CNC Turning
- Machined Metal and Plastic Prototypes & Production Parts in as Fast as 1-7 Days.
- ISO 9001 & IATF 16949
- 100% Factory Price
Table of Contents
Achieving Ra 0.8 Surface Finish Right Off the Lathe
Our skilled team of technicians and operators, with years of experience, are adept at handling the machining requirements of various complex components.
By utilizing advanced cutting tools and optimizing cutting parameters, we ensure that the surface finish of our lathe-turned parts achieves an impressive Ra 0.8 right off the machine, meeting the highest standards of surface smoothness.
Our CNC Turning Capabilities
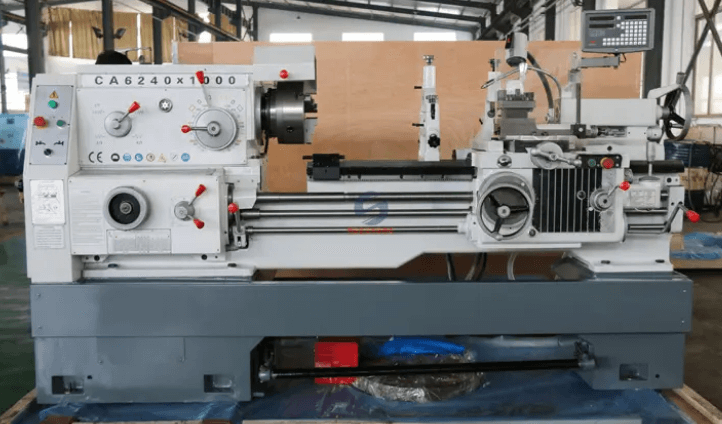
Horizontal Lathes
- The most common type of lathe, with a horizontally placed spindle, ideal for machining cylindrical workpieces.
- Typically used for turning, boring, grooving, and drilling operations.
Vertical Lathes
- Featuring a vertically placed spindle, suitable for machining large-diameter, short-length workpieces.
- Commonly used for turning large discs, flanges, and the internal and external surfaces of large parts.
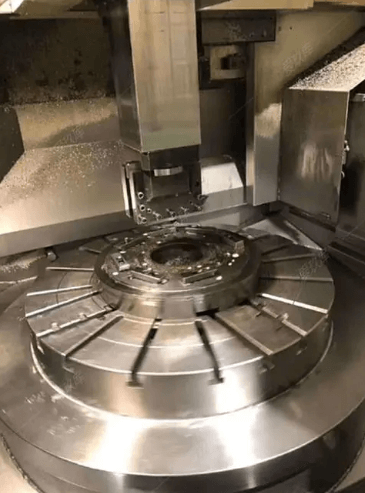
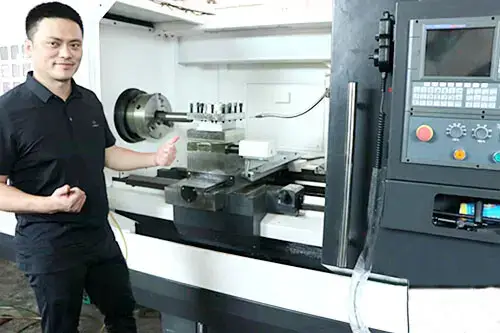
CNC Lathes
- Controlled by computer numerical control (CNC) systems, enabling high precision and high-efficiency automated machining.
- Ideal for complex surfaces, irregularly shaped parts, and mass production.
