Fused Deposition Modeling (FDM)
Table of Contents
FDM Tolerances Overview
Feature | Standard Resolution | High Resolution |
---|---|---|
Build Envelope | 500 x 500 x 500 mm (19.68″ x 19.68″ x 19.68″) | 300 x 300 x 400 mm (11.8″ x 11.8″ x 15.7″) |
Layer Height | 100-300 μm | 50-100 μm |
XY Plane Tolerance | +/- 0.5% with a minimum of +/- 0.2 mm | +/- 0.2% with a minimum of +/- 0.1 mm |
Z Plane Tolerance | +/- 0.5% with a minimum of +/- 0.2 mm | +/- 0.2% with a minimum of +/- 0.1 mm |
Minimum Linear Feature Size | 1.5 mm (0.059″) | 0.8 mm (0.0315″) |
Minimum Radial Feature Size | 1.5 mm (0.059″) | 0.8 mm (0.0315″) |
Note: These tolerances are standard for FDM processes and can vary depending on the material, geometry, and machine setup. For more precise tolerances, a manual quote review might be necessary after successful prototype completion. General tolerances apply before any secondary finishing or post-processing unless specified otherwise
Modo Rapid offers seamless access to premium 3D printing services, utilizing cutting-edge additive manufacturing technologies.
Choose from over 40 materials and 11 finishing options to perfectly match the requirements of any project.
FDM Materials and Their Properties
Modo Rapid offers a wide range of FDM materials tailored for specific applications. Here’s an overview of available materials and their key characteristics:
Material Name | Description | Tensile Strength (MPa) | Elongation at Break (%) | Flexural Modulus (MPa) |
---|---|---|---|---|
PLA | Easy to print, biodegradable | 65 MPa | 6% | 3600 MPa |
ABS | Durable, impact-resistant | 40 MPa | 10% | 2200 MPa |
PETG | Strong, flexible, chemical-resistant | 50 MPa | 23% | 2100 MPa |
Nylon (PA 6) | Tough, wear-resistant | 50 MPa | 50% | 1700 MPa |
Polycarbonate (PC) | High strength, heat-resistant | 68 MPa | 5-12% | 2300 MPa |
TPU (Thermoplastic Polyurethane) | Flexible, rubber-like | 25 MPa | 500% | 80 MPa |
PEEK | High-performance thermoplastic | 90-100 MPa | 20-30% | 4000 MPa |
ULTEM (PEI) | High heat resistance, good electrical properties | 90 MPa | 5-10% | 3100 MPa |
These materials are suitable for various industrial and commercial applications, ensuring that you have the right material for your specific project needs
Capabilities of FDM 3D Printers
FDM 3D printing technology is highly versatile, suitable for both prototyping and full-scale production. Here are the key features of FDM technology:
Maximum Build Volume | Typical Lead Time | Dimensional Precision | Layer Thickness | Smallest Feature Size | |
---|---|---|---|---|---|
Desktop FDM for Prototyping | 200 x 200 x 200 mm (7.87 in x 7.87 in x 7.87 in) | From 2 business days | ± 0.5% with a minimum of ± 0.5 mm (± 0.0197”) | 100-300 μm | 2.0 mm |
Industrial FDM | 500 x 500 x 500 mm (19.68 in x 19.68 in x 19.68 in) | From 3 business days | ± 0.3% with a minimum of ± 0.3 mm (± 0.012”) | 50-100 μm | 1.0 mm |
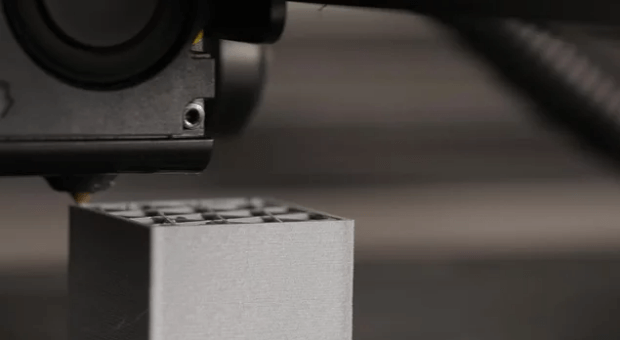
Advanced 3D Printing Solutions for Engineering with FDM
Access high-precision printed components at every stage of your product development.
