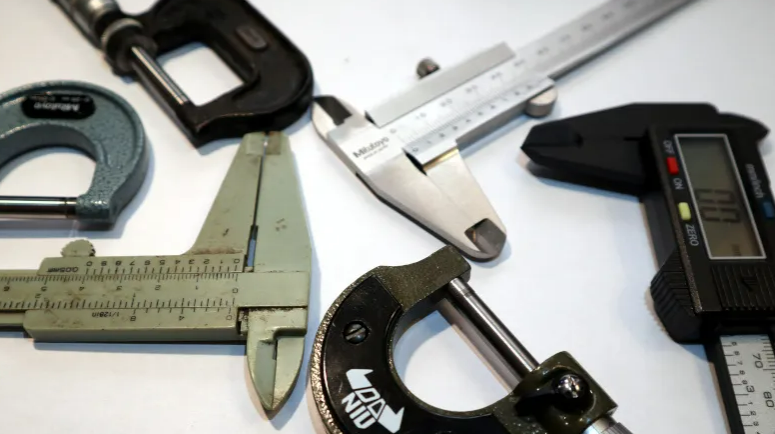
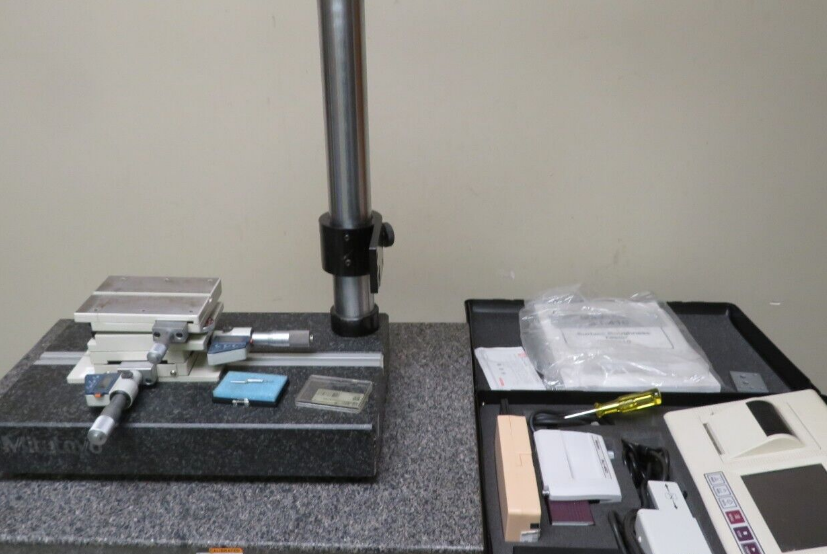
Surface Finish Inspection:
Equipment: Surface Roughness Tester. Purpose: Check the surface texture and finish to meet the required standards.
Final Quality Inspection:
Equipment: 2 ZEISS Coordinate Measuring Machines (CMM) and Optical Comparator. Purpose: Conduct a comprehensive inspection of the finished part to verify all dimensions, tolerances, and overall quality.
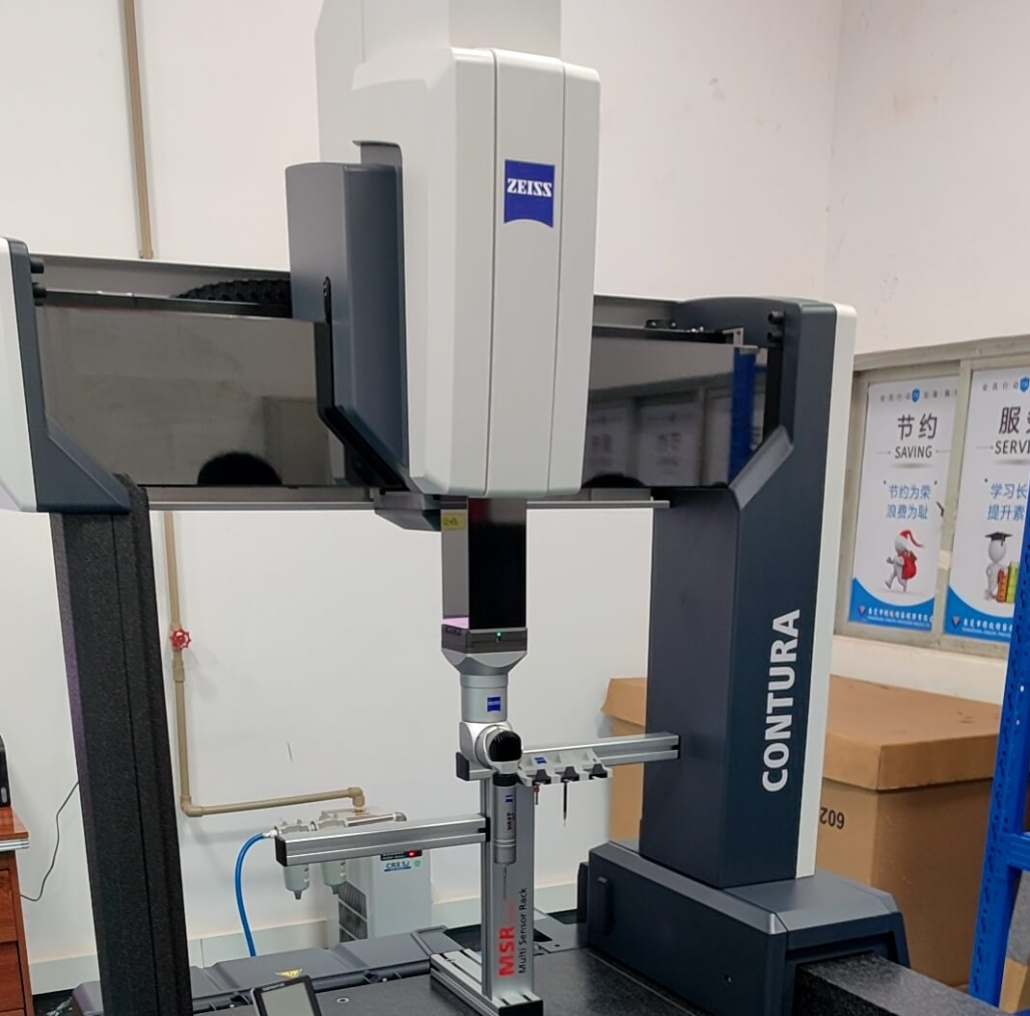
2 ZEISS CMMs for your project 24/7
We are a 24-hour facility with technicians working 3 shifts. For many of our customer’s urgent projects, we use our 2 ZEISS CMM’s to inspect the parts and make sure your project goes smoothly.
Quality Inspections We Perform for Your Parts
Delivery Time
When selecting a supplier, it’s crucial to consider their production cycle and delivery capabilities, especially for urgent projects. Our commitment to timely delivery is unwavering, ensuring your project stays on track.
For prototypes, we offer the following delivery times:
- 1-30 pieces: Delivery within 7 days
- 31-100 pieces: Delivery within 15 days
- 100-500 pieces: Delivery within 18 days
We can reprioritize orders in case of project emergencies. Please let us know in advance.
Cost Control
We understand that cost efficiency is crucial when sourcing CNC prototypes. Our competitive pricing ensures that you get the best value without compromising on quality. Here’s how we keep costs low:
- Processing Fees: By utilizing advanced CNC machinery, we reduce production time and costs. For instance, our 5-axis milling can complete complex parts in fewer setups, saving both time and money.
- Material Costs: We have established relationships with top material suppliers, allowing us to procure high-quality materials at discounted rates. For example, our bulk purchasing of aluminum alloys translates to significant savings for our clients.
- Shipping Fees: Our strategic partnerships with leading logistics companies ensure efficient and cost-effective shipping. For instance, our expedited shipping options for urgent orders do not come with the high price tag you’d expect.
By choosing us, you’re guaranteed low-cost, high-quality CNC prototypes that meet your budget and performance requirements. For example, a recent project involving 50 custom parts was delivered within budget and ahead of schedule, demonstrating our commitment to cost efficiency and timely delivery.