Work with A Certified Company
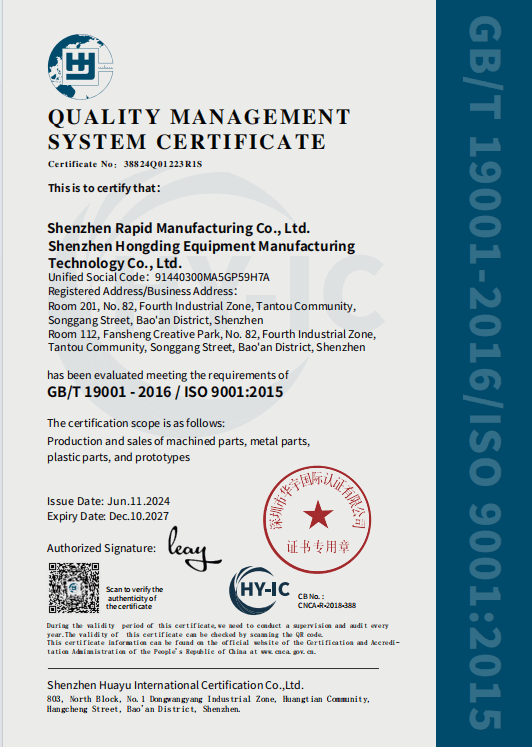

CNC Turning Design Advice and Capabilities
Horizontal Lathes | Vertical Lathes | CNC Lathes | |
---|---|---|---|
Max Part Size | 13.8 in diameter, 21.6 in length (350 mm diameter, 550 mm length) | Up to 60 in diameter (1524 mm) | 12 x 16 in (305 x 406 mm), bar capacity 1.75 in (45 mm) |
Min Part Size | 0.47 x 0.47 x 0.47 in (12 x 12 x 12 mm) | 0.47 x 0.47 x 0.47 in (12 x 12 x 12 mm) | 0.47 x 0.47 x 0.47 in (12 x 12 x 12 mm) |
Min Feature Size | Ø 0.031 in (Ø 0.8 mm) | Ø 0.031 in (Ø 0.8 mm) | Ø 0.031 in (Ø 0.8 mm) |
Standard Tolerance | Metals: +/- 0.004 in (+/- 0.10 mm) Plastics: +/- 0.006 in (+/- 0.15 mm) | Metals: +/- 0.004 in (+/- 0.10 mm) Plastics: +/- 0.006 in (+/- 0.15 mm) | Metals: +/- 0.004 in (+/- 0.10 mm) Plastics: +/- 0.006 in (+/- 0.15 mm) |
Lead Time | As low as 7 days for fewer than 50 parts | As low as 8 days for fewer than 50 parts | As low as 9 days for fewer than 50 parts |
Other Features | 8-inch chuck size, spindle speed up to 4500 rpm, high torque | Handles heavy, large workpieces with high precision and surface finish | High-performance, high-volume production, rapid speeds, high thermal stability |
CNC Machining Materials
Material Type | Examples |
---|---|
Metals | Aluminum (6061, 7075, 2024, 5052) |
Stainless Steel (304, 316, 17-4 PH) | |
Steel (A36, 1018, 1045, 4140) | |
Brass (C360) | |
Copper (C110, C101) | |
Titanium (Grade 2, Grade 5) | |
Magnesium | |
Nickel Alloys (Inconel, Monel) | |
Tool Steel (D2, O1, A2) | |
Plastics | ABS |
Nylon (PA6, PA66) | |
Polycarbonate (PC) | |
Polyethylene (PE) | |
Polypropylene (PP) | |
PEEK | |
PTFE (Teflon) | |
PVC | |
Delrin (POM) | |
Acrylic (PMMA) | |
Composites | Carbon Fiber |
Fiberglass | |
Specialty Materials | Ceramics (Alumina, Zirconia) |
Graphite | |
G10 | |
Phenolic | |
Other Materials | Wood (various types) |
Foam |
Customize Your CNC Prototype Parts According to Drawings
At Modo Rapid, we excel in creating high-precision CNC prototype parts customized to your exact designs. Our advanced 5-axis CNC machines allow us to craft complex and detailed components with exceptional accuracy. To guarantee top-notch quality, we employ ZEISS Coordinate Measuring Machines (CMM) for thorough inspection and verification.
As a premier factory in Shenzhen, we recognize the vital role that precision and quality play in your projects. Collaborate with us for unmatched precision, efficiency, and the expertise necessary to realize your prototypes.