Compare FDM Materials for Optimal Performance
Explore material properties and filter by application during your setup process with detailed material profiles.
Optimize Print Resolution
Adjust layer thickness in the settings menu to achieve the perfect balance between detail and production time for FDM parts.
Enhance Surface Finish Quality
Include optional post-processing configurations by uploading your drawing with marked areas for specific finishing requirements.
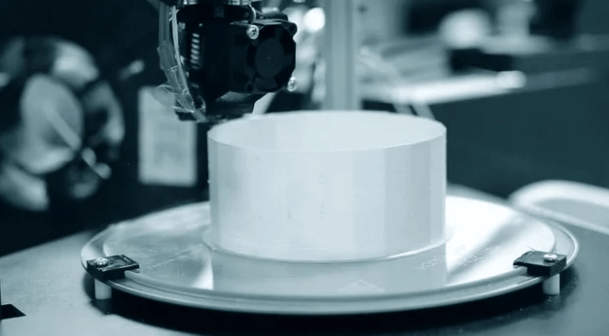
FDM Post-Processing
At Modo Rapid, we ensure that your FDM parts are of the highest quality. Post-processing options include support removal, sanding, and painting to achieve the desired finish. For functional parts, additional treatments such as annealing can be applied to enhance the mechanical properties.
Comparison of 3D Printing Technologies
Technology | Materials | Price | Dimensional Accuracy | Strengths | Build Volume | Layer Thickness | Min. Feature Size |
---|---|---|---|---|---|---|---|
FDM | 5 | $ | ± 0.5% with a lower limit of ± 0.5 mm | Low cost, wide range of materials | 500 x 500 x 500 mm (19.68″ x 19.68″ x 19.68″) | 100-300μm | 2.0 mm (0.0787”) |
Industrial FDM | 6 | $$$$ | ± 0.3% with a lower limit of ± 0.3 mm (± 0.012″) | High repeatability, engineering-grade materials | 406 x 355 x 406 mm (15.98” x 13.97” x 15.98″) | 100-330μm | 2.0 mm (0.0787”) |
Prototyping SLA | 8 | $$ | ± 0.3% with a lower limit of ± 0.3 mm (± 0.012″) | Smooth surface finish, fine detail resolution | 145 × 145 × 175 mm (5.7″ x 5.7″ x 6.8″) | 50-100μm | 0.2 mm (0.00787”) |
Industrial SLA | 3 | $$$ | ± 0.2% with a lower limit of ± 0.13 mm (± 0.005″) | Smooth surface finish, large build area | 500 x 500 x 500 mm (19.68″ x 19.68″ x 19.68″) | 50-100μm | 0.2 mm (0.00787”) |
SLS | 2 | $$ | ± 0.3% with a lower limit of ± 0.3 mm (± 0.012”) | Design flexibility, no supports required | 395 x 500 x 395 mm (15.53″ x 19.68″ x 15.53″) | 100μm | 0.5 mm (0.0196”) |
MJF | 2 | $$ | ± 0.3% with a lower limit of ± 0.3 mm (0.012”) | Design flexibility, no supports required | 380 x 285 x 380 mm (14.9” x 11.2” x 14.9”) | 80μm | 0.5 mm (0.0196”) |
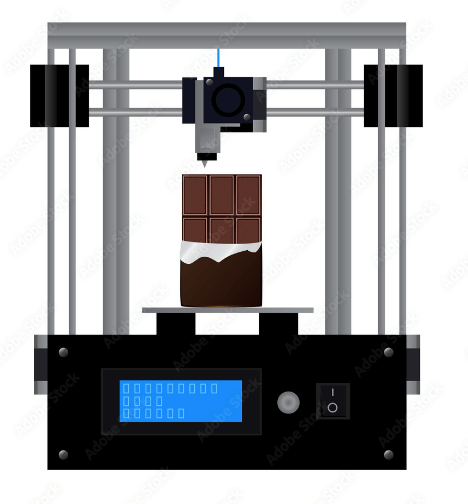
Our Commitment to High Standards in FDM 3D Printing
At Modo Rapid, we produce your custom parts with strict adherence to our manufacturing standards, ensuring that all parts and processes comply with our rigorous quality guidelines. A detailed verification of these requirements is provided in the inspection report included with every order.