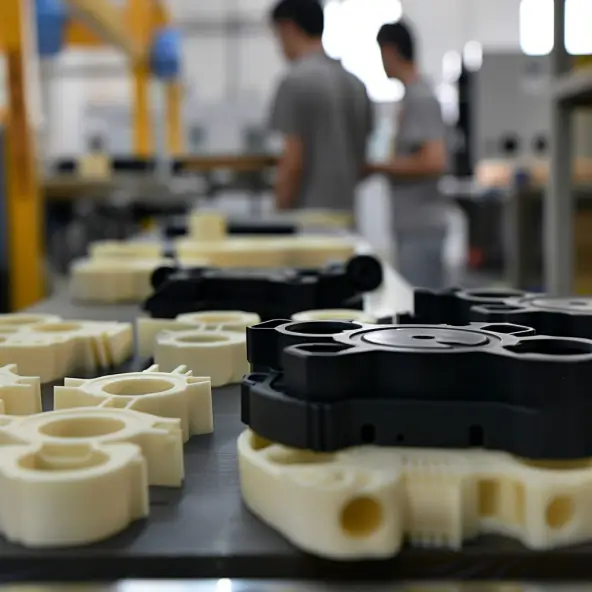
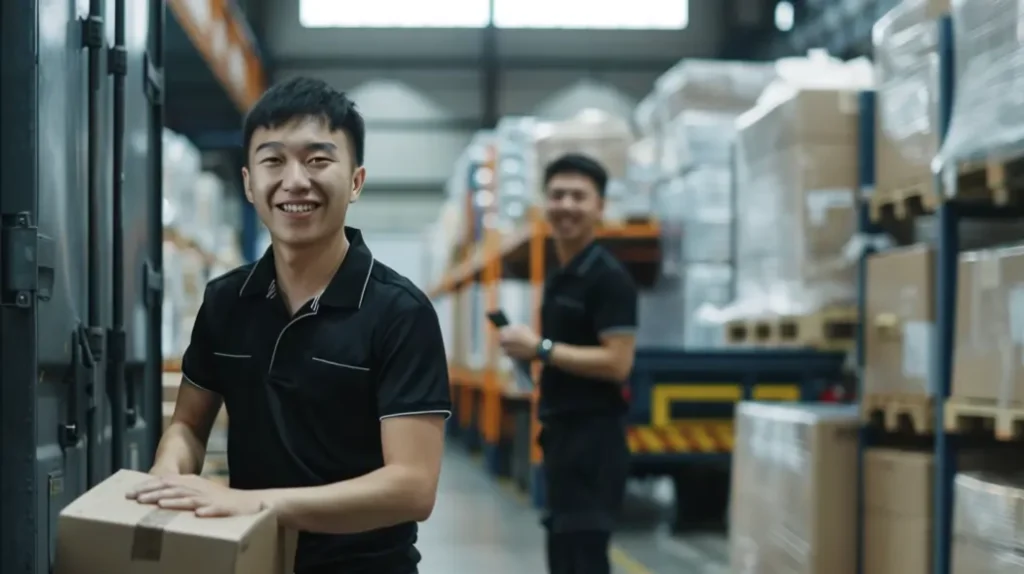
Communication Efficiency
Effective communication is key. We are online 16 hours daily, providing swift, expert support globally, ensuring seamless project management.
Flexibility
We specialize in prototypes and small batches, accommodating even single orders with flexible production and payment options.
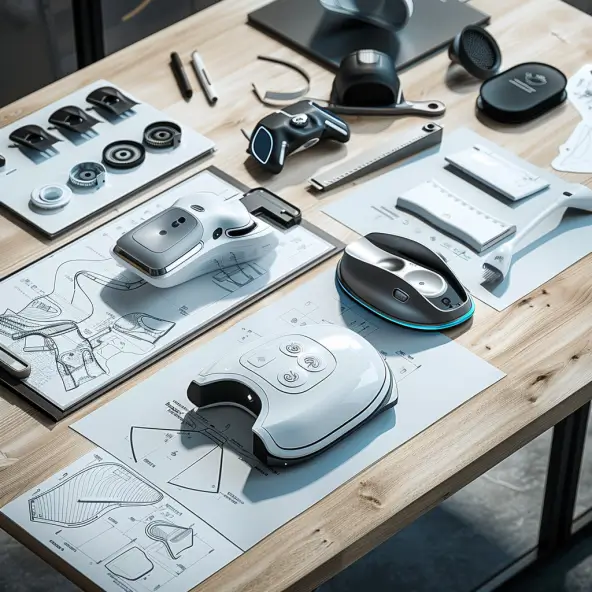
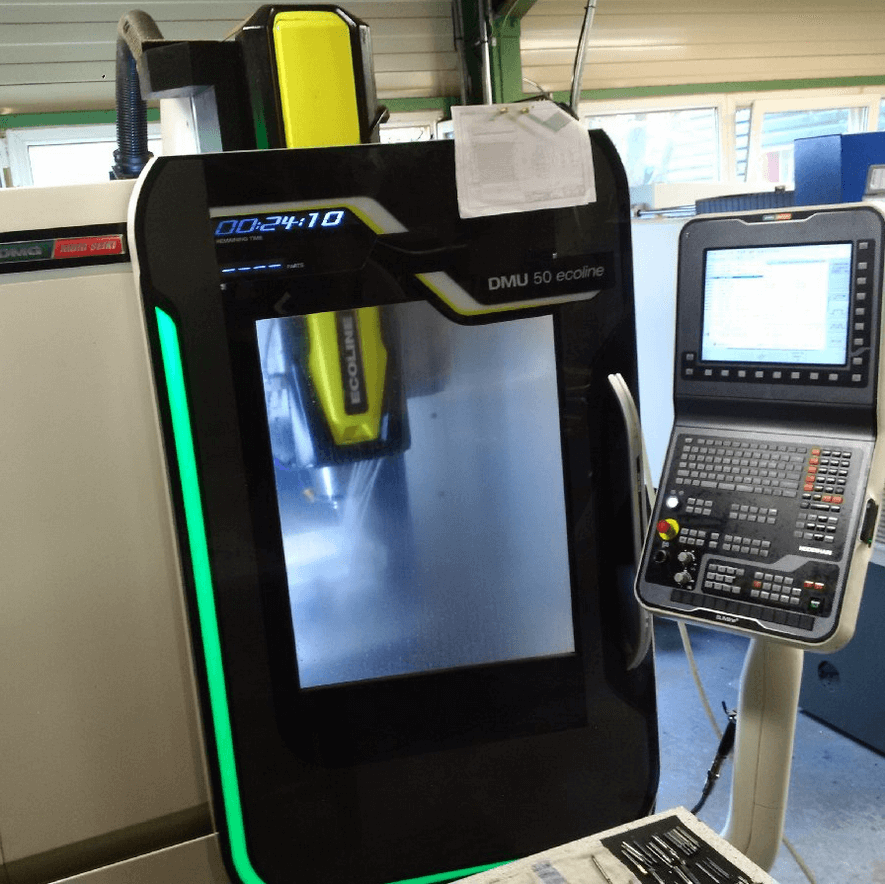
Confidentiality
We sign NDAs before discussing design details. Production occurs in temperature-controlled, sealed facilities.
Our employees and the company are also bound by confidentiality and non-compete agreements. The company and its employees are in a stable relationship to ensure that your designs are safe
Custom CNC Parts for Every Industry
Precision-engineered solutions tailored to meet the unique demands of automotive, aerospace, medical, and more industries, ensuring superior performance and reliability.

Frequently Ask Questions
We have a rigorous quality control process, including:
- Use of advanced CMM machines for precise measurement.
- Strict adherence to ISO 9001 and IATF 16949 standards.
- Continuous in-process inspections and final quality checks. Our production environment is temperature-controlled and sealed to maintain optimal conditions.
Yes, we specialize in prototyping and small batch production. We are highly flexible and can accommodate orders as small as a single prototype, ensuring the same level of quality and attention to detail as larger orders.
We prioritize the confidentiality of your designs and project information. We sign Non-Disclosure Agreements (NDAs) before discussing any design details. Our entire production process takes place in temperature-controlled, sealed facilities to ensure maximum security and confidentiality.