Post-Processing Techniques |
---|
Anodizing, Bead Blasting, Black Oxide, Brushing |
Chromate Conversion Coating, Deburring, Electropolishing, Heat Treatment |
Laser Engraving, Painting, Passivation, Plating (Nickel, Chrome, Zinc) |
Polishing, Powder Coating, Sandblasting, Shot Peening |
Tumbling, Ultrasonic Cleaning, Vibratory Finishing, Welding |
Quality Checks at Every Stage for Your Milled Parts
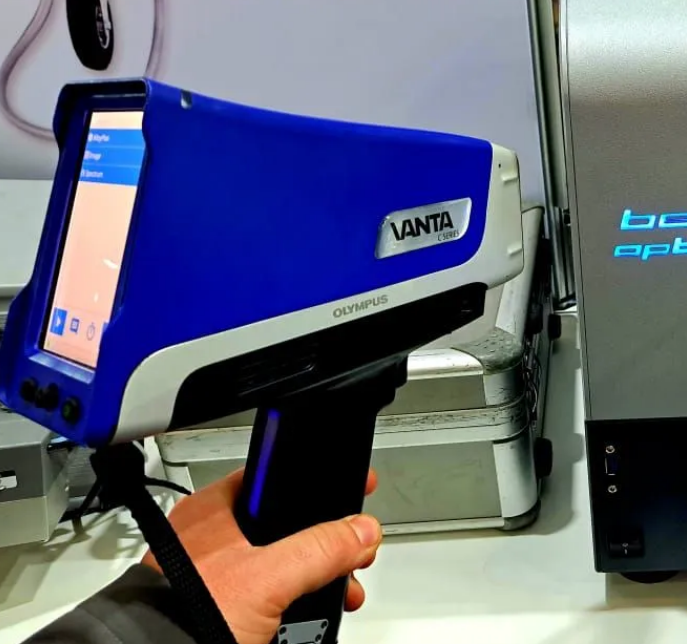
Initial Material Inspection:
Equipment: Optical Emission Spectrometer (OES) or X-ray Fluorescence (XRF) Analyzer. Purpose: Verify the composition and quality of raw materials before production begins.
In-Process Dimensional Inspection:
Equipment: Coordinate Measuring Machine (CMM) and Vernier Calipers. Purpose: Ensure parts meet dimensional specifications during various stages of machining.
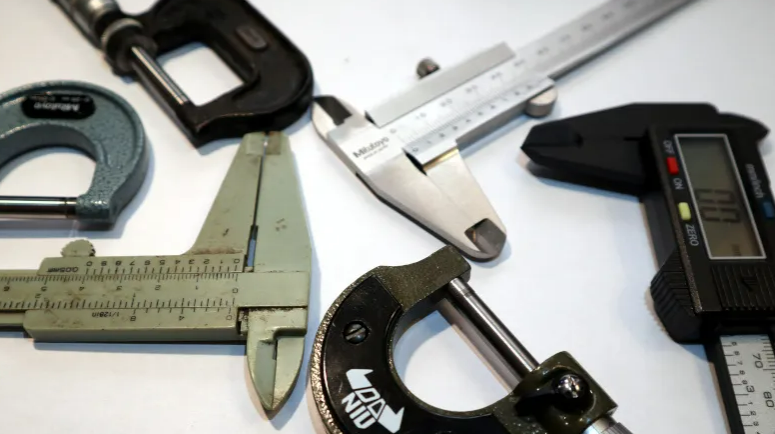
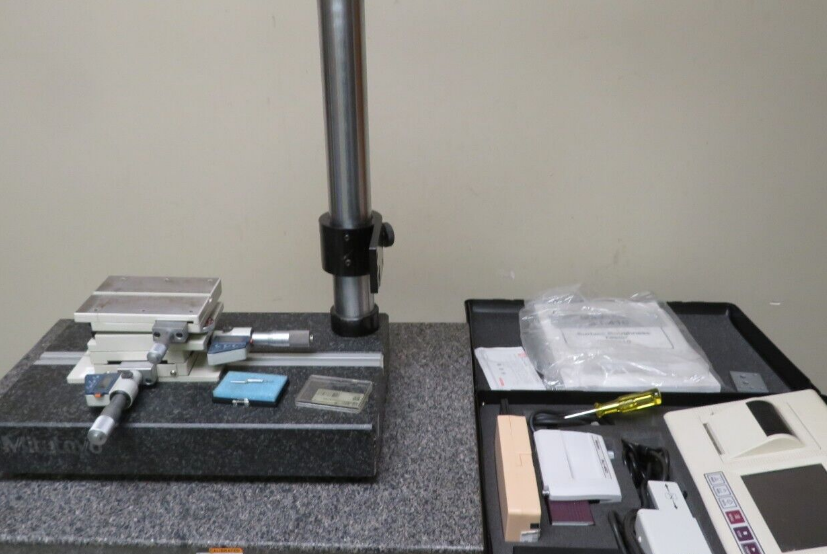
Surface Finish Inspection:
Equipment: Surface Roughness Tester. Purpose: Check the surface texture and finish to meet the required standards.