- Parts are fully cured according to the material manufacturer’s specifications before shipment.
- Hollow sections are thoroughly drained of any excess material.
- All support structures are removed, and any remaining support marks are meticulously sanded smooth.
Pros & Cons of 3D Printing
FDM 3D printing excels in producing robust, durable parts with a wide range of material options. It’s cost-effective for both prototyping and full-scale production, making it an ideal choice for functional parts. FDM also allows for easy post-processing, including painting and surface finishing, providing flexibility in the final appearance of the parts.
However, FDM has its limitations. The layer-by-layer build process can result in visible layer lines, which may require additional finishing. Also, FDM typically requires support structures for overhangs, which need to be removed post-printing. While it is excellent for creating functional parts, the surface finish may not be as smooth as that achieved with technologies like SLA.
Design Guidelines for FDM 3D Printing
When designing parts for FDM 3D printing, consider the following technical specifications to achieve optimal results. For unsupported walls, a thickness of 1.0 mm (0.0393 in) is recommended, while supported walls can be as thin as 0.5 mm (0.0197 in). The minimum feature size that can be accurately printed is 2.0 mm (0.0787 in), and the smallest hole diameter should be at least 0.5 mm (0.0197 in). Additionally, for escape holes, a minimum diameter of 4.0 mm (0.157 in) is advised.
1 Free Sample for First-Time Customers
Getting free samples is the best way to inspect suppliers
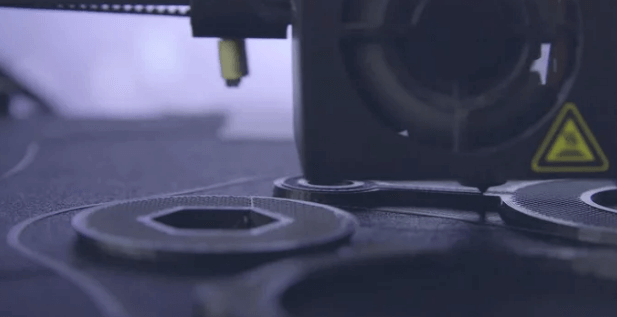
Production Feasibility Analysis
Before moving into full production, we conduct a comprehensive feasibility analysis to ensure that your design can be efficiently manufactured at scale. This step involves evaluating the materials, manufacturing processes, and potential challenges to ensure a smooth transition from prototype to production. Our team will collaborate closely with you to refine your design, optimize for manufacturability, and mitigate risks.
3D printing
Our 3D printing services offer rapid prototyping with precision and flexibility, allowing you to quickly test and iterate on your designs. We provide a range of 3D printing technologies, including SLA, SLS, and FDM, to match your specific needs, whether you require detailed models or functional parts. This stage is crucial for validating design concepts before moving to more advanced manufacturing processes.
Urethane Casting
For low to medium volume production, urethane casting offers a cost-effective solution with high fidelity to the original prototype. This process is ideal for creating durable, flexible parts that closely resemble injection-molded components. We use high-quality silicone molds and urethane resins to produce parts with excellent surface finishes and physical properties.
Injection Molding
When you’re ready for large-scale production, our injection molding services ensure consistent, high-quality parts with efficient turnaround times. We specialize in both prototype and production molds, offering a variety of materials to suit your product’s needs. From small batches to full-scale production, our injection molding capabilities are designed to meet your demands.
We Help You Go From Prototype To Production
Quality Checks at Every Stage for Your Parts
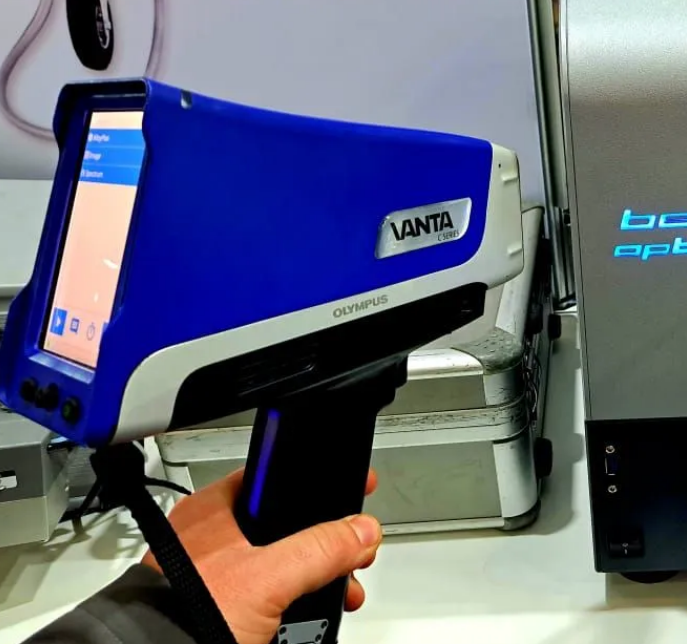
Initial Material Inspection:
Equipment: Optical Emission Spectrometer (OES) or X-ray Fluorescence (XRF) Analyzer. Purpose: Verify the composition and quality of raw materials before production begins.