We have established partnerships with leading logistics companies to ensure efficient and cost-effective shipping. We provide expedited shipping options for urgent orders and handle all customs documentation to facilitate smooth international deliveries.
Yes, our engineering and project teams are available to provide comprehensive technical support and consultation. From initial design review to final production, we guide you through each step to ensure your project’s success.
For urgent orders, we prioritize production schedules and utilize expedited shipping services to meet tight deadlines. Our flexible production capabilities allow us to quickly adapt to your needs and ensure timely delivery without compromising quality.
- Accuracy: High precision and repeatability in part production.
- Efficiency: Faster production times compared to manual milling.
- Consistency: Uniform quality across all produced parts.
- Reduced Labor: Less manual labor required due to automation.
- Complex Parts: Capable of producing parts with complex geometries.
- Material Variety: Can work with a wide range of materials.
- Scalability: Suitable for both small batch and large-scale production.
- Cost-Effective: Reduces waste and increases efficiency, lowering overall production costs.
- Initial Cost: High initial investment for CNC machines and software.
- Maintenance: Requires regular maintenance and skilled technicians.
- Programming: Needs skilled programmers to create and manage CNC programs.
- Setup Time: Initial setup can be time-consuming, especially for complex parts.
- Material Limitations: Some materials may require special tooling or parameters.
- Complexity: Complex machines and processes may require significant training and experience.
- Tool Wear: Cutting tools can wear out quickly and need frequent replacement.
- Energy Consumption: CNC machines consume significant amounts of energy.