Final Quality Inspection:
Equipment: 2 ZEISS Coordinate Measuring Machines (CMM) and Optical Comparator. Purpose: Conduct a comprehensive inspection of the finished part to verify all dimensions, tolerances, and overall quality.
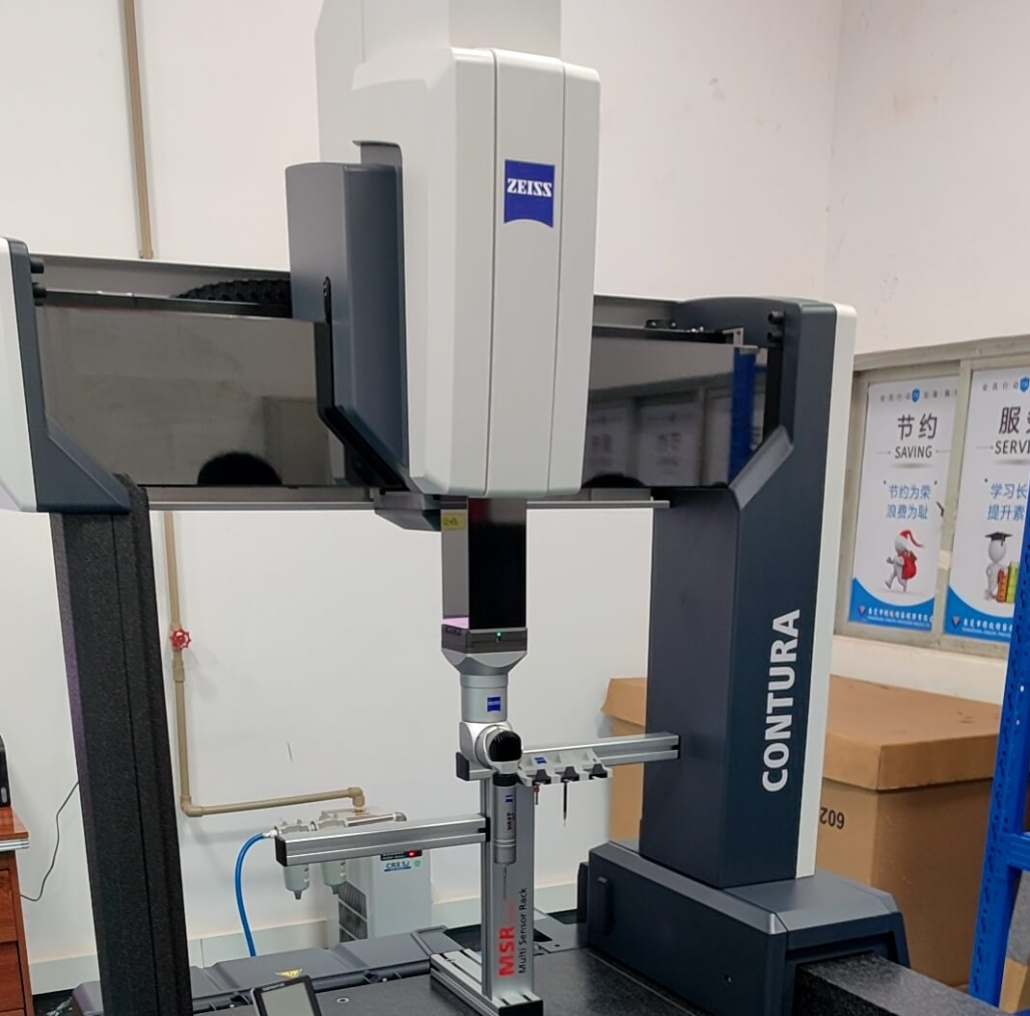
2 ZEISS CMMs for your project 24/7
We are a 24-hour facility with technicians working 3 shifts. For many of our customer’s urgent projects, we use our 2 ZEISS CMM’s to inspect the parts and make sure your project goes smoothly.