In-Process Dimensional Inspection:
Equipment: Coordinate Measuring Machine (CMM) and Vernier Calipers. Purpose: Ensure parts meet dimensional specifications during various stages of machining.
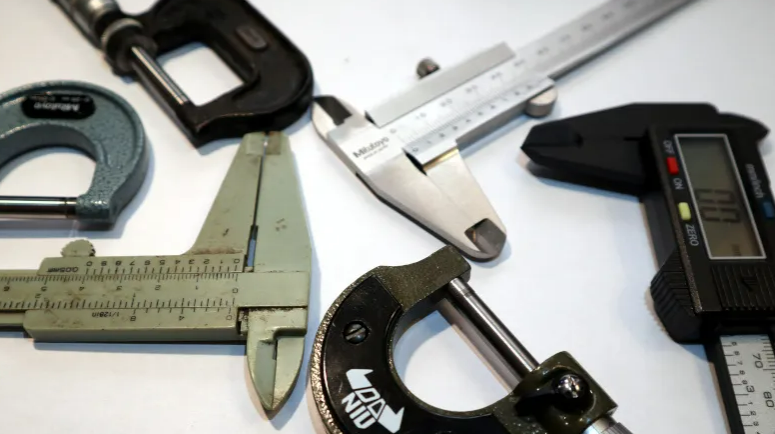
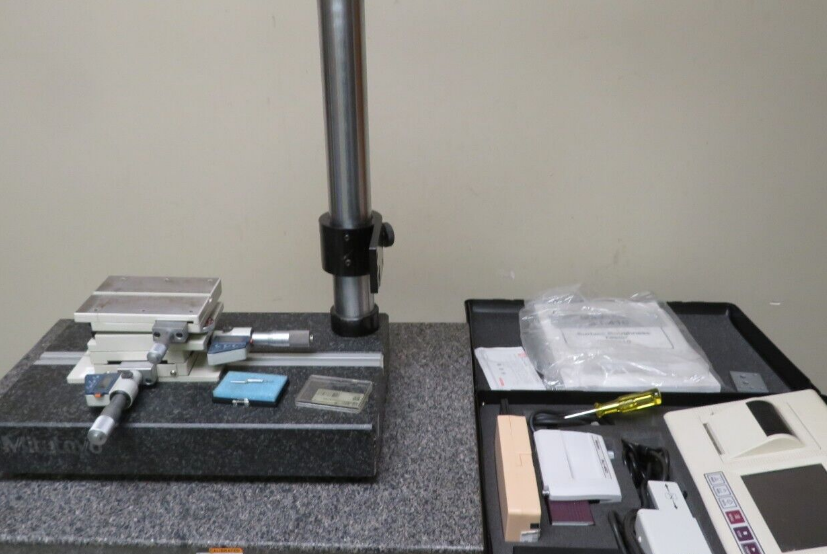
Surface Finish Inspection:
Equipment: Surface Roughness Tester. Purpose: Check the surface texture and finish to meet the required standards.
Final Quality Inspection:
Equipment: ZEISS Coordinate Measuring Machine (CMM) and Optical Comparator. Purpose: Conduct a comprehensive inspection of the finished part to verify all dimensions, tolerances, and overall quality.
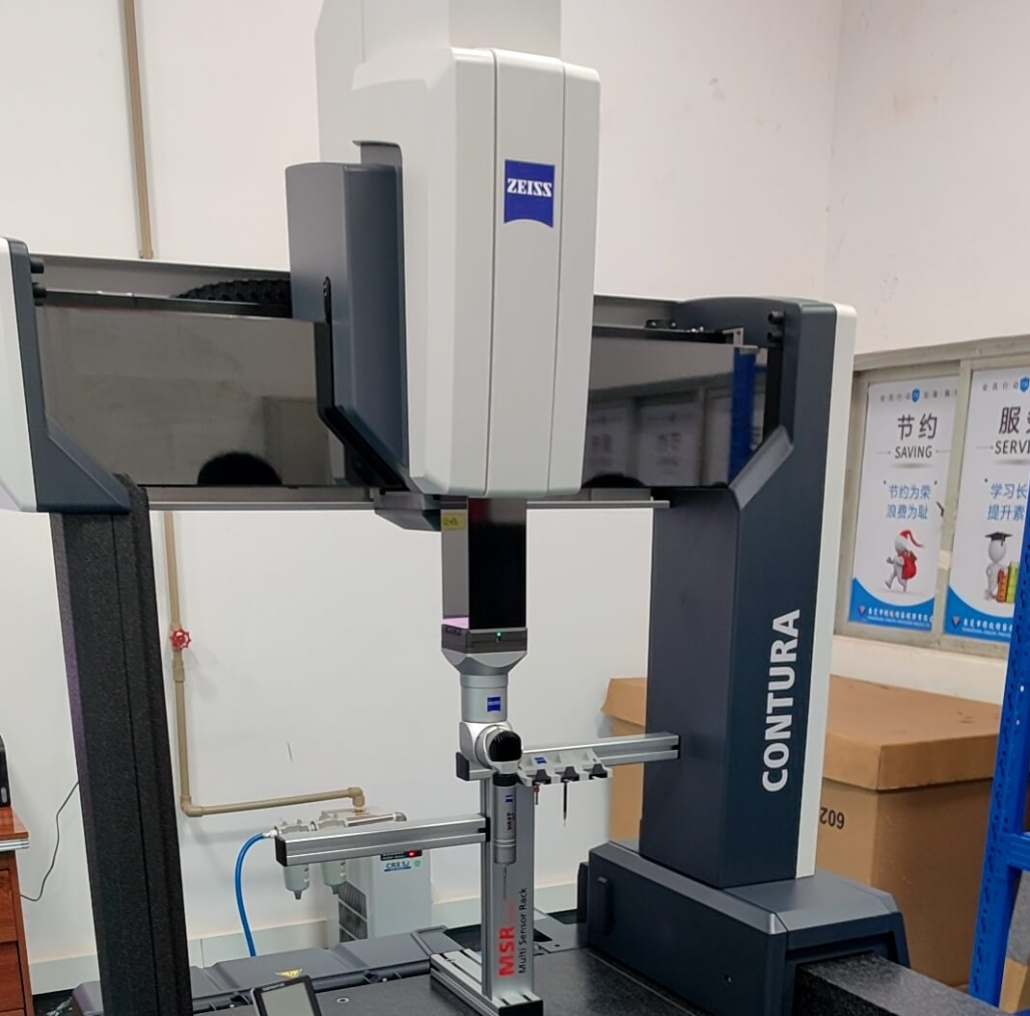
2 ZEISS CMMs for your project 24/7
We are a 24-hour facility with technicians working 3 shifts. For many of our customer’s urgent projects, we use our 2 ZEISS CMM’s to inspect the parts and make sure your project goes smoothly.
Quality Inspections We Perform for Your Parts
Rapid Printing According To Your Needs
Prototypes: 1-7 Days Lead Time
Small Batches: 7-10 Days Lead Time
Large Volumes: 10-30 Days Lead Time
100% China factory price, no middleman
24 hours factory operation, feel free to contact us
Frequently Ask Questions
Part accuracy depends on printer calibration and model complexity. Industrial FDM printers generally offer higher accuracy than desktop machines, although home 3D printer technology is improving.
FDM is relatively quick, with typical lead times of only a few days.
The combination of cost-effectiveness, material variety, and versatility makes FDM the most widely used 3D printing technology today.
FDM is primarily used for prototyping, modeling, and low-volume manufacturing. It’s also widely used in education, product development, and industrial applications, including the production of jigs, fixtures, and end-use parts.