Quality Inspections We Perform for Your Parts
CNC Turning Delivery Time
When selecting a CNC turning supplier, considering their production cycle and delivery capabilities is crucial, especially for urgent projects. We prioritize timely delivery to ensure your project remains on schedule.
For CNC turning prototypes, we offer the following delivery times:
- 1-30 pieces: Delivery within 7 days
- 31-100 pieces: Delivery within 15 days
- 100-500 pieces: Delivery within 18 days
In case of project emergencies, we can reprioritize orders. Please inform us in advance to accommodate your urgent needs.
Cost Control
We understand that cost efficiency is crucial when sourcing CNC turning parts. Our competitive pricing ensures that you get the best value without compromising on quality. Here’s how we keep costs low:
Processing Fees: By utilizing advanced CNC turning machinery, we reduce production time and costs. For instance, our high-precision lathes can complete complex parts in fewer setups, saving both time and money.
Material Costs: We have established relationships with top material suppliers, allowing us to procure high-quality materials at discounted rates. For example, our bulk purchasing of aluminum alloys translates to significant savings for our clients.
Shipping Fees: Our strategic partnerships with leading logistics companies ensure efficient and cost-effective shipping. For instance, our expedited shipping options for urgent orders do not come with the high price tag you’d expect.
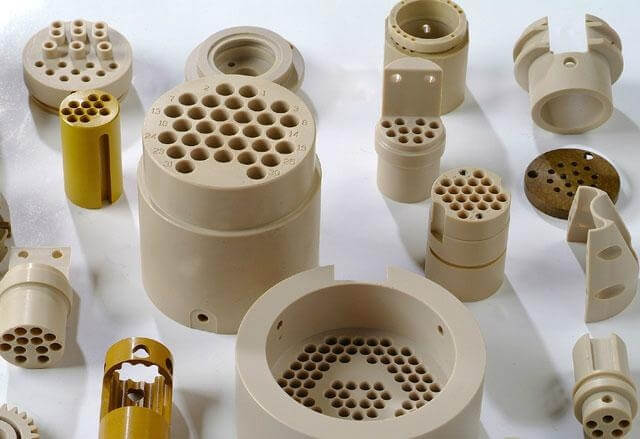
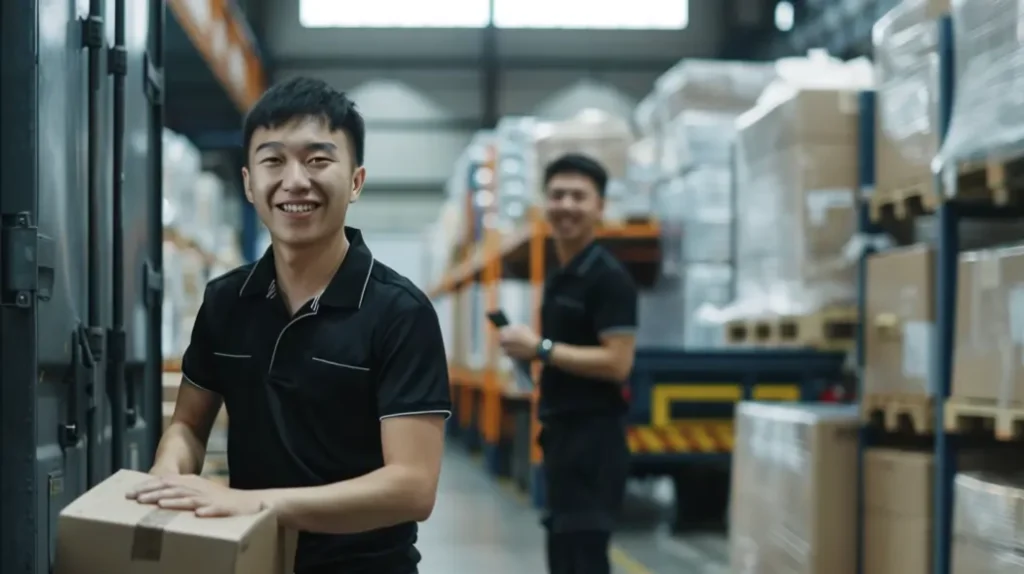
Communication Efficiency
Effective communication is key. We are online 16 hours daily, providing swift, expert support globally, ensuring seamless project management.