FDM is one of the most cost-effective 3D printing methods. Desktop FDM printers and materials are generally inexpensive, making it accessible for hobbyists and professionals alike. Industrial FDM machines are more expensive but offer higher precision and speed.
FDM 3D printing is an additive manufacturing method where a spool of thermoplastic filament is fed through an extruder that heats, melts, and extrudes the plastic through a nozzle. The print head moves along the build plate to draw each layer, following instructions from a GCODE file that slices a 3D model into layers. Each layer is deposited and solidified until the entire object is built.
Filament-based 3D printing, like FDM, has become more user-friendly with features like automatic bed leveling, closed build chambers, and power failure recovery. However, FDM parts are anisotropic, meaning they are stronger in one direction. The visible layers often require post-processing, such as sanding or vapor smoothing, especially when overhangs are involved.
FDM printers use a variety of thermoplastics, with PLA (polylactic acid) being the most common due to its ease of use. ABS is another common material, known for its durability but more challenging to print with. Other materials include Nylon, PETG, TPU (for flexible parts), and even carbon-fiber-infused filaments for stronger, lightweight parts.
FDM 3D printing is used in various industries, from aerospace to automotive, for prototyping, producing jigs and fixtures, and even manufacturing complex parts. It is also widely used in education for its accessibility and cost-effectiveness. During the COVID-19 pandemic, FDM printers were used to produce essential items like face shields and swabs.
- FDM: Limited by nozzle size and filament properties, generally resulting in visible layer lines and less precise details.
- SLA: Offers the highest resolution with smooth surfaces and fine details, ideal for parts requiring high accuracy.
- SLS: Provides good resolution with slightly rougher surfaces compared to SLA but is excellent for complex and functional parts.
- FDM: Entry-level printers are affordable, starting at a few hundred dollars, but may require more labor-intensive post-processing.
- SLA: Professional printers range from $2,000 to $10,000, offering higher part quality and less post-processing labor.
- SLS: Typically more expensive, with benchtop systems starting around $30,000, but they offer high productivity and low material costs per part.
- FDM: Common thermoplastics like ABS, PLA, and PETG, with specialty materials such as nylon and carbon-fiber composites.
- SLA: Custom-formulated resins offering a wide range of properties, including tough, flexible, and biocompatible options.
- SLS: Engineering thermoplastics like nylon, TPU, and polypropylene, with options for composites and flexible materials.
- FDM: Slower due to the extrusion process; best for small batches or prototypes.
- SLA: Faster than FDM, particularly with MSLA technology, making it suitable for higher-volume production.
- SLS: Offers high throughput by packing many parts in a single build, making it ideal for low to mid-volume production.
Yes, many businesses use multiple 3D printing technologies together. FDM is often used for quick prototypes, SLA for high-detail and functional parts, and SLS for durable, complex geometries. Each technology complements the others, offering a comprehensive solution for various stages of product development.
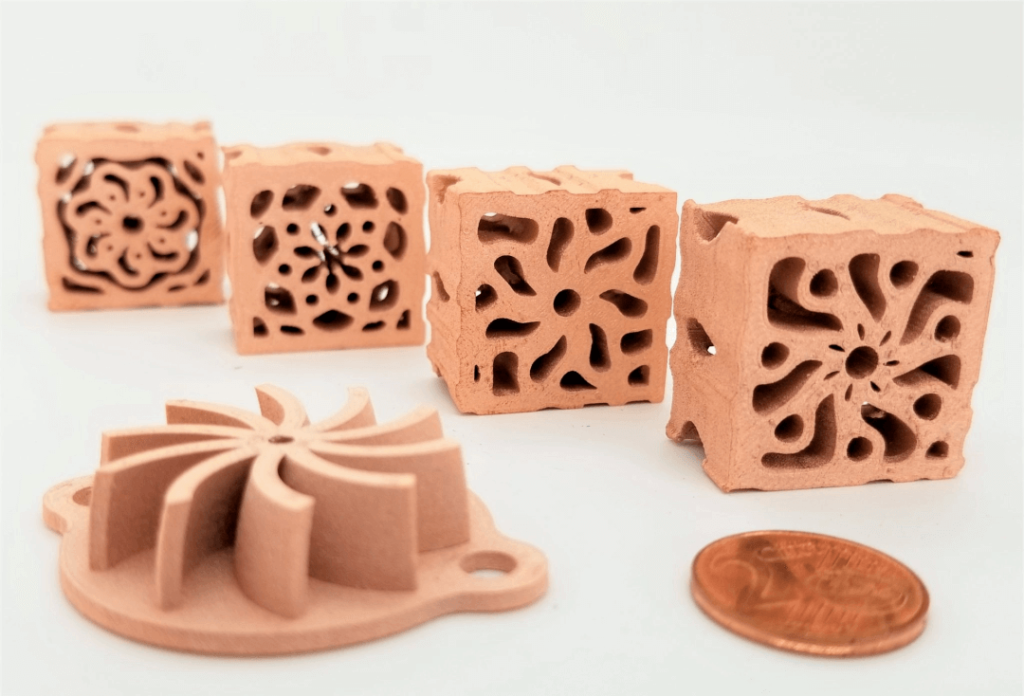
Bronze 3D Printing Service
Receive quick quotes for parts made from over 70 different metal and plastic materials. All orders comply with ISO 9001:2015, IATF 16949:2016 certifications. Availability may vary, and we cannot always guarantee this service at all times.