Flexibility
We specialize in prototypes and small batches, accommodating even single orders with flexible production and payment options.
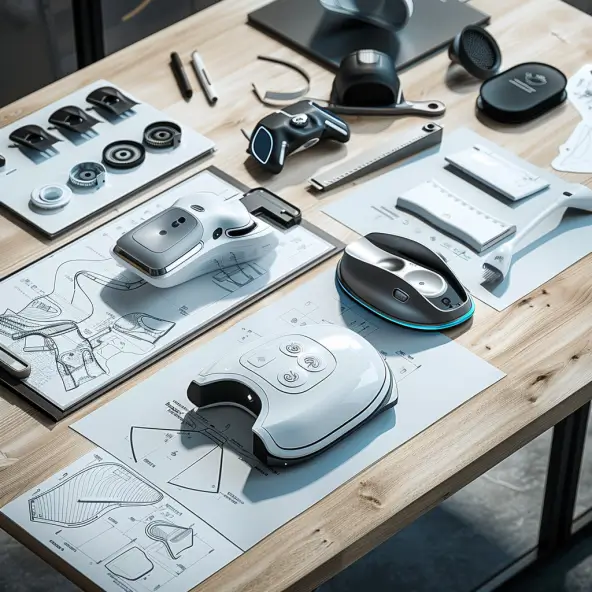
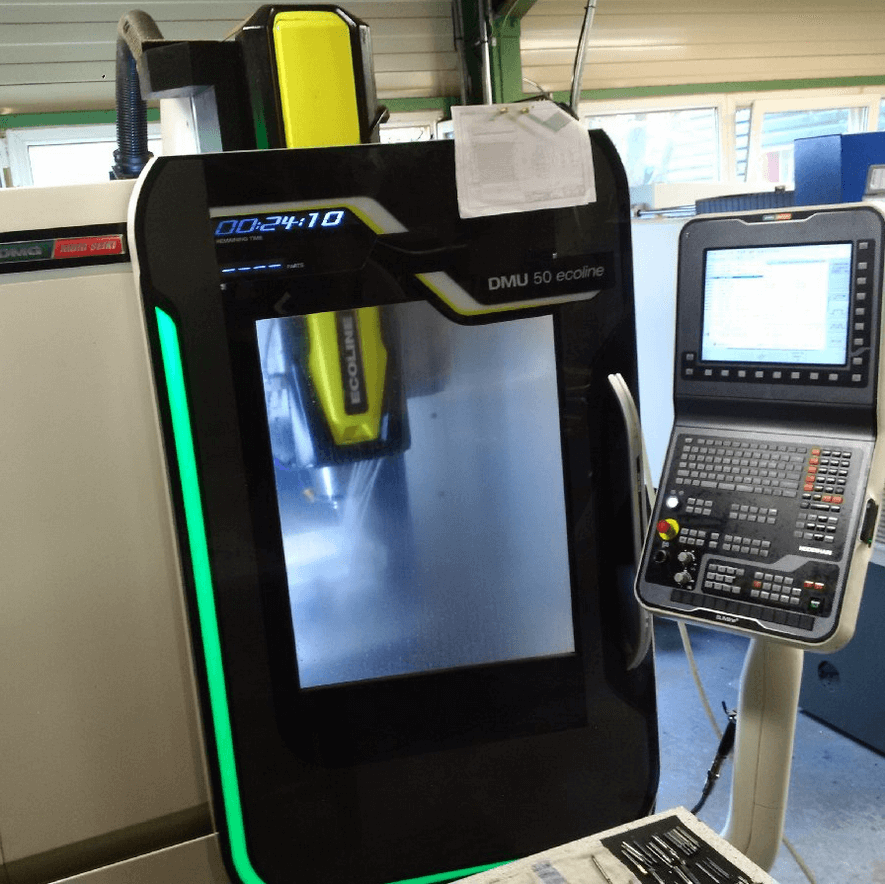
Confidentiality
We sign NDAs before discussing design details. Production occurs in temperature-controlled, sealed facilities.