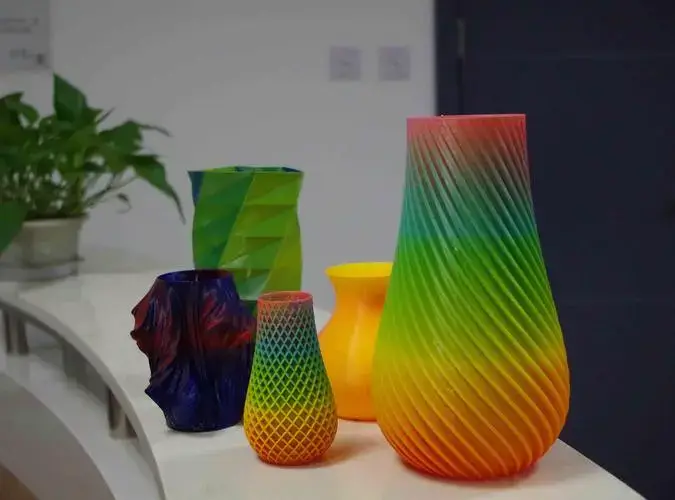
Color 3D Printing Service by Modo Rapid
Get instant quotes online for parts made from over 70 metal and plastic materials.
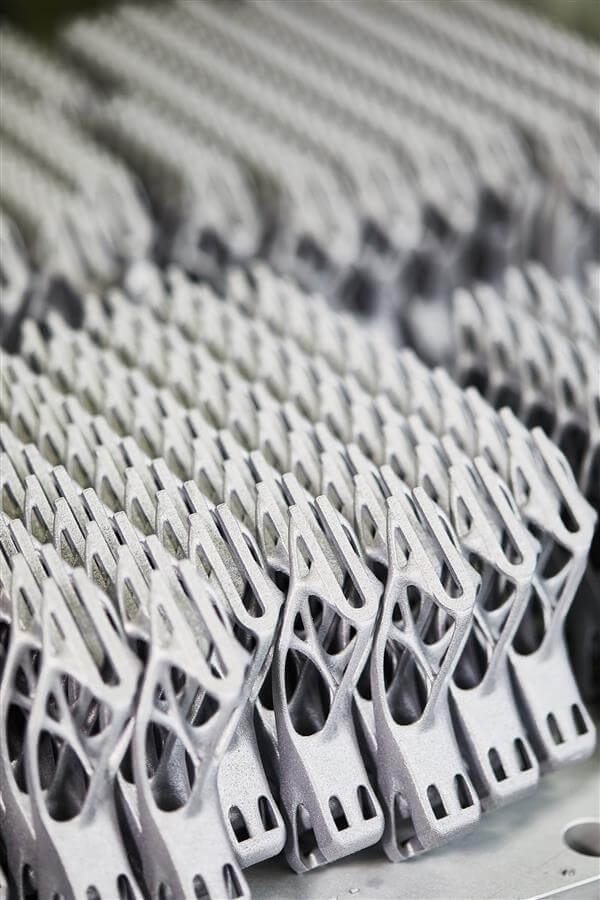
Large Scale 3D Printing Service
Get quotes for large-scale 3D printed parts, available in over 70 different metal and plastic materials.