Our employees and the company are also bound by confidentiality and non-compete agreements. The company and its employees are in a stable relationship to ensure that your designs are safe
Custom CNC Parts for Every Industry
Precision-engineered solutions tailored to meet the unique demands of automotive, aerospace, medical, and more industries, ensuring superior performance and reliability.

Frequently Ask Questions
We have a rigorous quality control process, including:
- Use of advanced CMM machines for precise measurement.
- Strict adherence to ISO 9001 and IATF 16949 standards.
- Continuous in-process inspections and final quality checks. Our production environment is temperature-controlled and sealed to maintain optimal conditions.
Yes, we specialize in prototyping and small batch production. We are highly flexible and can accommodate orders as small as a single prototype, ensuring the same level of quality and attention to detail as larger orders.
We prioritize the confidentiality of your designs and project information. We sign Non-Disclosure Agreements (NDAs) before discussing any design details. Our entire production process takes place in temperature-controlled, sealed facilities to ensure maximum security and confidentiality.
We have established partnerships with leading logistics companies to ensure efficient and cost-effective shipping. We provide expedited shipping options for urgent orders and handle all customs documentation to facilitate smooth international deliveries.
Yes, our engineering and project teams are available to provide comprehensive technical support and consultation. From initial design review to final production, we guide you through each step to ensure your project’s success.
For urgent orders, we prioritize production schedules and utilize expedited shipping services to meet tight deadlines. Our flexible production capabilities allow us to quickly adapt to your needs and ensure timely delivery without compromising quality.
- Accuracy: High precision and repeatability in part production.
- Efficiency: Faster production times compared to manual milling.
- Consistency: Uniform quality across all produced parts.
- Reduced Labor: Less manual labor required due to automation.
- Complex Parts: Capable of producing parts with complex geometries.
- Material Variety: Can work with a wide range of materials.
- Scalability: Suitable for both small batch and large-scale production.
- Cost-Effective: Reduces waste and increases efficiency, lowering overall production costs.
- Initial Cost: High initial investment for CNC machines and software.
- Maintenance: Requires regular maintenance and skilled technicians.
- Programming: Needs skilled programmers to create and manage CNC programs.
- Setup Time: Initial setup can be time-consuming, especially for complex parts.
- Material Limitations: Some materials may require special tooling or parameters.
- Complexity: Complex machines and processes may require significant training and experience.
- Tool Wear: Cutting tools can wear out quickly and need frequent replacement.
- Energy Consumption: CNC machines consume significant amounts of energy.
Yes, we can provide detailed inspection reports and certificates of compliance with each order as required.
Lead times vary depending on the order size and complexity, but typically range from 2 to 4 weeks. We can provide a more accurate estimate once we review your specific requirements.
We have a rigorous quality control process, including:
- Use of advanced CMM machines for precise measurement.
- Strict adherence to ISO 9001 and IATF 16949 standards.
- Continuous in-process inspections and final quality checks. Our production environment is temperature-controlled and sealed to maintain optimal conditions.
Yes, we specialize in prototyping and small batch production. We are highly flexible and can accommodate orders as small as a single prototype, ensuring the same level of quality and attention to detail as larger orders.
We prioritize the confidentiality of your designs and project information. We sign Non-Disclosure Agreements (NDAs) before discussing any design details. Our entire production process takes place in temperature-controlled, sealed facilities to ensure maximum security and confidentiality.
We have established partnerships with leading logistics companies to ensure efficient and cost-effective shipping. We provide expedited shipping options for urgent orders and handle all customs documentation to facilitate smooth international deliveries.
Yes, our engineering and project teams are available to provide comprehensive technical support and consultation. From initial design review to final production, we guide you through each step to ensure your project’s success.
We prioritize urgent orders and have the flexibility to adjust our production schedule to meet tight deadlines. Please contact us to discuss your specific needs.
Any additional fees will be clearly detailed in our quotation, ensuring full transparency.
Our standard payment terms are typically 30% upfront and 70% upon completion, but we can discuss and agree on terms that best suit your needs.
Yes, you will have a dedicated account manager who will be your main point of contact throughout the project.
We accommodate design changes and modifications by closely working with you to implement necessary adjustments while minimizing impact on the project timeline.